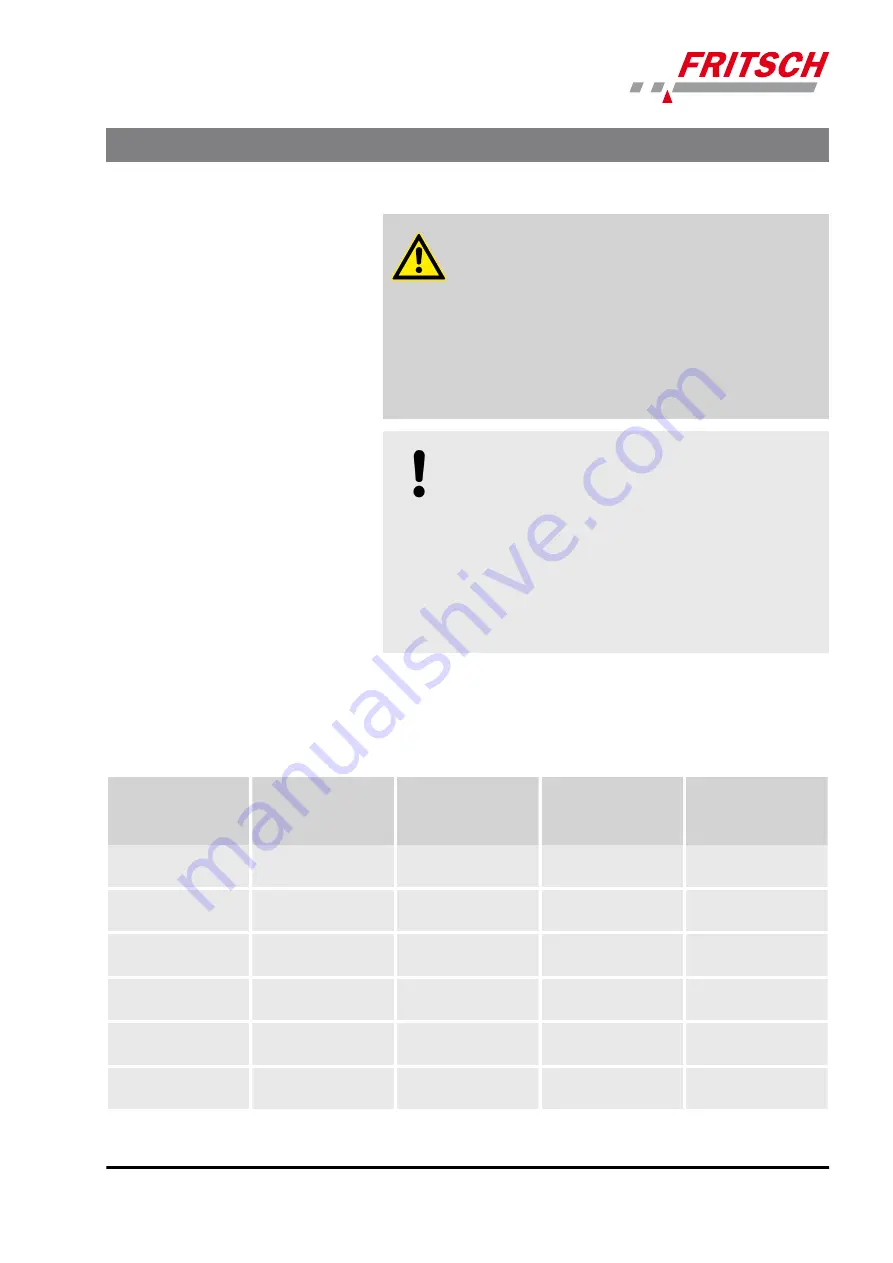
CAUTION!
The grinding element is subject to normal wear when
used. Before every grinding operation, check the wall
thickness of the grinding bowls. In the event of severe
wear, replace the grinding bowl. If this is not done, the
prevailing high centrifugal forces during grinding may
cause the grinding balls to penetrate the bowl's wall
and damage the mill. Failure to observe this will render
void the guarantee and release us from liability for any
resulting damage to the device or personal injury.
NOTICE!
Each grinding process means wear to the grinding ele-
ment. Therefore, please pay attention to what compo-
nents the material of the grinding element contains and
whether these could react with the sample. Such reac-
tions may have consequences. A simple reaction with
minor consequences may be, for example, the grinding
of samples containing sulphur in the steel bowl, which
contains iron. The iron released by abrasion can com-
bine with sulphur and react to form iron sulphide. This
can lead to black deposits on your grinding set.
The hardness and density (specific weight) of the grinding bowl and
grinding balls used have to be greater than that of the material used to
prevent excessive wear by abrasion.
Material
(bowl and balls)
Main components of
the material
Density in g/cm
3
High density means
high impact energy!
Abrasion resistance
Use for grinding
stock
Agate
(99.9% SiO
2
)
2.65
Good
Soft to medium-hard
samples
Silicon nitride
(90% Si
3
N
4
)
3.25
Extremely good
Abrasive samples,
metal-free grinding
Sintered corundum
(99.7% Al
2
O
3
)
3.9
Fairly good
Medium-hard,
fibrous samples
Zirconium oxide
(96.2% ZrO
2
)
5.7
Very good
Fibrous, abrasive
samples
Hardened, stainless
steel
(16.0 - 18.0% Cr)
7.7
Fairly good
Medium-hard, brittle
samples
Tungsten carbide
(93% WC+6% Co)
14.9
Very good
Hard, abrasive sam-
ples
Using the device
- 29 -