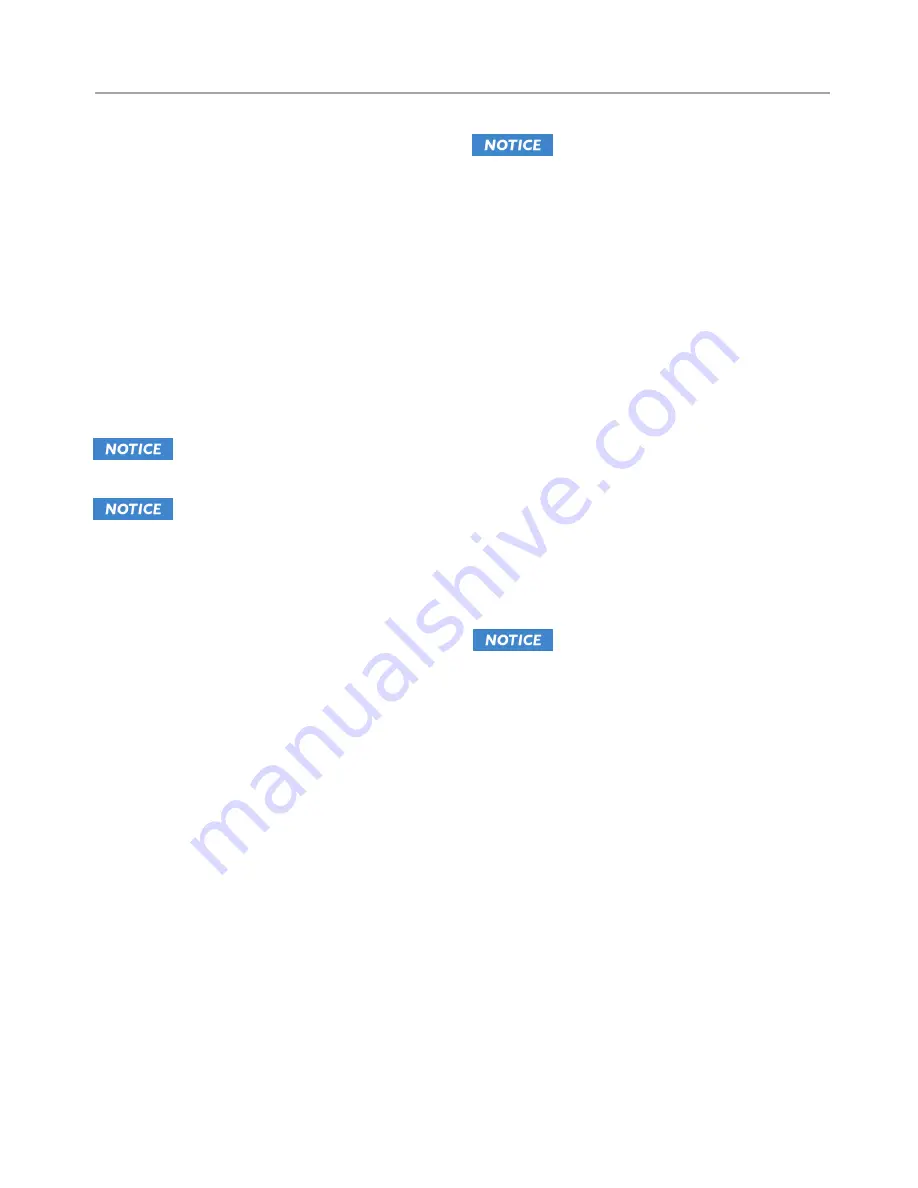
mr
.
steam
®
C U S E R I E S
Installation, Operating & Maintenance Manual
PRINCIPLES
OF
OPERATION
MrSteam
CU
Steambath
Generators
require
two
sources
of
electrical
supply
–
power
voltage
and
control
voltage.
Power
voltage
is
usually
208,
240,
or
480
volt,
single
or
three
phase.
Control
voltage
for
generator
suitable
for
operation
with
these
voltages
is
120V,
1PH.
The
Automatic
Blowdown
System
(CU81600)
has
a
24-
hour,
7-day
timer
that
turns
the
steambath
generator
ON
and
OFF.
