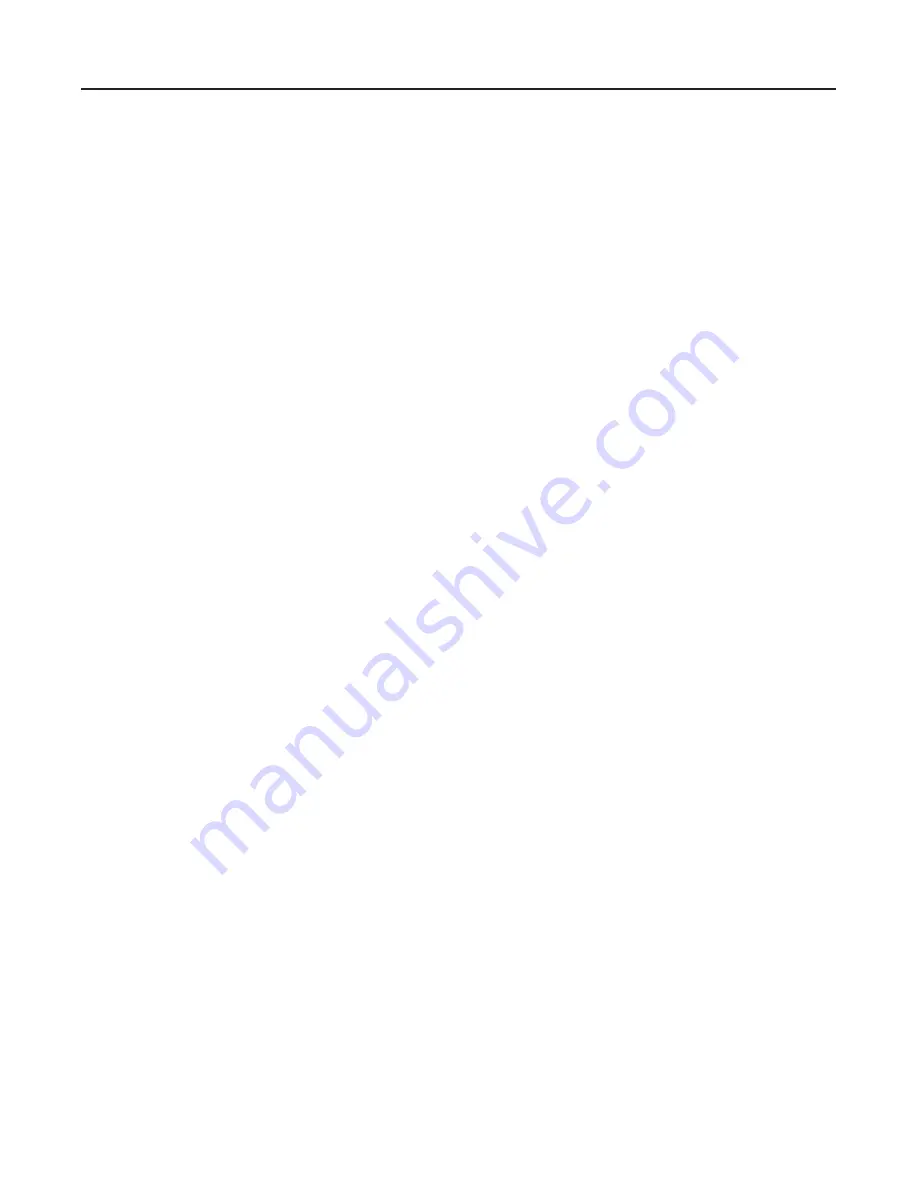
4150K and 4160K Series
25
3. Remove the casing screws (key 96), casing as-
sembly (key 85), and top diaphragm (key 91). On a
high-temperature relay, also remove the top gasket
(key 100) that covers the top diaphragm.
4. Remove the spacer ring (key 84), diaphragm as-
sembly (key 86), and relay spring (key 92) from the
relay body (key 83). On a high-temperature relay, also
remove the bottom gasket (key 99) from underneath
the diaphragm assembly.
