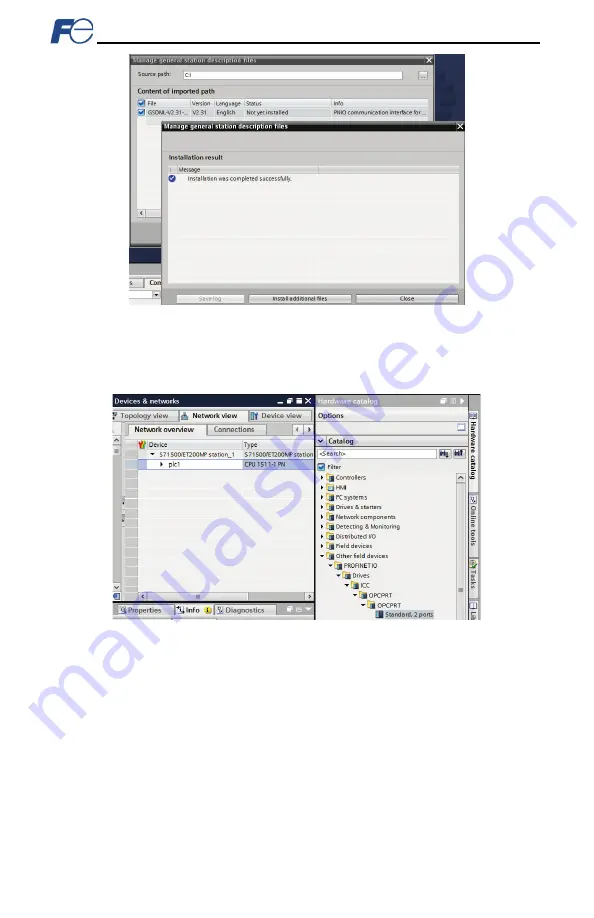
104
Figure 90: Successfully Installed GSDML File
This will update the
Hardware catalog
. Locate the device in the
Hardware catalog
. In the
Project tree,
double-click on
Device & networks.
Select the
Network view
tab and locate the device in the
Hardware catalog
as shown in Figure 91.
Figure 91: Updated Hardware Catalog