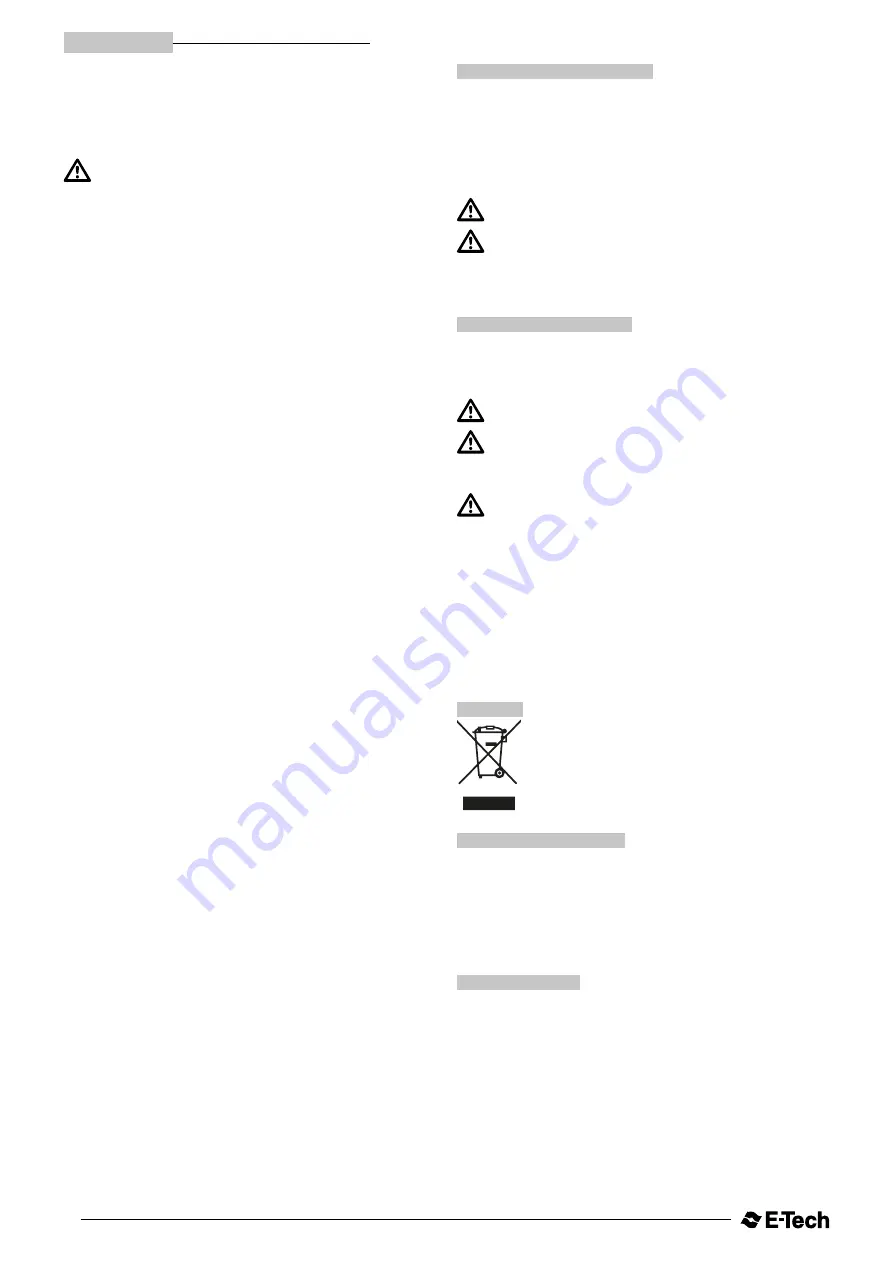
8
Translation of the original instructions
ENGLISH
CENTRIFUGAL PUMPS STANDARDISED IN ACCORDANCE WITH EN 733
6.1.1 Monobloc electric pumps
Lift the machine using a lifting lug, as shown in
Fig. A5
, if any. Alternatively, use a standard lifting
rope, looped around the machine as shown in the figure. In this use, the rope capacity is reduced by
20% compared to the rated one. Tighten the rope appropriately and make sure it cannot slip before
starting the lifting operations.
6.1.2 Electric pumps with rigid couplings
Lift the machine using the lifting lug located on the lantern connecting the pump and the motor, as
shown in
Fig. A5
.
Do not use the motor lifting lug to lift the whole frame
6.1.3 Base-mounted pump-motor units
A base should be provided with lifting lugs, with a load capacity that is suitable for the weight of the
pump,motor and base itself. Lift the machine by 4 suspension points.
6.1.4 Bare shaft pumps
Lift the pump (without motor) using a lifting lug, as shown in
Fig. A5
.
