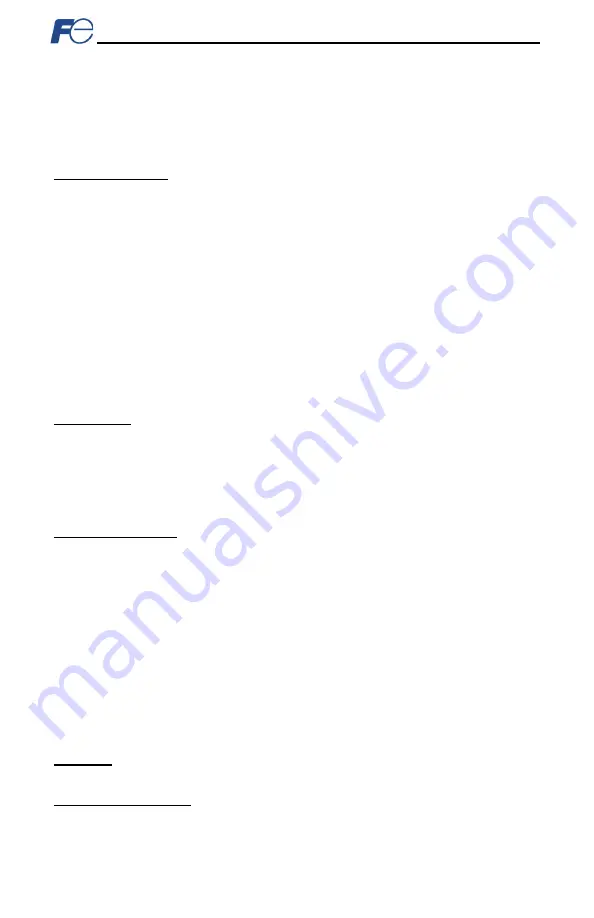
56
9.2.3 Connection Timeout Options
In the studio’s Project panel, navigate to
OPC-PRT…Ethernet…EtherNet/IP Server
. The following
configuration options will determine the actions to be taken if the connection is abnormally terminated or
lost. While this feature provides an additional level of fail-safe functionality for those applications that
require it, there are several ramifications that must be understood prior to enabling this capability. Note
that a certain degree of caution must be exercised when using the timeout feature to avoid “nuisance”
timeouts from occurring.
Run/Idle Flag Behavior
EtherNet/IP clients (such as PLCs) have the option of adding a 32-bit “run/idle” header to all class 1 (I/O)
data packets sent to devices. Bit 0 of this header is called the “run/idle flag” by the EtherNet/IP
specification, and is intended to signify when the client is in a “running” state or an “idle” state. A running
state (run/idle flag = Run) is indicated whenever the client is performing its normal processing (e.g.
scanning its ladder logic). An idle state (run/idle flag = Idle) is indicated otherwise. For example, Allen
Bradley ControlLogix PLCs will set their run/idle flag to Idle whenever their processor keyswitch is
placed in the “PROG” position, presumably in preparation to receive a new application program from
RSLogix 5000.
The behavior of EtherNet/IP devices when they receive I/O data from a controller with the run/idle flag
set to Idle is not defined in the EtherNet/IP specification. The driver allows the option of two different
behavioral responses when a run/idle flag = Idle condition is received, depending on the state of the
Invoke Timeout When Run/Idle Flag = Idle
checkbox.
•
If the checkbox is cleared (default setting), then the driver will maintain the last I/O data values
received from the client. For example, if a device mapped to the database was being commanded
to run prior to the run/idle flag being set to Idle by the client, then it will continue to run.
•
If the checkbox is checked, then the driver will perform the
Timeout Action
.
Timeout Action
Select an action from the drop down menu:
“None” ..................................No effect. The inverter will continue to operate with the last available
settings.
“Apply Fail-safe Values” .......Apply the fail-safe values as described in section 5.4.1.
“Fault Drive” .........................The behavior will depend on the timeout conditions set by the inverter
(function codes o27 and o28), which may result in an Er5 fault. Refer to
section 3.2.
Enable Drive Fault Reset
This will clear the Er5 fault once communication is re-established. This option is only available if the
Timeout Action
is set to “Fault Drive”.
9.2.4 Generic Class 1 I/O Produced and Consumed Data Settings
The Produced Data Word and Consumed Data Word objects are only applicable when connecting to
assembly instances 100 and 150 (generic I/O), which is typically the case. The Produced Data Word
defines the structure of status data sent from the inverter back to the controller (T->O, target to
originator). The Consumed Data Word objects will define the structure of the command data sent from
the EtherNet/IP controller (for example, a ControlLogix PLC) to the inverter (O->T, originator to target).
These objects allow the creation of custom-built I/O data. Up to 32 “command” function code values can
be sent to the inverter, and up to 32 “status” function code values can be sent back to the controller.
Therefore, up to 32 Produced and 32 Consumed Data Word objects can be created. If a consumed word
offset is not defined, that data will be ignored by the inverter. If a produce word offset is not defined, the
value will default to 0. The size of the actual I/O produced and consumed data is determined by the
client upon initial connection establishment. Since a data word utilizes 2 bytes, the size must be an even
number of bytes. The I/O data format is summarized in Table 20.
Description
This 32-character (max) field is strictly for user reference: it is not used at any time by the driver.
Produced Data Word Offset
The value from the associated inverter function code will populate this word offset of the produced data
that is to be sent to the client. It is recommend to start at word offset 0.