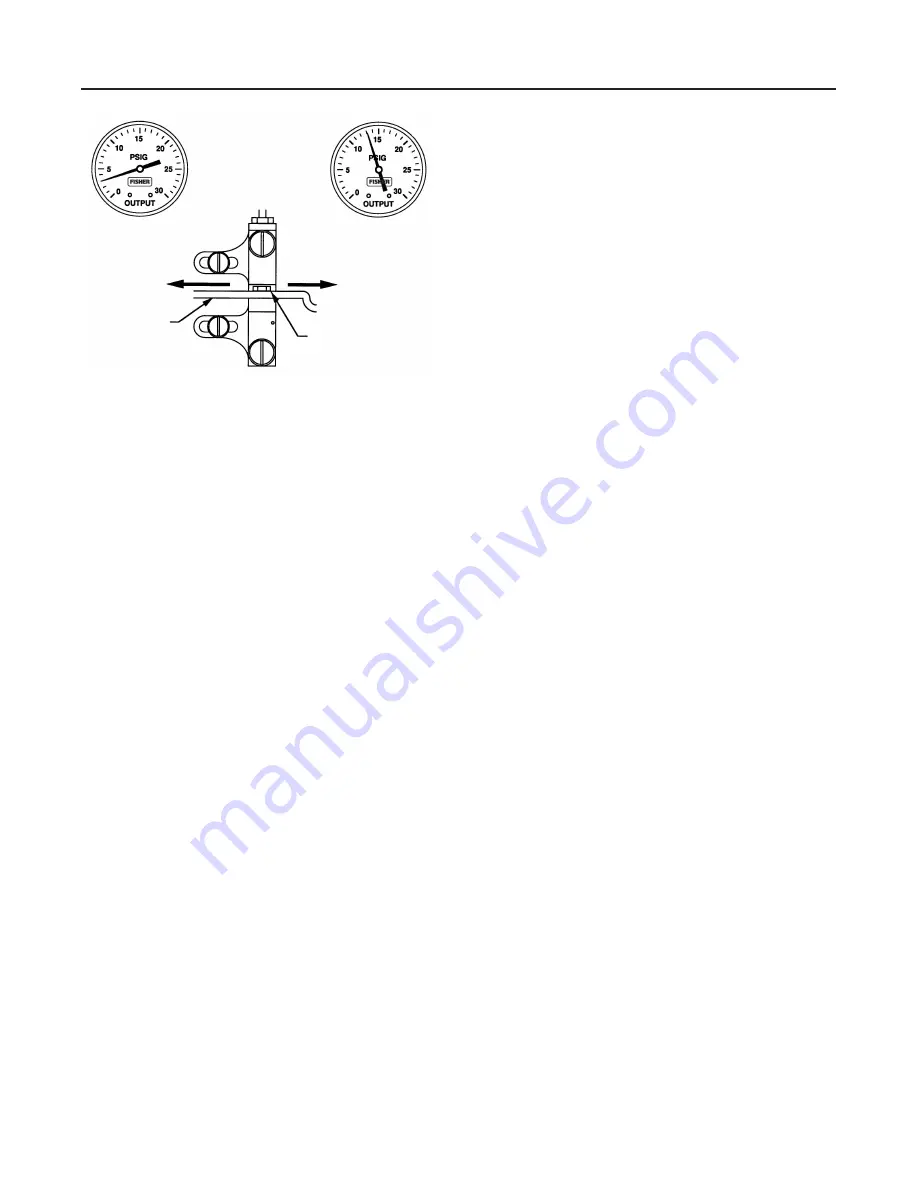
4150K and 4160K Series
13
Figure 9. Direct-Acting Controller Span Adjustment—
Proportional-Plus-Reset Controllers
IF OUTPUT IS:
BELOW
8 TO 10 PSIG
(0.6 TO 0.7 BAR)
ABOVE
8 TO 10 PSIG
(0.6 TO 0.7 BAR)
MOVE ADJUSTER
LEFT
MOVE ADJUSTER
RIGHT
FLAPPER
NOZZLE
NOTE:
3 TO 15 PSIG (0.1 TO 1.0 BAR) OUTPUT SHOWN.
FOR 6 TO 30 PSIG (0.2 TO 2.0 BAR) OUTPUT, ADJUST
VALUES AS APPROPRIATE.
A6154 / IL
screw. If the adjustment is repeated sev-
eral times, alternate the loosening of the
two screws to prevent the nozzle from
being misaligned with the flapper. Dur-
ing calibration, always be sure the
nozzle remains perpendicular to the
flapper.
11. If the output pressure is not between 8 and 10 psig,
adjust the controller span by loosening one of the two ad-
justing screws (key 43) and move the calibration adjuster
(key 41) a small distance as indicated in figure 9.
12. Repeat steps 6 through 11 until no further adjust-
ment is necessary.
13. For controllers with anti-reset windup (Type 4160KF
and 4162KF), remove the two machine screws, anti-re-
set windup cover, and two O-rings installed in step 1 of
this procedure. Install the anti-reset windup assembly
(key 186) with the arrow pointing in the direction re-
corded in step 1.
14. Proceed to the Startup procedures for proportional-
plus-reset controllers.
For reverse-acting controllers:
6. Apply an input pressure equal to the sensing element
upper range value.
7. Rotate the pressure setting knob to the maximum
value.
8. Adjust the nozzle (key 57) until the controller output
pressure is between 8 and 10 psig (0.6 and 0.7 bar).
9. Apply an input pressure equal to the sensing element
lower range value.
10. Rotate the pressure-setting knob to the minimum
value.
Note
When performing the span adjustment
in step 11, do not watch the output
gauge while changing the calibration
adjuster. The change in output is not a
good indication of the change in span.
While moving the calibration adjuster,
the output pressure may change in the
opposite direction than expected. For
example, while moving the calibration
adjustor to increase span, the output
pressure may decrease. This should be
disregarded since even though the out-
put pressure decreases, the span is in-
creasing.
Loosen one screw only on the calibra-
tion adjuster and move the calibration
adjuster a small amount using the tight
screw as a pivot and retighten the
screw. If the adjustment is repeated sev-
eral times, alternate the loosening of the
two screws to prevent the nozzle from
being misaligned with the flapper. Dur-
ing calibration, always be sure the
nozzle remains perpendicular to the
flapper.
11. If the output pressure is not between 8 and 10 psig,
adjust the controller span by loosening one of the two ad-
justing screws (key 43) and move the calibration adjuster
(key 41) a small distance as indicated in figure 10.
12. Repeat steps 6 through 11 until no further adjust-
ment is necessary.
13. For controllers with anti-reset windup (Type 4160KF
and 4162KF), remove the two machine screws, anti-re-
set windup cover, and two O-rings installed in step 1 of
this procedure. Install the anti-reset windup assembly
(key 186) with the arrow pointing in the direction re-
corded in step 1.
14. Proceed to the Startup procedures for proportional-
plus-reset controllers.