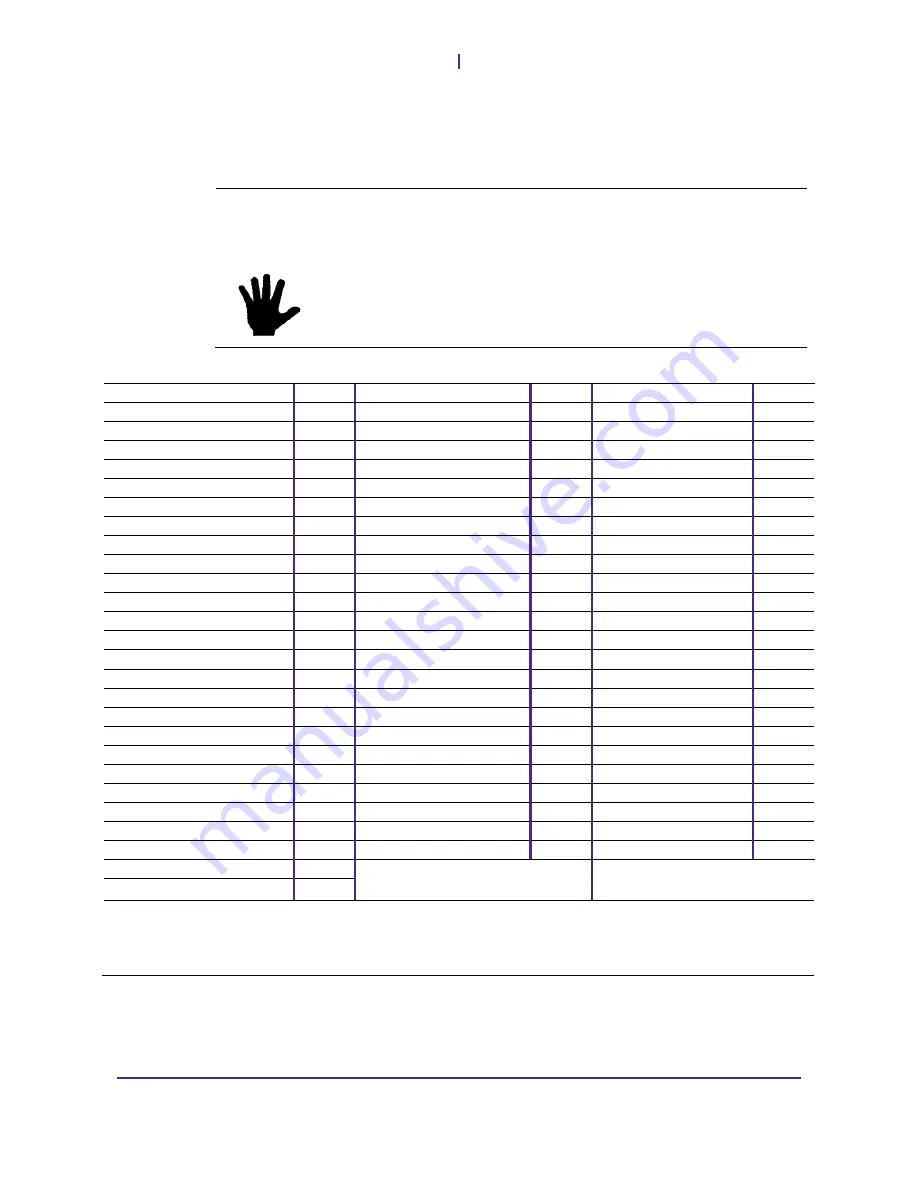
General Maintenance
FTS Systems LyoStar™ 3
58
Rev 006, 01/14
© SP Scientific 2014
Acrylic Parts
Clean acrylic parts with a mild detergent. Use a soft cloth or Kimwipes® to avoid
scratching the acrylic.
C
h
e
mical Resistance Chart
Chemical
Code
Chemical
Code
Chemical
Code
Acetic Acid (5%)
R
Ethyl Alcohol (50%)
LR
Nitric Acid (10%)
R
Acetic Acid (Glacial)
N
Ethyl Alcohol (95%)
N
Nitric Acid (40%)
LR
Acetic Anhydride
LR
Ethylene Dichloride
N
Nitric Acid (Conc.)