5. Remove the screws (key 97), spring plate (key 95),
spring plate gasket (key 94), spring (key 93), and
valve plug (key 87).
6. Inspect the valve seats for roughness due to corro-
sion. One seat is located in the diaphragm assembly
(key 86), and the other seat is located in the relay
body (key 83).
Relay Assembly
1. Replace the diaphragm assembly or relay body if
necessary. Inspect the diaphragms and gaskets, and
replace them if necessary. Also replace the spring and
valve plug if they show signs of corrosion. The lower
diaphragm is part of the diaphragm assembly and
must be replaced as an assembly. Clean all parts thor-
oughly before re-assembling.
2. Place the relay spring in the relay body and, on a
high-temperature relay, install a bottom gasket. Install
the diaphragm assembly, spacer ring, and top dia-
phragm on the body so that all flow passage holes are
lined up. On a high-temperature relay, also install a
gasket over the top diaphragm.
3. Put the casing assembly on the top diaphragm so
that the lugs on the casing and spacer ring line up and
are also lined up with the body lug.
4. Install the casing screws, but do not tighten.
5. If using an optional alignment tool (figure 17), insert
the smaller end of the tool into the opening in the relay
body. If the tool does not engage the hole in the dia-
phragm assembly, move the relay parts slightly to re-
position the diaphragm assembly so that the alignment
tool engages the hole in the diaphragm assembly. Do
not remove the alignment tool until the casing screws
have been tightened.
6. Tighten the casing screws (key 96) evenly. Re-
move the alignment tool if one was used.
7. Install the valve plug, spring, gasket, and cover
plate (keys 87, 93, 94, and 95). Secure with the ma-
chine screws (key 97).
8. Install the O-ring (key 90) on the orifice assembly
(key 88), and install the orifice assembly into the relay
casing.
9. Install the relay as described in steps 7 and 8 in the
relay replacement section.
Changing Output Signal Range
Use the following information and subsequent proce-
dures when changing the output signal range of the
controller or transmitter. Use the following procedure:
D
For a controller or transmitter, use this proce-
dure to change from a 3 to 15 psig (0.2 to 1.0 bar) to a
6 to 30 psig (0.4 to 2.0 bar) output signal range or vice
versa.
D
For a differential gap controller, use this pro-
cedure to change from a 0 and 20 psig (0 and 1.0 bar)
to a 0 and 35 psig (0 and 2.4 bar) output signal range
or vice versa.
D
When changing the supply pressure source to a
new range, refer to table 5 for supply pressure require-
ments for the output signal range selected.
Also, make appropriate changes to the nameplate of
the controller or transmitter, reflecting the new range
selections. Refer to figure 21 or 22 for key number
locations unless otherwise directed.
1. Shut off the supply pressure and process lines to
the controller or transmitter.
2. Disconnect the tubing from the mounting base (key
30) and calibration adjuster (key 41). Disconnect the
tubing that connects the pressure block (key 8, figure
19 or 20) to the Bourdon tube or bellows assembly
(key 62 or 71), at the pressure block end.
3. Unscrew the machine screws (key 28, figure 19 or
20), and remove the subassembly from the case.
4. If the controller or transmitter uses a Bourdon tube
sensing element, disconnect the Bourdon tube from
the beam (key 44) by removing the screw (key 63). Be
careful to avoid losing the bearing (key 65). Unscrew
the machine screws (key 77), and remove the wash-
ers and Bourdon tube (keys 76 and 62).
5. Unscrew the bellows screws (key 54) from each
end of the mounting base (key 30). [Note: The bellows
screws (key 54) have an O-ring (key 55, figure 18)
installed beneath the bellows screw head. Remove the
O-ring and obtain a replacement when re-assembling
the bellows.]
6. Compress the bellows so that the end of the bel-
lows and beam can be removed from the end of the
mounting base (key 30) and unscrewed from the stud
(key 51, not shown) that connects the bellows.
7. With the stud that connects the two bellows in
place in the spacer (key 50), screw the new bellows
onto the stud. Install new gaskets (key 53) on each
bellows.