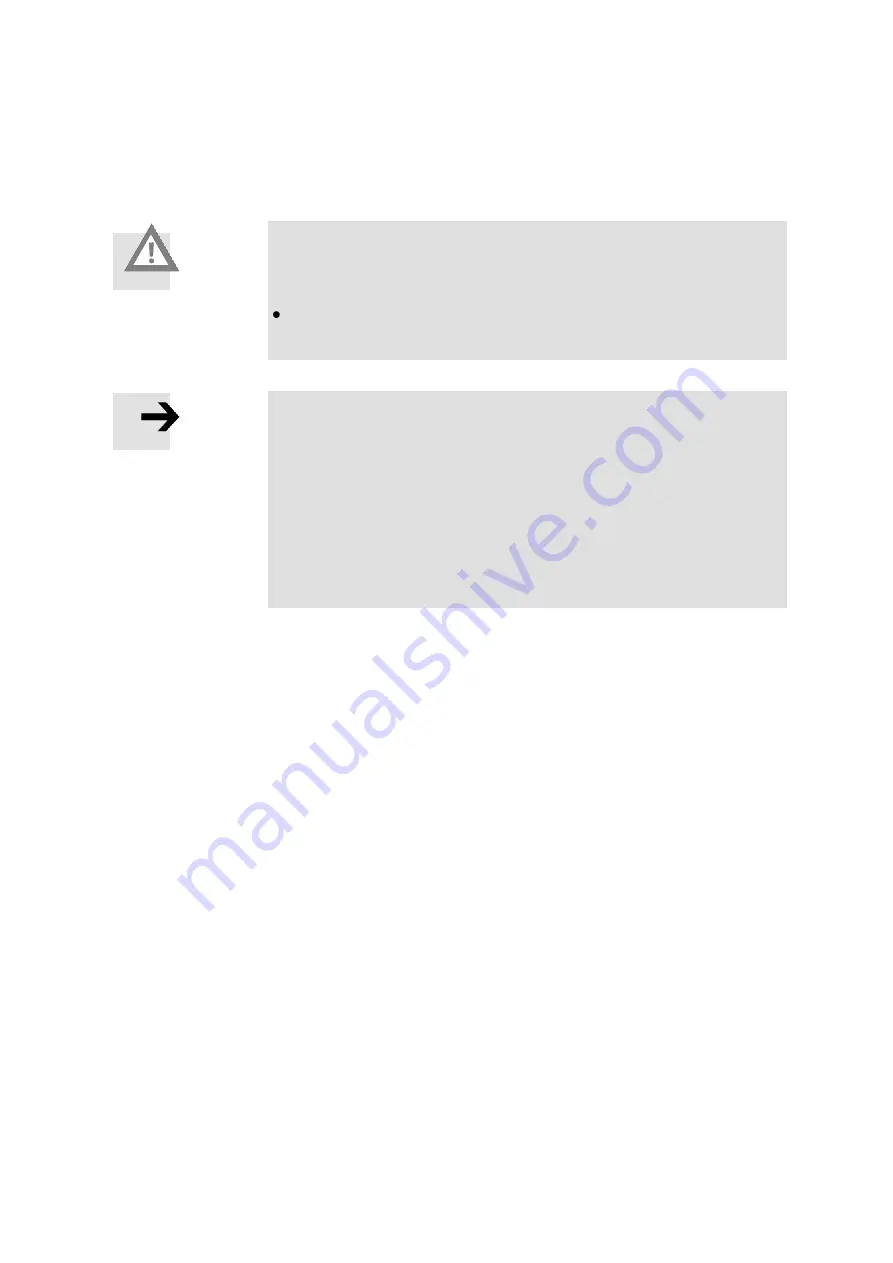
2. Assembly
20
Festo GDCP-CMXR-C2-HW-EN 1002NH
2.
Assembly
2.1
General instructions on assembly and dismantling
Caution
Sub-assemblies, modules and control systems may be damaged if
they are not handled correctly.
Before carrying out assembly, installation and maintenance
work, always switch off the operating and load voltage supplies.
Note
Damage to components!
Handle all modules and components with great care. Note
especially the following:
-
Contact surfaces must be clean (avoid contact errors).
-
The bus plug contacts must not be bent.
-
Make sure that no bits of wire, filling material or shavings fall
into the device when you drill holes or connect wires.
2.2
Guidelines on the CMXR-C2 device configuration
Guidelines on the device configuration for the multi-axis control system CMXR-C2
The multi-axis control system CMXR-C2 is supplied pre-assembled ex-works. You may
adapt the device to your requirements by adding or removing modules.
Rules for assembly
-
A maximum of 12 peripheral modules may be connected in series on the right-hand
side of the central module.
-
The layout of the peripheral modules is freely selectable.
-
The central module provides 45 W (24 V) and 24 W (5 V) to power the peripheral
modules and optional modules respectively.
-
Peripheral modules of the same type must be set to different module addresses
(see section 2.2.2).
-
Peripheral modules with different type designations (e.g. CECX-D-16E and CECX-D-14A-2)
can have the same module addresses.
Summary of Contents for CMXR-C2
Page 2: ......
Page 5: ...Festo GDCP CMXR C2 HW EN 1002NH 5...
Page 56: ...6 Maintenance and care 56 Festo GDCP CMXR C2 HW EN 1002NH...