N
Acetone
N
Ethylene Glycol
R
Oleic Acid
R
Acetonitrile
N
2-Ethylhexyl Sebacate
R
Olive Oil
R
Ammonium Chloride (Saturated)
R
Formaldehyde (40%)
R
Phenol Solution (5%)
N
Ammonium Hydroxide (10%)
R
Gasoline (Regular, Leaded)
LR
Soap Solution (Ivory)
R
Ammonium Hydroxide (Conc.)
R
Glycerine
R
Sodium Carbonate (2%)
R
Aniline
N
Heptane
R
Sodium Carbonate (20%)
R
Battery Acid
R
Hexane (Commercial Grade)
R
Sodium Chloride (10%)
R
Benzene
N
Hydrochloric Acid
N
Sodium Hydroxide (1%)
R
Benzyl Alcohol
N
Hydrofluoric Acid (40%)
R
Sodium Hydroxide (10%)
R
Butyl Acetate
N
Hydrogen Peroxide (3%)
R
Sodium Hydroxide (60%)
R
Calcium Chloride (Sat.)
R
Hydrogen Peroxide (28%)
N
Sodium Hypochlorite (5%)
R
Calcium Hypochlorite
R
Isooctane
R
Sulfuric Acid (3%)
R
Carbon Tetrachloride
N
Isopropyl Alcohol
LR
Sulfuric Acid (30%)
R
Chloroform
N
Kerosene
R
Sulfuric Acid (Conc.)
N
Chromic Acid (40%)
N
Lacquer Thinner
N
Toluene
N
Citric Acid (10%)
R
Methyl Alcohol (50%)
LR
Transformer Oil
R
Cottonseed Oil (Edible)
R
Methyl Alcohol (100%)
N
Trichloroethylene
N
Detergent Solution (Heavy Duty)
R
Methyl Ethyl Ketone (MEK)
N
Turpentine
LR
Diesel Oil
R
Methylene Chloride
N
Water (Distilled)
R
Diethyl Ether
N
Mineral Oil
R
Xylene
N
Dimethyl Formamide
N
Naphtha (VM&P)
R
Trifluroacetic Acid
N
Dioctyl Phthalate
N
Ethyl Acetate
N
CODES
R = Resistant
(withstands long periods of exposure at temperatures up to 50 °C).
LR = Limited Resistance
(withstands short periods of exposure at room temperature).
N = Not Resistant
(immediate damage may occur upon exposure).
CAUTION! DO NOT USE ORGANIC SOLVENTS OR ABRASIVE CLEANERS.
Summary of Contents for LYOSTAR 3
Page 2: ......
Page 6: ...iv Rev 006 01 14 SP Scientific 2014...
Page 10: ...Contents FTS Systems LyoStar 3 viii Rev 006 01 14 SP Scientific 2014...
Page 18: ...Getting Started FTS Systems LyoStar 3 8 Rev 006 01 14 SP Scientific 2014...
Page 30: ...Operating your Lyophilizer FTS Systems LyoStar 3 20 Rev 006 01 14 SP Scientific 2014...
Page 36: ...Liquid Nitrogen Trap FTS Systems LyoStar 3 26 Rev 006 01 14 SP Scientific 2014...
Page 48: ...Sample Extractor Assemblies FTS Systems LyoStar 3 38 Rev 006 01 14 SP Scientific 2014...
Page 52: ...Stoppering FTS Systems LyoStar 3 42 Rev 006 01 14 SP Scientific 2014...
Page 56: ...Shelf Latching FTS Systems LyoStar 3 46 Rev 006 01 14 SP Scientific 2014...
Page 74: ...Appendix A Sample Recipe FTS Systems LyoStar 3 64 Rev 006 01 14 SP Scientific 2014...
Page 80: ...Appendix C Stainless Steel Cleaners FTS Systems LyoStar 3 70 Rev 006 01 14 SP Scientific 2014...
Page 81: ......