6.2 Positioning
Keep wall distances that do not interfere with the cooling air conveyance system. We recommend a
minimum distance of at least 30 cm on the fan cover side. Provide an unobstructed passageway on
the four sides of the machine to perform maintenance work.
6.3 Ground anchoring
Electric pumps and base-mounted pump-motor units must rest on a solid concrete foundation (
Fig.
A1
). The foundation must be adequately wider than the machine (at least 150 mm around the whole
perimeter). To reduce vibration, use one of the two suggested solutions.
If the pumped fluid temperature is significantly different from the room temperature, or if high
temperature variations are expected, install the product in such a way as to allow relative sliding of
its parts on the ground.
6.3.1 Flexible anchoring
To reduce vibration transmission through the foundation, it is recommended to install the machine on
flexible, low stiffness and medium to low damping supports. Use flexible supports with a minimum
deflection of at least 5 mm under the weight of the machine, or such as to guarantee less than 15 Hz
natural frequency, in relation to the machine mass. We recommend installing the machine on a mass
foundation at least twice (preferably 3 to 5 times) as large as that of the machine. Use appropriately
flexible piping sections at the inlet and outlet ports. To fasten the pump to the flexible supports,
observe the instructions of their manufacturer.
6.3.2 Rigid anchoring
The support feet or the base are rigidly anchored to the foundation by means of stud bolts or support
screws. Tighten them to prevent elements from being unscrewed due to vibrations; the load required
depends on the type of installation and anti-unscrewing solution used. Check the machine behaviour
during the running-in period on a regular basis.
The foundation must be independent of the surrounding flooring and rest on a low vibration
transmission sub-base. Create a heavy duty mass foundation (at least 3 times as large as that of the
pump, greater as the pump mass decreases and in any case heavier than 150 kg) above a soft, medium
to low damping sub-base. To evaluate the best solution, ask for an expert’s advice. Take the possibility
of increasing the foundation mass into account, if necessary.
6.4 Alignment of the pump-motor unit
6.4.1 Unit with flexible coupling
Mount-based pump-motor units, in which the motor and the pump are not rigidly connected and
there is a flexible drive coupling, require to be checked for alignment on site.
The check must be carried out before start-up, after mechanically installing and connecting the pipes,
and repeated during the running-in period on a regular basis.
PTo check for alignment, remove the coupling guards (detail I in
Fig. A2
). Disconnect the two parts
of the coupling (remove the connecting pins or the flexible elements, depending on the type). Use
a steel line or a level to check the two halves for proper alignment along the whole perimeter (
Fig.
A3
). Repeat the check in different positions. If necessary, the unit must be realigned by inserting
calibrated shims between the pump or motor feet and the base. Observe the instructions of the
coupling manufacturer about the maximum angular (A max in
Fig. A3
) and parallel (B max in
Fig. A3
)
misalignment values, as well as for clearance S. If no other indications are provided, typical values are
1° (A max), 0.2 mm (B max) and 4 mm (S) for smaller motors and up to 2°, 0.5 mm and 6 mm for larger
motors respectively. Greater limits can be accepted for more flexible couplings.
6.4.2 Unit with rigid coupling
The pump-motor units in which the hydraulic part is rigidly coupled to the motor do not require
further alignment operations. However, it is advisable to insert shims between the pump and/or
motor feet and the base in order to recover any clearance and avoid bending loads in the connection
between the two components.
6.5 Guards and protective barriers
6.5.1 Guards for bare shaft pumps
Bare shaft pumps purchased as single elements require guards to prevent accidental contact with
moving parts (detail I in
Fig. A2
). The guards must be made in such a way as to comply with at least
one of the following criteria (see
Fig. A4
):
1) The cracks present do not allow the passage of solids with a diameter greater than 12 mm.
2) If solids with a diameter of less than 30 mm can pass through the slots, active parts must be placed
at least 120 mm from the access point.
3) If solids larger than 30 mm can pass through the guards, the path to reach potentially dangerous
parts must be very curvy and at least 50 cm long.
Perform a check in all positions and from all possible directions. Pay particular attention to the open
sides and corners of the guards (see detail A in
Fig. A4
).
6.5.2 Additional guards and barriers
The assessment of the risks associated with the machine operation is based on an installation
assumption complying with statutory requirements, in a plant technical room with adequate
characteristics and accessed only by experienced, qualified personnel. If the installer deems it
necessary, we recommend installing additional guards. For example, if the machine is installed in a
common area, or an area that is accessed by unqualified personnel required to use it, it may be useful
to use barriers or guards preventing non-maintenance personnel from getting in contact with the
machine, without interfering with its normal functions (e.g. cooling of active parts).
