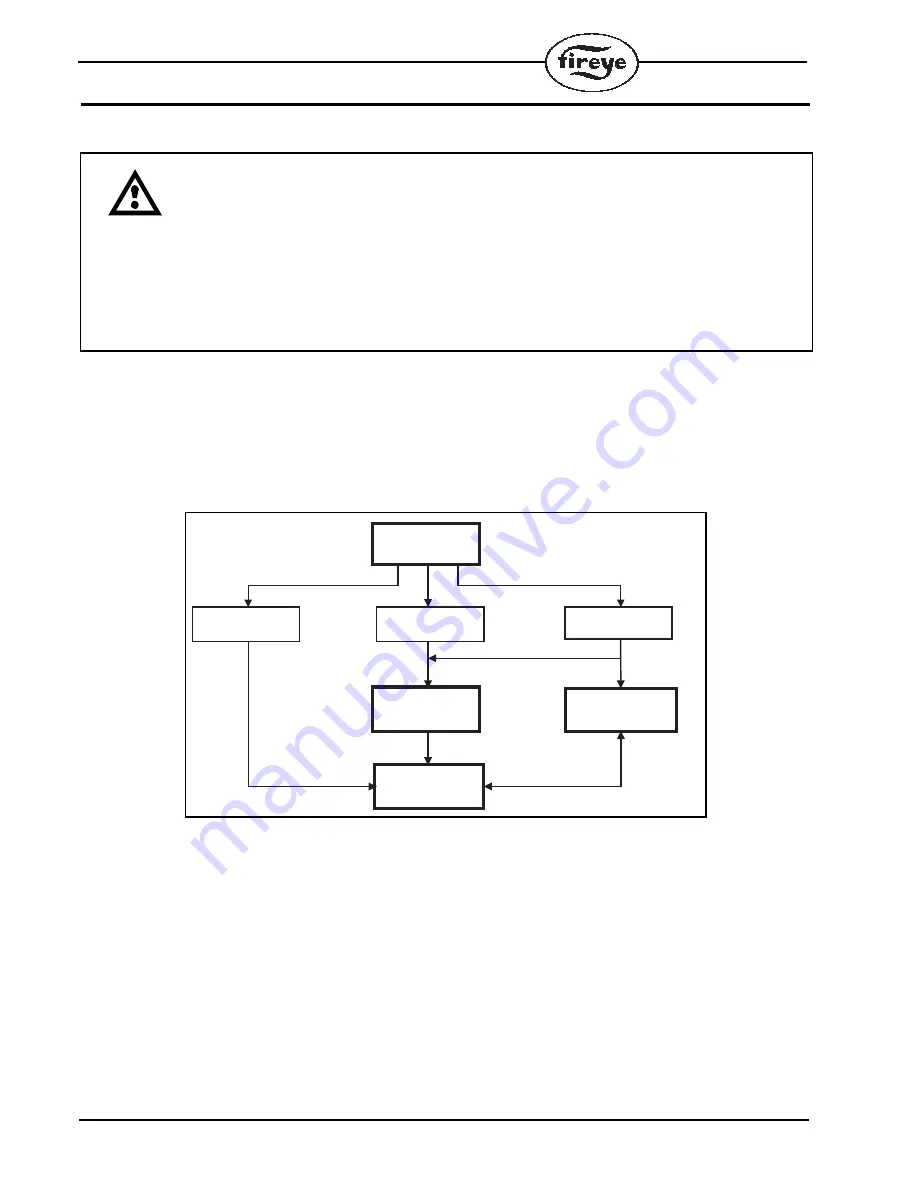
26
OPERATION IN THE COMMISIONING MODE
WARNING: While the unit is operating in commissioning mode or adjust ratio mode cer-
tain safety checks cannot be performed by the Fireye Nexus PPC5000 Fuel Air Ratio Con-
troller and therefore the safety of the system operation is the sole responsibility of the
commissioning engineer.
Do not allow fuel to accumulate in the combustion chamber. If fuel is allowed to enter the
chamber for longer than a few seconds without igniting, an explosive mixture could result.
It is recommended that you refer to the burner controller equipment manual to which this
unit is connected for recommendations concerning flame failure at ignition or any other
position.
If any settings in the unit are to be changed, it is necessary to enter a commission mode. Three pass-
codes are available for this purpose.
•
Supplier passcode
- allows entry to all commissioning modes.
•
Adjust ratio passcode
- allows adjustment of some option parameters and entry to adjust ratio
mode.
•
Site passcode
- allows adjustment of some option parameters.
Commissioning Data
Option Parameters
Option parameters contain information about the configuration of the burner and the boiler. Option
parameters may be adjusted in option set mode, but it may not be possible to adjust all of them if the
burner is on.
Setpoints
Setpoints contain information about required motor positions. Extra setpoints will become available
when option cards are inserted.
There are seven tables of setpoints (or seven profiles), each of which may be visualized using the fol-
lowing diagram:
RUN
MODE
ADJUST RATIO
PASSCODE
SUPPLIER
PASSCODE
SITE
PASSCODE
BURNER ON
BURNER OFF
ADJUST
RATIO MODE
COMMISSION
RATIO MODE
COM KEY
OPTION SET
MODE
COM KEY