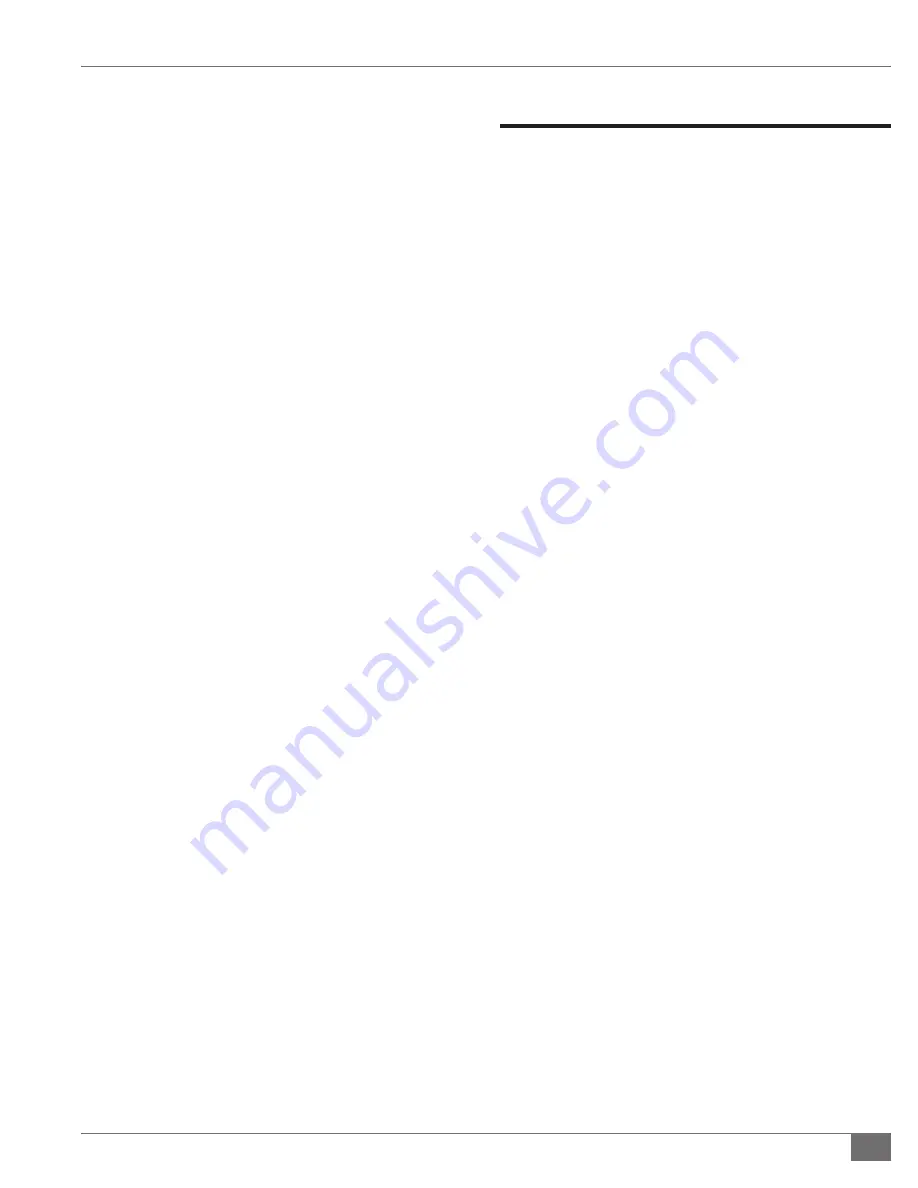
Questions? Please Contact Your Local Manufacturer’s Representative
SECTION 2
VSRT-IOM-2022-0728
INSTALLATION
2-45
3. Install the top fitting (the fitting without the drain port)
into the upper fitting on the water bottle using service
rated sealant. Wrench tighten the fitting until it is snug
and the glass outlet is pointing at about 5 o’clock (about
1/8 turn from its final downward vertical position).
4. Install the bottom fitting (the fitting with the drain port)
into the lower fitting on the water bottle. Wrench tighten
the fitting until it is snug and the glass outlet is pointing
directly upward.
5. Verify that the top and bottom fittings are threaded
into the water bottle tappings the same amount
(horizontally).
6. Remove the glass packing nut, friction washer and glass
packing from the fittings and place them in the same
order on either end of the water gauge glass. Push both
packings about 1in (25.4 mm) from the end of the water
gauge glass.
7. Gently insert one end of the water gauge glass into the
top gauge fitting. Keeping the glass inside the fitting,
gently rotate the top fitting clockwise until it is vertically
aligned with the bottom fitting.
It is crucial that the
gauge glass valves are aligned both vertically and
horizontally. If not aligned, they may leak.
8. Insert the gauge glass into the bottom fitting until it
bottoms out, and then gently raise glass about 1/16 in
(1.6 mm). Do not allow glass to remain in contact with
any metal surface.
9. Carefully slide the bottom glass packing down until
the glass packing is touching the lower gauge fitting.
Carefully slide the top glass packing up until the glass
packing is touching the upper gauge fitting.
10. Hand tighten both glass packing nuts, then tighten ½
turn more by wrench. Do not overtighten. If any leakage
occurs, tighten the packing nut slightly, no more than a
¼ turn at a time, until the leak stops.
11. When provided, install the protective guard over the
gauge glass assembly.
12. The gauge glass valves are fitted with ball checks. Make
sure that the valves are fully open to ensure that the ball
check will function properly in the event that the gauge
glass breaks.
13. Install drain piping from water bottle and lower water
gauge glass fitting to the boiler blo
w off piping.
Stack & Flue Connections
Adhere to the following for stack and flue connections:
1. An appropriately-sized stack should be connected to
the flue gas outlet at the boiler. The proper flue size
and draft control is most important for proper burner
operation. The flue must be as large or larger than the
outlet on the vessel. Avoid long flue piping and too
many elbows by placing the equipment as close as
possible to the chimney.
2. The stack should rise continuously to the connection
at the chimney and should contain no more than two
bends at 45 degree angles or less. If required, as a result
of space limitations, one 90 degree elbow (or tee) can be
fitted at the back of the vessel.
3. Any alternative stack arrangement must supply the
following draft:
VSRT must supply a draft condition of -0.25” w.c.
to + 1.50” w.c draft at the boiler.
Positive pressure draft requires a CAT 3 stack.
4. The run in the total distance of stack ducting, as
measured in a straight line from the outlet of the boiler
to the outlet of the stack, should not exceed 25% of
the rise. With the exception of the duct run previously
described, horizontal sections of ducting must be
avoided and should not exceed four feet total. See
Figures 28-29.
5. The stack and chimney material shall comply with all
applicable codes.
6. Adequate provision must be made for the support of
the weight of the chimney and stack to avoid having
a load imparted to the outlet connection of the
equipment.
7. The installation of a draft regulator by the client/
contractor is recommended at all installations. This will
help to maintain the required draft. The placement of
the draft regulator should be as shown in
Figures 28-29.