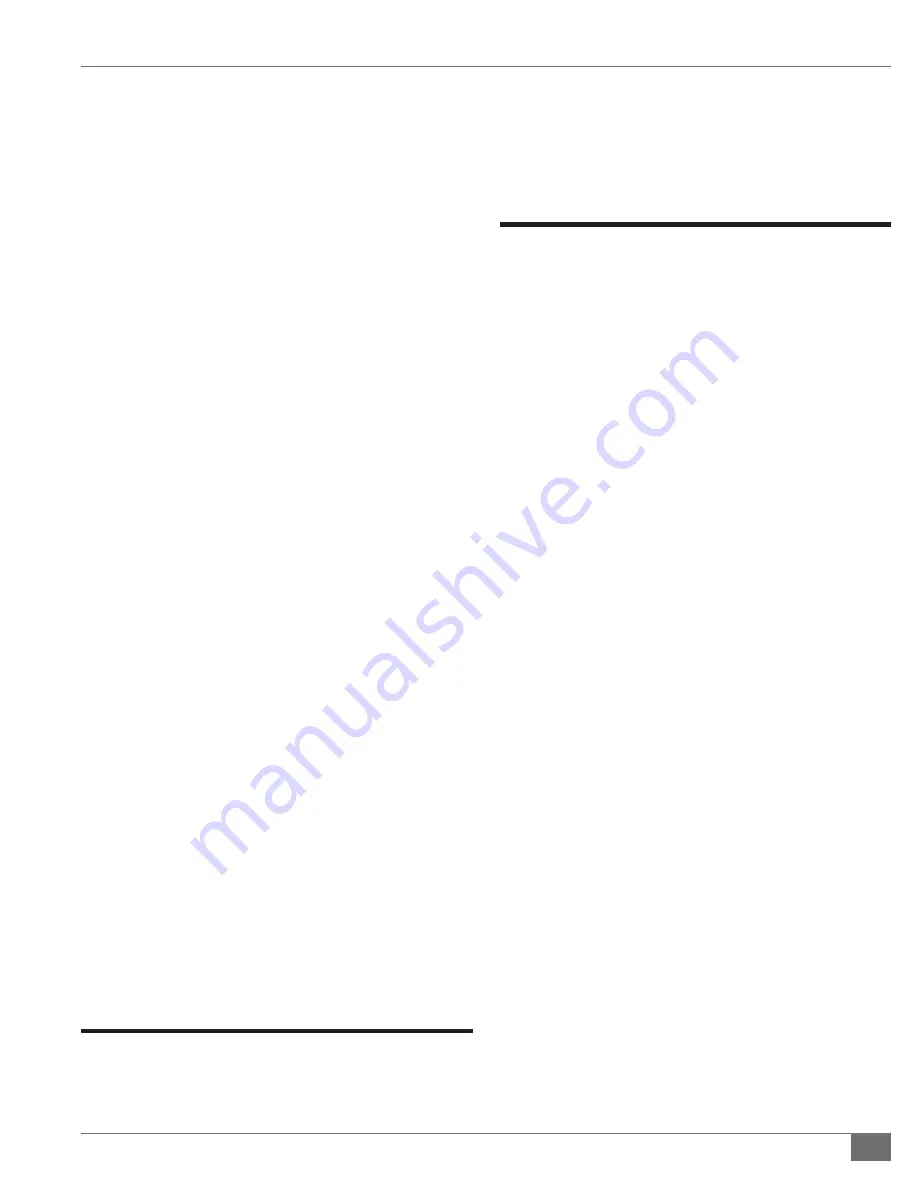
Questions? Please Contact Your Local Manufacturer’s Representative
SECTION 2
VSRT-IOM-2022-0728
INSTALLATION
2-49
Side Wall Vent Termination
Adhere to the following for installation (see
Figures 29, 31
):
NOTE:
The vent termination is joined to the vent pipe outside
the wall. Use the same joining procedures for vent pipe and
fittings.
1. When penetrating a non-combustible wall, the hole
through the wall must be large enough to maintain
the pitch of the vent and provide sealing. Use adhesive
material to seal around the vent on both sides of the
wall. When penetrating a combustible wall, a wall
thimble must be used. See
Figures 29, 31
for installation
instructions. Minimum wall thickness through which
vent system may be installed is 3.25 inches (8.26 cm).
Maximum wall thickness through which vent system
may be installed is 20 inches (50.8 cm).
2. The termination of the vent system must be at least 12
inches (30.48 cm)above the finished grade, or at least
12 inches (30.48 cm) above normal snow accumulation
level (for applicable geographical areas).
3. The termination of the vent system shall not be located
in traffic areas such as walk ways, adjacent buildings,
operable windows and building openings unless the
venting system is at least 7 ft (2.1 m) above finished
grade, (National Fuel Gas Code, ANSI Z223.1).
4. The vent terminations must be at least 4 ft (1.22 m)
horizontally from electric meters, gas meters, regulators,
and relief equipment.
5. When installing inlet and exhaust terminations on the
same wall, the exhaust outlet must be installed 4 feet
(1.22 m) minimum above and 10 feet (3.05 m) minimum
downwind from air supply inlet to prevent exhaust
recirculation.
6. Under certain wind conditions, some building materials
ma
y be affected by flue products expelled in close
proximity to unprotected surfaces. Sealing or shielding
of the exposed surfaces with a corrosion resistant
material (such as an aluminum sheet) may be required
to prevent staining or deterioration. Flue should be
directed away from surfaces, if possible.
System Piping Testing
Upon completion of the installation, adhere to the following
for system piping testing:
1. Perform a pressure test.
2. Perform soap tests at all welds and joints to ensure that
the system is free from leaks.
Assembly of Fulton Multi-Skid Systems
Adhere to the following for multi-skid engineered systems:
1. Refer to the Fulton mechanical/electrical drawings
during assembly.
2. Ensure that equipment orientation allows for operation
interface and maintenance.
3. Align the skids as shown on the drawings ensuring that
skid fasteners (skid joint angles) are matched. The skid
joint angles are a matched set and the edges of the
fasteners should be exactly aligned.
NOTE:
Do not bolt the skids to the housekeeping pad/floor
until all of the piping has been reassembled and tightened.
4. Ensure the skids are level and flat before fastening
the skids together with the supplied bolts. The skids
should be leveled front to back, side to side and corner
to corner. Failure to properly level the skids will result
in piping misalignment. A level or laser level should be
used to verify skid alignment (when a standard level is
used, the length should be appropriate for the skid). If
assembling multi-component support stands, attach
sections using the supplied bolts through the tank
frame mounting plates. These should be hand tight
until all of the piping is assembled.
NOTE:
Skids are leveled at the factory using a laser level.
5. Connect the piping between the skids by matching
the union connections and/or flange stamps and
tightening. Refer to the mechanical drawing as
necessary to confirm location of spool pieces etc. as the
flange stamps are shown on the drawing in hexagonal
callouts. The flange stamps should matched and
aligned (the flange stamps should be directly across
from one another. Rotating a flange will result in piping
misalignment). Bolts should be hand tight until all
of the piping is assembled. Refer to the appropriate
instructions to tighten the flanges to the required
torque specifications. Support pipe runs as required.
6. Ensure that a low point drain is installed in the piping.
7. Connect the conduit runs between the skids and
tighten conduit connectors.
8. Locate the supplied wiring for the equipment and pull