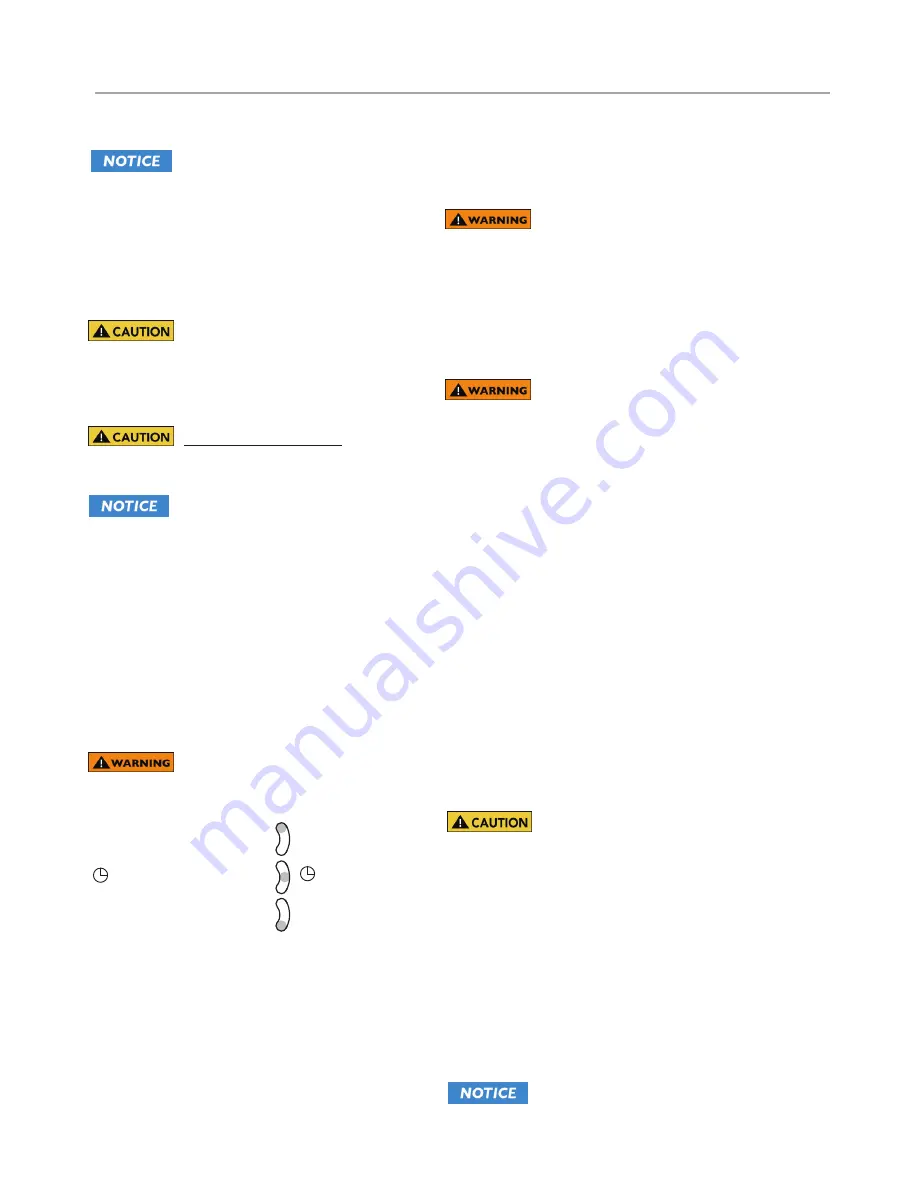
Read
all
warnings
and
instructions
before
performing
any
installation,
maintenance,
or
troubleshooting.
These
instructions
are
intended
to
aid
service
personnel
in
isolating
the
issue
causing
the
CU
Steambath
generator
to
malfunction.
Troubleshooting
does
NOT
substitute
authorized
technical
service
or
factory
evaluation.
For
replacement
parts
and
warranty
information,
please
call
MrSteam
technical
support
at
the
number
listed
at
the
bottom
of
this
document.
