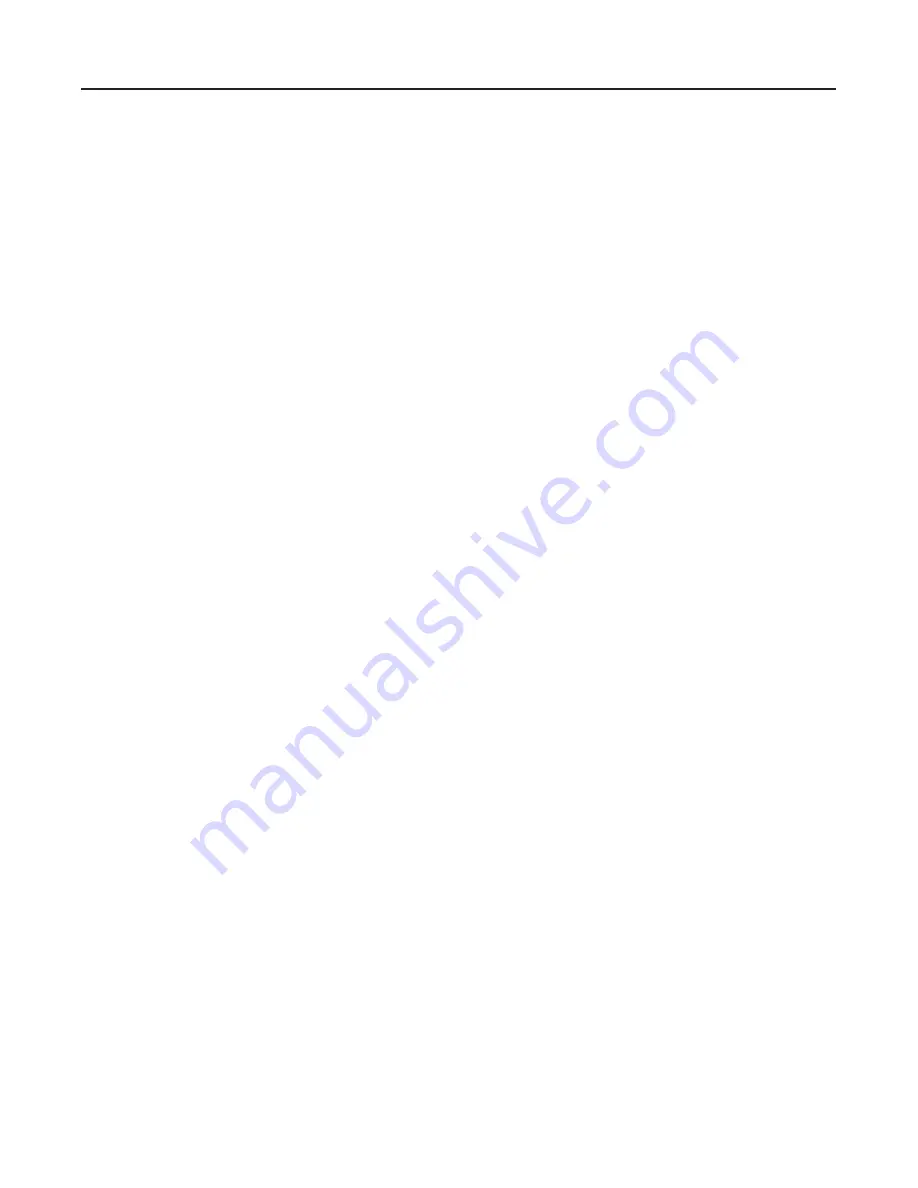
4150K and 4160K Series
9
the adjustments and calibration procedures are com-
plete, close and latch the cover.
To better understand the adjustments and overall op-
eration of the controller, refer to the Principle of Op-
eration section in this manual for proportional-only
controllers. Refer also to the schematic diagram in
figure 14.
Adjustments
Adjustment: Set Point
Adjust the pressure-setting knob by turning the knob
clockwise to increase the set point and counterclock-
wise to decrease the set point. Note: The dial setting
and actual process pressure may vary significantly,
especially with a wide proportional band setting.
Adjustment: Proportional Band
To adjust the proportional band, rotate the proportional
band knob to the desired value.
The proportional band adjustment determines the
amount of change in controlled pressure required to
cause the control valve to stroke fully. It may be ad-
justed from 3–100 percent of the nominal sensing ele-
ment pressure rating.
Calibration: Proportional-Only Controllers
Unless otherwise indicated, key number locations are
shown in figure 5.
Provide a process pressure source capable of simulat-
ing the process pressure range of the controller. If an
output pressure gauge is not provided, install a suit-
able pressure gauge for calibration purposes.
Connect a pressure source to the supply pressure reg-
ulator and be sure the regulator is delivering the cor-
rect supply pressure to the controller. The controller
must be connected open loop (Open loop: The control-
ler output pressure changes must be dead ended into
a pressure gauge). The following procedures use a 3
to 15 psig (0.2 to 1.0 bar) output pressure range as an
example. For a 6 to 30 psig (0.4 to 2.0 bar) output
range, adjust the values as appropriate.
1. Complete the above connections and provide a pro-
cess pressure equal to the sensing element range.
2. Rotate the proportional band knob, shown in figure 5,
to 1.5 (15 percent proportional band).
3. Verify that the calibration adjuster screws (key 43) are
at mid-position in the calibration adjuster (key 41) slots.
Depending upon the controller action, perform one or
the other of the following procedures.
For direct-acting controllers:
4. Apply an input pressure equal to the sensing element
lower range value.
5. Rotate the pressure setting knob to the minimum
value.
6. Adjust the nozzle (key 57) until the controller output
pressure is between 8 and 10 psig (0.6 and 0.7 bar).
7. Apply an input pressure equal to the sensing element
upper range value.
8. Rotate the pressure-setting knob to the maximum
value.
Note
When performing the span adjustment
in step 9, do not watch the output gauge
while changing the calibration adjuster.
The change in output is not a good in-
dication of the change in span. While
moving the calibration adjuster, the out-
put pressure may change in the oppo-
site direction than expected. For exam-
ple, while moving the calibration
adjustor to increase span, the output
pressure may decrease. This should be
disregarded since even though the out-
put pressure decreases, the span is in-
creasing .
Loosen one screw only on the calibra-
tion adjuster and move the calibration
adjuster a small amount using the tight
screw as a pivot and retighten the
screw. If the adjustment is repeated sev-
eral times, alternate the loosening of the
two screws to prevent the nozzle from
being misaligned with the flapper. Dur-
ing calibration, always be sure the
nozzle remains perpendicular to the
flapper.
9. If the output is not between 8 and 10 psig, adjust the
controller span by loosening one of the two adjusting
screws (key 43) and move the calibration adjuster (key
41) a small distance as indicated in figure 6.
10. Repeat steps 4 through 9 until no further adjustment
is necessary.
11. Proceed to the startup procedure for proportional
controllers.
For reverse-acting controllers:
4. Apply an input pressure equal to the sensing element
upper range value.