6.6. Other requirements for bare shaft pumps
6.6.1. Motor choice
Bare shaft pumps are supplied without electric motors. For the selection of the electric motor, refer
to the data on the pump nameplate. Select the motor according to the mains voltage and frequency,
as well as the rotation speed (i.e. number of poles) and the power specified on the pump nameplate.
Do not overload the motor.
7 START-UP AND PROLONGED STOP
Before starting the electric pump, it is necessary to fill it and the suction pipe with water (the whole
circuit, if the plant is closed). If an electric pump with positive suction head is installed, perform the
following operations manually. Unscrew the filler cap (B in
Fig. A7
). Fill the pump up to the cap level
and close it again.
On the contrary, if a negative suction head system is installed, or the suction line is pressurised, it is
sufficient to open the valves, vent air (using the vent valves - the discharge valve if the circuit is open,
or filler cap B in
Fig. A7
) and wait for filling. In closed circuits, load the system from the highest point
and vent air at the same time.
During the first few seconds of operation, the pump will expel further air. If the circuit is closed, vent
it with appropriate valves.
Pay attention to leaks. Use appropriate PPE to protect against mechanical and chemical
risks.
Slowly open the valves during venting, avoiding sudden manoeuvres; do not direct the jet
towards people, animals or electrical appliances.
After prolonged downtime, check the pump for proper priming before starting it, and vent the pipes,
if necessary.
If a long downtime is expected and/or it is necessary to drain liquid from the machine, use the drain
plug at the bottom of the pump body (detail A in
Fig. A7
).
8 MAINTENANCE AND SUPPORT
The electric pump does not require special maintenance.
Have the electric pump repaired only by personnel authorised by the manufacturer so as to keep your
warranty valid and not to impair the safety of the appliance. Use only original spare parts or parts
approved by the manufacturer.
Always use the required PPE (refer to the relevant section).
Before starting any work on the electric pump, make sure it has been disconnected from the
power supply and cannot be accidentally reconnected.
Caution! In the event of an overload shutdown, appliances equipped with automatic reset
motor protection switches will automatically restart when the temperature drops below the
danger level.
It is advisable to check the condition of cables (especially at the cable glands) every month and clean
the filters and/or suction grille.
If the power cable is damaged, it must be replaced by qualified personnel.
Regularly check that no condensation is formed in the motor.
The components that are normally subject to wear are mechanical sealing devices and bearings if
any. Wear is associated with working conditions and workloads. Regular checks on the state of wear
and tear of these components will improve the reliability and increase the service life of the product.
Perform checks on a monthly basis, more frequently if the working conditions require to do so, and
during the first 500 hours of work.
• After cutting off the power supply, check the shaft passage area for any liquid leaks, these being
seal wear indicators.
• During normal operation, pay attention to any abnormal noises and/or vibrations from the
bearings, if any.
Check guards for proper positioning and safety devices for proper operation on a daily basis.
8.1 Spare parts
Use original spare parts or parts approved by the manufacturer, in order to avoid any risks to the
service personnel’s and users’ health. Contact the supplier and/or check the spare parts tables (see
technical catalogue) for information.
9 DISPOSAL
The devices marked with this symbol may not be disposed of in domestic waste
but disposed of in appropriate local collection centres for Waste Electrical and
Electronic Equipment (WEEE), or delivered to the distributor who is required to
collect them.
The product is not potentially dangerous for human health and the environment
as it does not contain any harmful substances pursuant to Directive 2011/65/EU
(RoHS), but if dispersed in the environment it will adversely impact the ecosystem.
The illegal or improper disposal of the product involves severe criminal and/or
administrative penalties.
10 EMERGENCY MANAGEMENT
10.1 Fire
• The only machine part exposed to a fire hazard is the motor. However, a fire hazard also exists for
materials unrelated to the machine but close to it.
• In the event of a fire, use extinguishers approved for electrical devices.
10.2 Liquid spills
• The pumped liquid may escape from the machine as a result of installation, start-up, maintenance
or disposal, unforeseen breakages or excessive wear of sealing devices.
• If spills can be dangerous or harmful to human, animal or environmental health, install a waterproof
collecting basin around the machine.
11 TROUBLESHOOTING
For the solution of problems related to the electric pump operation, follow the instructions in the table
below. If you do not have the necessary knowledge and skills, contact qualified personnel. Always use
PPE (see relevant section) and appropriate tools. If the problem cannot be solved by following the
instructions in the table, contact a professional, authorised service centre.
Summary of Contents for E-Tech FNC Series
Page 25: ...23 العربية والتركيب االستعمال دليل ...
Page 26: ...24 األصلية التعليمات ترجمة العربية ...
Page 27: ...25 العربية والتركيب االستعمال دليل ...
Page 69: ......
Page 70: ......
Page 71: ......