Before beginning troubleshooting, with
all power disconnected at main switch, insure all elec-
trical and mechanical connections are tight before
energizing unit to prevent electrical problems and
mechanical leaks.
Under any circumstances, only
qualified service personnel should attempt the
below procedures.
Refer to wiring diagram for check points.
STEP 1:
Test your main control voltage and verify you
have 120V.
STEP 2:
When you have your blowdown timer set
properly and running you will have 120V at these two
points. Make sure your blowdown timer is set for a run-
time. Refer to page 29 for full instructions on operating
the blowdown timer. You must have voltage coming
out of the blowdown timer from the brown wire. Have it
set to run. Below are the 3 way manual override switch
positions. You can set it to permanent ON for all of the
following tests.
Burn Hazard. Pressurized Steam and
Hot Water is discharged during blowdown.
3-WAY MANUAL OVERRIDE SWITCH
I
= Boiler Permanent ON
I
= Automatic
O
= Boiler Permanent OFF
O
STEP 3:
Make sure the on/off switch is set to the on
position. Testing here will determine if the on/off switch is
functioning. If there is no voltage then your switch is faulty.
STEP 4:
Check to see that you have 120V going to L1
& L2 of the upper PC board. If you do not have voltage
this could mean that the room overtemp (125 degree)
has tripped and cut the power to the rest of the
system.
mr
.
steam
®
C U S E R I E S
Installation, Operating & Maintenance Manual
TROUBLESHOOTING
THE
104460
BOARD
Perform
the
steps
below
to
verify
proper
function
Substitution
of
components
or
modification
of
wiring
systems
voids
warranty
and
can
lead
to
dangerous
oper-
ating
conditions.
• Pulling off the purple wire from the board should cause the
water solenoid to engage and fill the unit.
• If the sight glass is full and tripped on a high water, pulling the
pink wire will release it from a high water condition and engage
the contactors(if the rest of the circuit is functioning properly).
Safety
glasses
and
gloves
should
be
worn
at
all
times
when
working
with
or
examining
water
gauge
glass
and
connections.
STEP
5:
Verify
that
you
have
120V
on
L1
&
L2
of
the
lower
pc
board.
If
not
you
may
have
a
problem
with
your
upper
pc
board
TROUBLESHOOTING THE 90241MRT BOARD
Perform the steps below to verify proper function.
• Pull
off
the
red
wire
from
the
9
inch
probe
on
the
top
of
the
pressure
vessel
and
physically
ground
it
out
to
the
pressure
vessel
or
the
jacket.
This
should
send
voltage
through
the
NO
(normally
open)
terminal
on
the
board
to
engage
the
contactors.
• To
check
a
faulty
test
button,
you
can
take
a
jumper
wire
and
jump
across
the
two
test
button
terminals.
This
should
allow
the
board
to
actuate
correctly
if
the
button
is
faulty.
• A
blinking
light
on
the
pc
board
indicates
the
board
is
having
difficulty
sensing
water
(either
due
to
a
dirty
probe
or
low
conductivity
in
the
water).
Holding
the
reset
button
for
30
seconds
should
reset
the
board
back
to
function.
See
next
section
for
maintenance
schedule
in
locales
where
water
quality
requires
regular
treatment.
Turn off all power supplies to steambath
generator and release pressure to zero (0) psig before
removing probes.
MAINTENANCE OF PROBE AND LWCO
• Inspect
probe
annually
for
scale
build-up
and
clean
if
necessary.
Make
certain
there
is
no
scale
or
build-up
on
the
probe
or
its
white
insulator.
For
cleaning
instructions,
refer
to
page
25.
• Replace
probe
every
10
years.
More
frequent
replace-
ment
of
the
probe
is
required
if
it
is
used
in
locales
where
significant
water
treatment
is
required,
where
more
frequent
cleaning
is
necessary,
or
in
applications
with
high
make-up
water
requirements.
• Replace
the
low
water
cutoff
every
15
years.
For recommended feedwater quality,
refer to page 10.
TROUBLESHOOTING GUIDE
33