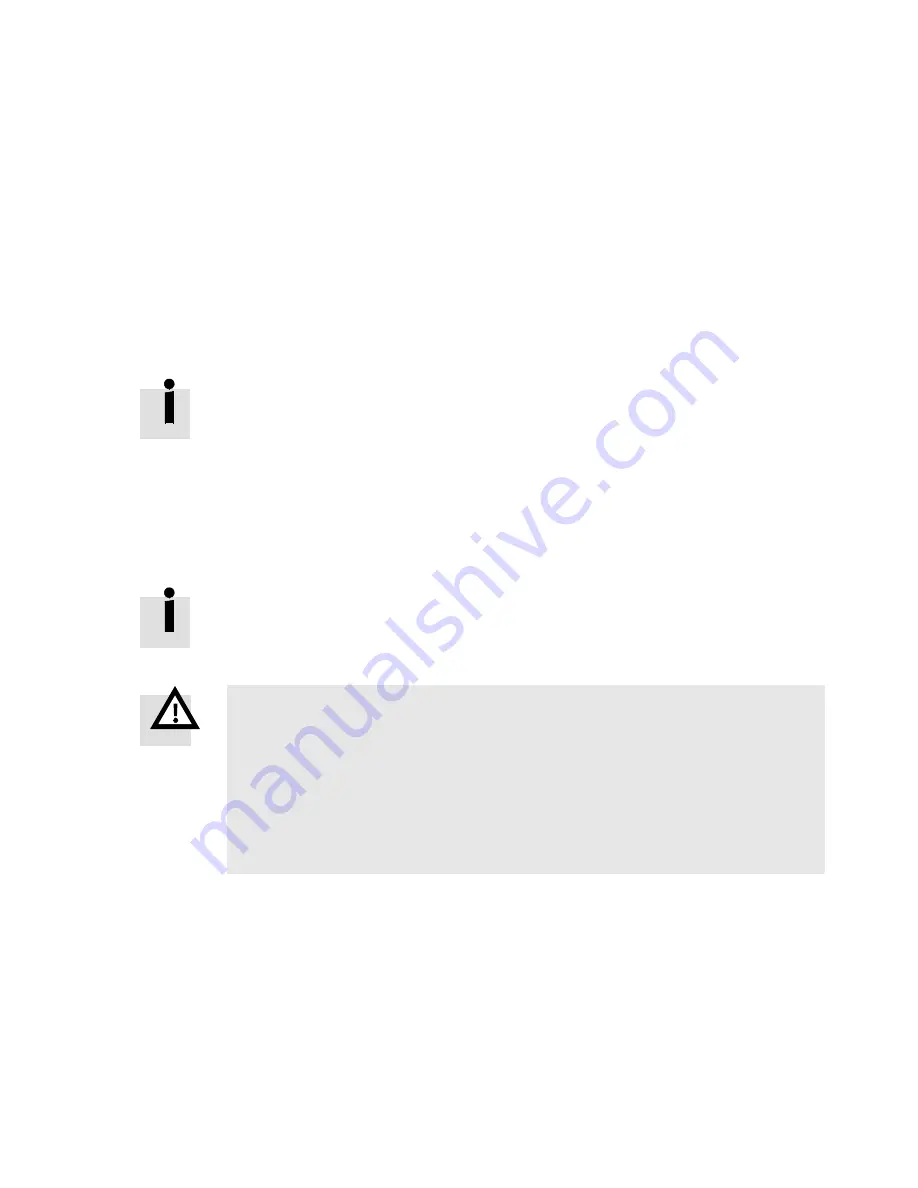
4
Electrical installation
Festo – GDCP-CMMD-AS-HW-EN – 1404NH – English
39
4.8.2
Output power per axis
The intermediate circuits are connected internally. The nominal current of both axes together is 8 A.
These 8 A can be distributed flexibly between axes 1 and 2. Here, the maximum nominal current for the
first axis is 7 A. With distribution 7 A for axis 1 and 1 A for axis 2, the specified total rated output of the
double output stage in S1 operation must be reduced. An increase in the maximum nominal current is
permissible only for axis 1 due to the cooling profile (connection [X6 1]). Peak current per axis is 10 A
(
Appendix A, Tab. A.8). A distribution of peak current similar to that for nominal current is not pos-
sible.
4.8.3
Connecting the screening of the motor cable
If third-party cables are used: Place the complete screening of the motor-side cable flat
on the plug or motor housing. Maximum length 40 mm.
•
Place the complete screening of the motor cable at the screening connection terminal of the related
motor controller so that the leaked current can flow back into the controller causing it.
•
Do not use the complete screening as strain relief.
For further instructions regarding EMC-compliant wiring of the motor
Chapter 4.2.1.
4.8.4
Connection of a holding brake
Holding brakes are not appropriate for braking the motor. They only serve functional hold-
ing of the motor shaft. Additional measures are required for use in safety-oriented applic-
ations.
Warning
The holding brake integrated in the motor, or an external holding brake controlled by
the motor controller, is not suitable for protecting personnel!
•
Provide additional support to protect vertical axes from falling or slipping down
when the motor is switched off through
–
mechanical locking of the vertical axis
–
an external brake/catch/clamping device or
–
sufficient counterbalance of the axis.
•
Connect the holding brake to the terminals BR+ (Pin 2) and BR- (Pin 1) of the related connection
[X6.1] or [X6.2]. The brake is supplied from the logic supply of the motor controller.