At
the
beginning
of
the
"ON"
cycle,
the
boiler
is
automatically
blown
down,
discharging
daily
accumu-
lation
of
minerals
and
salts
which
if
not
drained
may
affect
steam
generator
performance.
An
Auxiliary
Manual
Reset
Low
Water
Cutoff
serves
as
a
back
up
to
the
standard
liquid
level
control
as
required
in
some
jurisdictions
and
operation.
In
all
cases,
refer
specifically
to
the
boiler
data
plate
located
on
the
outside
of
the
boiler
enclosure
for
rated
power
and
control
voltages.
See
the
generator
nameplate
for
specific
electrical
supply
requirements
for
your
steam
generator.
A
lighted
ON/OFF
switch
activates
the
control
circuit.
MrSteam
CU
Generators
are
equipped
with
automatic
liquid
level/low
water
cutoff
control.
CU360
–
CU1400
are
equipped
with
a
dual
probe
type
electronic
control.
CU2000-CU4500
are
equipped
with
float
type
MM150
control
(Refer
to
wiring
diagrams.)
When
there
is
no
water
in
the
generator,
the
contactor
is
"OFF"
and
the
water
feed
solenoid
valve
is
"ON".
The
unit
will
start
fill-
ing
with
water.
When
the
water
level
has
reached
approximately
halfway
up
the
gauge
glass,
the
contac-
tor(s)
will
be
energized
and,
in
turn,
energize
the
heating
element(s).
The
water
solenoid
will
continue
to
feed
water
for
a
short
time
and
then
de-energize.
Steam
will
be
available
within
a
few
minutes.
The
generator
has
an
electronic
high
water
level
cutoff
control.
If
water
level
rises
near
the
top
of
the
pressure-
sure
vessel,
the
contactor(s)
and
the
water
feed
solenoid
valve
will
de-energize
to
“OFF”.
When
steam
pressure
reaches
the
operating
pressure
control
setting,
the
pres-
sure
control
will
de-energize
the
contactor(s).
Operating
pressure
control
is
factory
set
at
5
psig.
It
is
recommended
that
the
steam
gen-
erator
not
be
operated
higher
than
5
PSIG.
Steam
supply
to
the
steambath
is
controlled
by
the
Digital
1
Temperature
Control
System
and
the
steam
solenoid
valve(s).
As
the
room
temperature
selected
by
the
owner/operator
decreases
below
the
set
point,
the
Digital
1
Control
will
energize
the
steam
solenoid
valve(s)
and
allow
steam
to
enter
the
steam
room.
Once
the
set
temperature
on
the
control
is
reached
at
the
sensor,
the
control
will
de-energize
the
steam
valve,
closing
the
valve
and
stopping
the
flow
of
steam
into
the
steam
room.
The
Digital
1
Kit
is
provided
with
Over
Temperature
Control.
Digital
1
monitors
the
room
temperature
inside
the
commercial
steambath.
If
the
room
temper-
ature
exceeds
the
set
point,
the
Digital
1
shuts
off
the
power
to
the
CU
Steambath
Generator,
shutting
steam
off.
CU-HL
can
also
send
a
signal
to
an
audible
alarm
(CU
Alarm
sold
separately).
The
pressure
in
the
generator
will
decrease
slightly
as
steam
leaves
the
generator
and
enters
the
steam
room.
The
pressure
control
will
energize
and
de-ener-
gize
the
contactor(s),
maintaining
the
set
pressure.
As
the
water
level
in
the
generator
decreases,
the
liquid
level
control
will
energize
the
water
solenoid
valve
on
and
off
and
maintain
proper
water
level.
Owners/operators
should
obtain
a
copy
and
familiarize
themselves
with
the
latest
edition
of
the
American
College
of
Sports
Medicine
Health/Fitness
Faculty
Standards
and
Guidelines,
or
a
similar
resource
and
reference
publication,
and
refer
to
those
guidelines
for
the
proper
and
safe
operation
of
a
spa
facility
including
steam
rooms.
The
owner/operator
has
the
responsibility
to
select
a
room
operating
temperature
meeting
guideline
requirements
for
steam
rooms.
Important
Optional
Equipment:
An
optional
control
circuit
transformer
provides
con-
trol
circuit
voltage
from
the
power
supply
voltage.
This
option
is
in
lieu
of
the
need
for
a
separate
con-
trol
circuit.
19