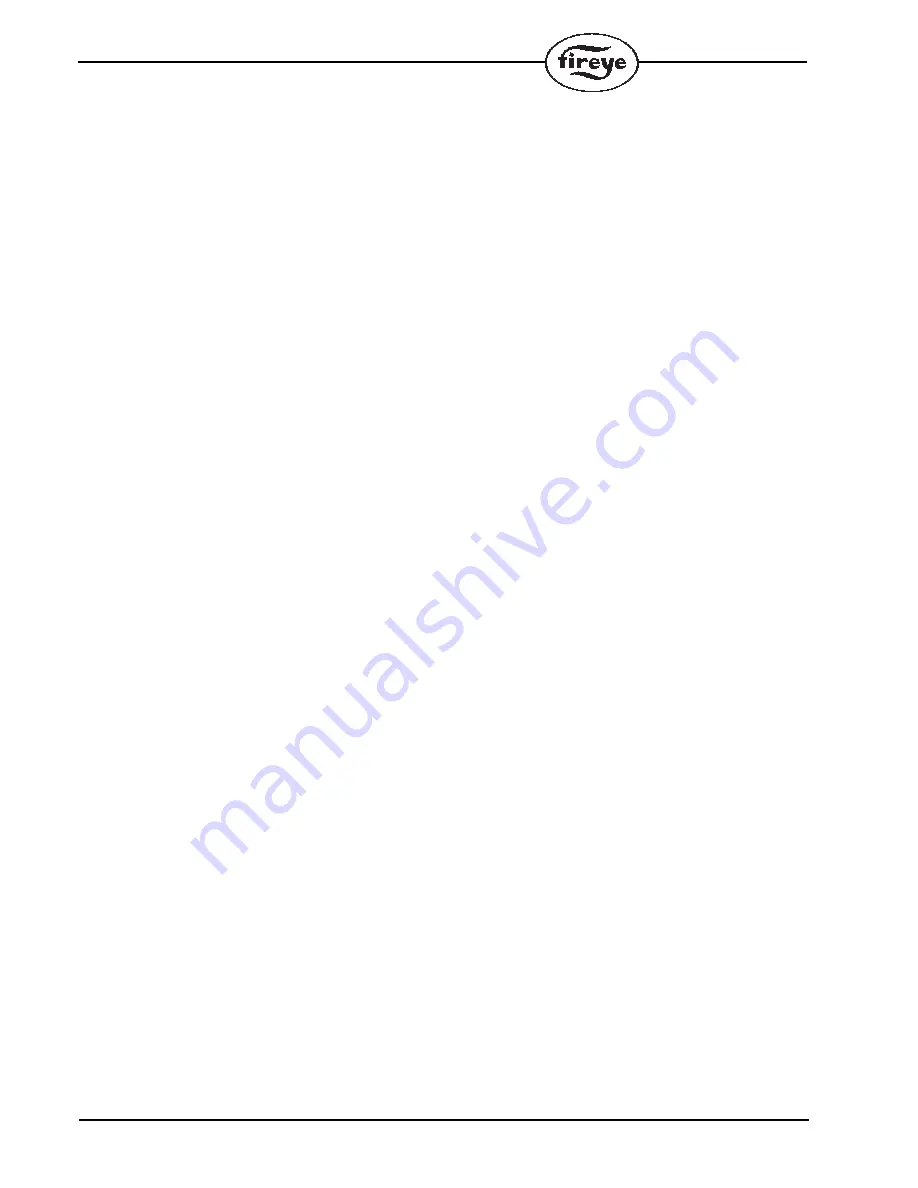
48
Description of control method
During start up of the burner and before the drives move to purge, the Nexus PPC5000 fuel air ratio
control system moves all motors to their minimum positions and outputs a current of 4mA to each
inverter drive. The unit waits for the inverter stop time (option 22.4), and then monitors the feedback
signals of all drives and compares them to the values which were stored in memory at commission
time. If the values do not match the ones in memory, a positioning fault is given and the unit per-
forms a safety shutdown.
If the test is successful, the unit moves all motors to their maximum positions and outputs a current
of 20mA to each inverter drive. As the drives’ feedback signals increase, the response time of each
drive is measured for later use in the control algorithm during modulation. Once the drives’ feedback
signals have stopped changing, the unit again performs a comparison with the values that were stored
in memory at commission time. If the values do not match those in memory, a positioning fault is
given and the unit performs a safety shutdown.
These tests prove the control circuit to the inverter and help to guard against control parameters
being changed on the inverter, which may affect the safety of the burner.
If the inverter is not performing correctly, start-up may be unreliable (See section 7).
Setting up the inverter for use with the Nexus PPC5000 fuel air ratio control system
The Nexus PPC5000 fuel air ratio control system will work with most inverters which meet the fol-
lowing criteria:
•
4-20mA speed reference input
•
4-20mA speed feedback output
•
Remote run/stop command
•
Fault relay for internal (inverter) and external (motor) faults
•
Speed reference and feedback signals must be isolated from each other unless a resistor greater
than the inverter input resistance is fitted in the feedback signal line.
Analogue inputs and outputs:
The analogue inputs and outputs (i.e. the 4-20mA reference and feedback signals) on the inverter
should be configured in the following way:
•
4-20mA signal (this may be an option parameter and/or a board jumper)
•
Speed reference input
•
Speed reference output
•
Minimum frequency 0Hz for 4mA signal
•
Maximum reference frequency as required (nominally 60Hz) for 20mA signal
•
Maximum feedback frequency same as reference for 20mA signal
•
No filtering (time constant = 0.0) and no rate limiting
Digital inputs and outputs:
The digital inputs and outputs (i.e. the RUN/STOP and FAULT signals) on the inverter should be
configured in the following way:
•
RUN/STOP from external input (NOT inverter keyboard)
•
RUN/STOP active high (i.e. energize to start)
•
FAULT relay set for internal inverter fault or motor over temperature/current
•
FAULT relay energized during normal operation (i.e. loss of power breaks circuit)
Control characteristics:
•
The control characteristics of the inverter should be configured in the following way:
•
Acceleration and deceleration time approximately 25 - 40 seconds, must be the same
•
Straight line (linear) acceleration between reference points
•
Motor to coast to a stop when RUN signal is removed
•
No critical frequencies
•
DC braking may be needed if motor deceleration is not linear