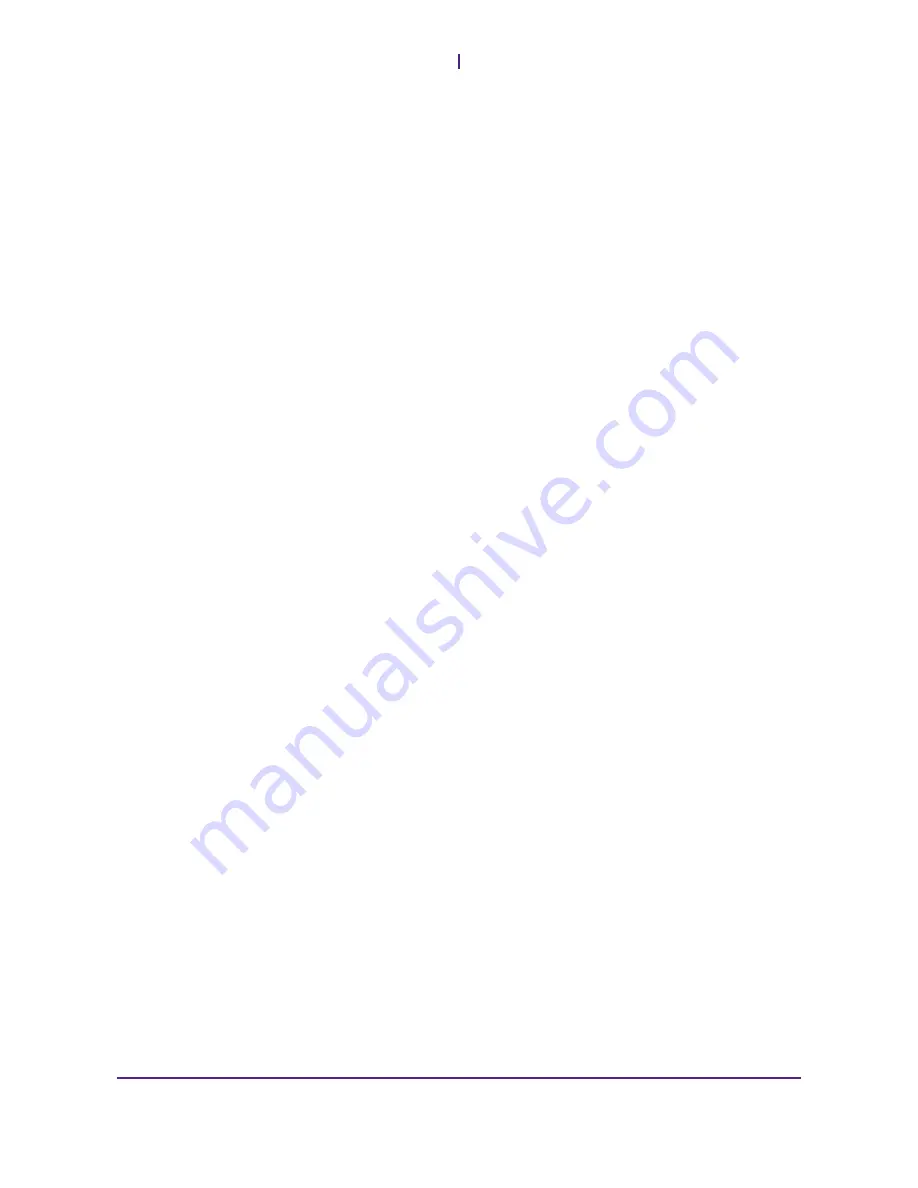
The Freeze-Drying System
FTS Systems LyoStar™ 3
14
Rev 006, 01/14
© SP Scientific 2014
Aeration and Vacuum Level Control
You may ‘break’ vacuum in the product and condenser chambers by aeration using
nitrogen, room air or other suitable gas. A single inert gas port, which is located on the
freeze dryer’s rear panel, is provided for vacuum release, vacuum level control and
backfill (
e.g.
, prior to stoppering). Room air or an inert gas supply is fed through a 0.2
micron sterile air filter to the product chamber during vacuum level control and backfill
processes, or to the condenser chamber during vacuum release. The valve used for
vacuum level control and backfill is located on the product chamber, while the valve
used for vacuum release is located on the condenser chamber.
Vacuum System
The purpose of the vacuum system is to provide vacuum and vacuum level control at
the setpoint required by the freeze-dry cycle. An adequately-sized two-stage rotary
vane vacuum pump is typically supplied with LyoStar™ 3 lyophilizers. The vacuum
system also includes an oil mist eliminator which traps or filters out oil mist created by
the vacuum pump before the mist is expelled into the ambient environment.
Vacuum Pump Exhaust
As vacuum pump vapors can be unpleasant in the lab and are not typically permitted
in a clean room environment, SP Scientific recommends installing an adequate
vacuum pump exhaust system. Vacuum pump exhaust piping should travel
horizontally from the pump across to a “T” equipped with a drainable trap and then 90
degrees vertically to an outside vent. Always place the drain trap as close to the pump
as possible. Exhaust lines should have an inside diameter no smaller than the
discharge of the pump. If you cannot exhaust directly outside the facility, a hood may
be used.
LyoS™ Control System
The LyoS™ Control System is designed to meet the lyophilization requirements of
pharmaceutical and biotechnology companies. The system is based on GE’s Proficy
HMI/SCADA iFIX solution for Windows® and utilizes an Allen-Bradley CompactLogix
programmable logic controller (PLC).
The GE Proficy operator interface is designed for ease of use as a Human-Machine
Interface (HMI), which presents process data to the operator and allows the operator
to monitor and control all process parameters. The iFIX SCADA engine is ideally
suited for process-driven applications, offering you faster, more intelligent control of
your lyophilization cycle and related functions. Installed on a Microsoft® Windows®-
based PC, the software provides visualization, data acquisition and supervisory
capabilities directly to the PLC. All process control is completed via the PLC.
Note: For more information, refer to your control system operator’s manual.
Programmable Logic Controller (PLC)
For every LyoStar™ 3 lyophilizer there is a Programmable Logic Controller (PLC)
running a computer program configured to that system. There is a set of master PLC
code, from which the PLC code for each individual project is derived.
Note: For more information, refer to your control system operator’s manual.
Summary of Contents for LYOSTAR 3
Page 2: ......
Page 6: ...iv Rev 006 01 14 SP Scientific 2014...
Page 10: ...Contents FTS Systems LyoStar 3 viii Rev 006 01 14 SP Scientific 2014...
Page 18: ...Getting Started FTS Systems LyoStar 3 8 Rev 006 01 14 SP Scientific 2014...
Page 30: ...Operating your Lyophilizer FTS Systems LyoStar 3 20 Rev 006 01 14 SP Scientific 2014...
Page 36: ...Liquid Nitrogen Trap FTS Systems LyoStar 3 26 Rev 006 01 14 SP Scientific 2014...
Page 48: ...Sample Extractor Assemblies FTS Systems LyoStar 3 38 Rev 006 01 14 SP Scientific 2014...
Page 52: ...Stoppering FTS Systems LyoStar 3 42 Rev 006 01 14 SP Scientific 2014...
Page 56: ...Shelf Latching FTS Systems LyoStar 3 46 Rev 006 01 14 SP Scientific 2014...
Page 74: ...Appendix A Sample Recipe FTS Systems LyoStar 3 64 Rev 006 01 14 SP Scientific 2014...
Page 80: ...Appendix C Stainless Steel Cleaners FTS Systems LyoStar 3 70 Rev 006 01 14 SP Scientific 2014...
Page 81: ......