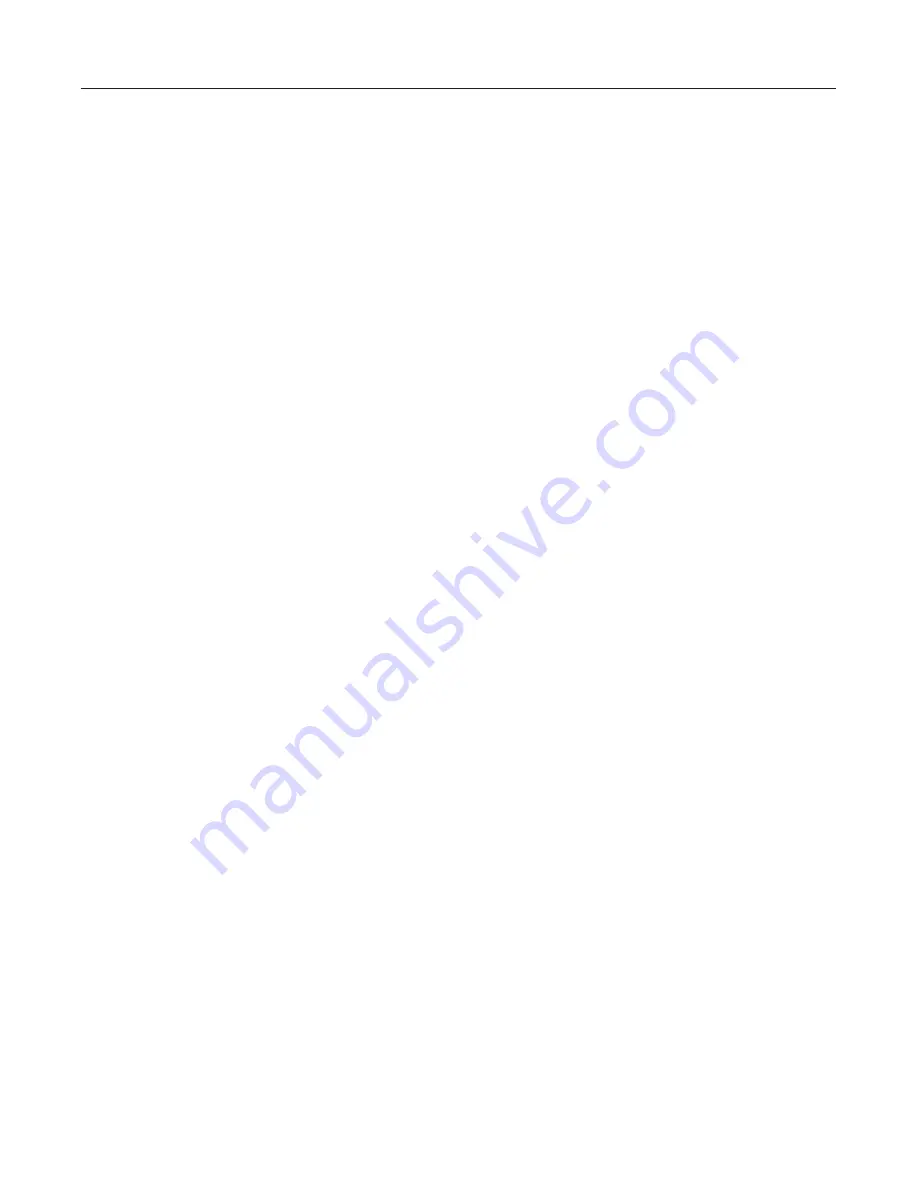
4150K and 4160K Series
12
The proportional band adjustment determines the
amount of change in controlled pressure required to
cause the control valve to stroke fully. It may be ad-
justed from 3–100 percent of the nominal sensing ele-
ment pressure rating.
Adjustment: Reset
To adjust reset action turn the knob clockwise to de-
crease the minutes per repeat. Turn the knob counter-
clockwise to increase the minutes per repeat. Increas-
ing the minutes per repeat provides a slower reset
action.
The reset adjustment dial is calibrated in minutes per
repeat. By definition, this is the time in minutes re-
quired for the reset action to produce an output
change which is equal to the change produced by pro-
portional control action. This is in effect, the time in
minutes required for the controller to increase (or de-
crease) its output pressure by an amount equal to a
proportional increase (or decrease) caused by a
change in set point or process pressure.
Adjustment: Anti-Reset Windup
The externally mounted differential relief valve can be
mounted to relieve on increasing or decreasing output
pressure.
Calibration
Calibration: Proportional-Plus-Reset Controllers
Unless otherwise indicated, key number locations are
shown in figure 8.
Before starting this procedure:
D
Provide a process pressure source capable of
simulating the process pressure range of the control-
ler.
D
If an output pressure gauge is not provided,
install a suitable pressure gauge for calibration pur-
poses. The controller must be connected open loop
(Open loop: The controller output pressure changes
must be dead ended into a pressure gauge).
Note
Type 4160KF and 4162KF (anti-reset
windup) controllers are supplied with
two O-rings (key 367, not shown), an
anti-reset windup cover (key 369, not
shown), and two machine screws (key
368, not shown). Use these parts in the
next step.
1. For controllers with anti-reset windup (Type
4160KF and 4162KF), record the direction of the ar-
row on the anti-reset windup assembly (key 186, in
figure 20). Remove the assembly and install the two
O-rings (key 367, not shown), and cover (key 369, not
shown) supplied with the controller. Secure the cover
with the two machine screws (key 368, not shown)
provided.
2. Connect regulated supply pressure to the control-
ler. Do not exceed the normal operating pressure in
table 5.
3. Rotate the reset knob to 0.01 minutes per repeat
(fastest setting).
4. Rotate the proportional band knob to 1.5 (15 per-
cent proportional band).
5. Verify that the calibration adjuster screws (key 43)
are at mid-position in the calibration adjuster (key 41)
slots.
Depending upon the controller action, perform one or
the other of the following procedures.
For direct-acting controllers:
6. Apply an input pressure equal to the sensing element
lower range value.
7. Rotate the pressure setting knob to the minimum val-
ue.
8. Adjust the nozzle (key 57) until the controller output
pressure is between 8 and 10 psig (0.6 and 0.7 bar).
9. Apply an input pressure equal to the sensing element
upper range value.
10. Rotate the pressure-setting knob to the maximum
value.
Note
When performing the span adjustment
in step 11, do not watch the output
gauge while changing the calibration
adjuster. The change in output is not a
good indication of the change in span.
While moving the calibration adjuster,
the output pressure may change in the
opposite direction than expected. For
example, while moving the calibration
adjustor to increase span, the output
pressure may decrease. This should be
disregarded since even though the out-
put pressure decreases, the span is in-
creasing.
Loosen one screw only on the calibra-
tion adjuster and move the calibration
adjuster a small amount using the tight
screw as a pivot and retighten the