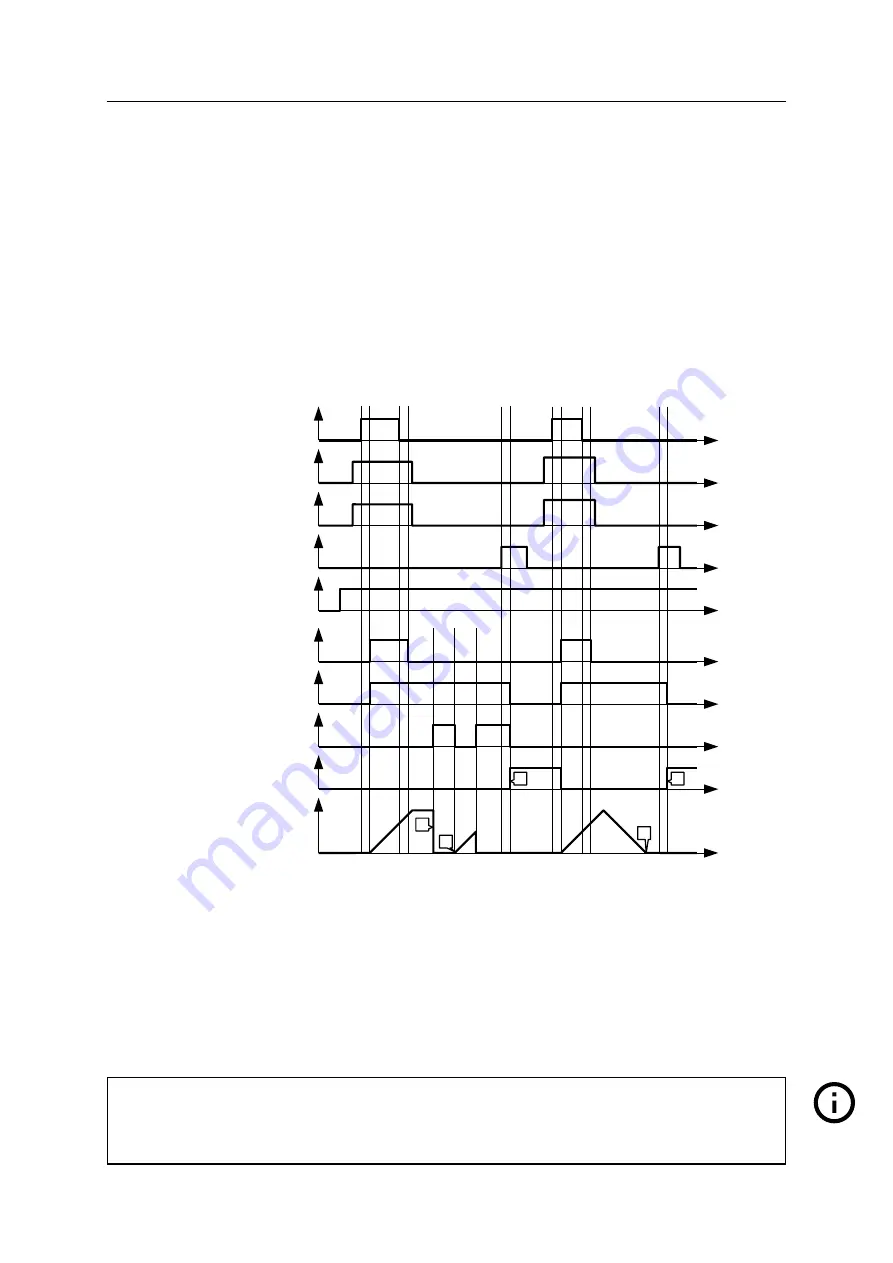
4. CiA402 Drive Profile
Push Motion (Non-stop Mode)
The Push Motion (Stop Mode) of Ezi-SERVOII EtherCAT TO moves motor to the Target Position while
maintaining the specified torque. Stops motor when a work is detected, but it moves again when a work
is disappeared. it continues the Push Motion until a stop command is received. The motor torque during
the Push Motion can be set through Push ratio of Object 201Ah: Push Mode. Pull back distance of
Object 201Ah: Push Mode allows to set the distance to pull back the motor when the Push Motion is
finished.
To do Push Motion (Non-stop Mode) to the new Target Position, Set Push Mode (Bit 12) and Non-stop
Push (Bit 13) before change New Set-Point (Bit 4) of Control word from RESET to SET. Once controller
receives this request, Set-Point Acknowledge (Bit 12) and Push State (Bit 8) of Status word become SET
and the Push Motion is executed. Target position refers to Target position (607Ah) and Position value
can be absolute coordinates or relative coordinates by Control word of Relative (Bit 6).
In the Push Motion (Non-stop Mode), the Push Motion is not finished even if a work is detected or the
target position is reached. the Push Motion is finished when Halt (Bit 8) of Control word becomes SET.
t
t
t
t
t
Actual Speed
Control Word – bit 4
New Set-Point
Target Position
Status Word – bit 12
Set-Point Acknowledge
Status Word – bit 10
Target Reached
t
Control Word – bit 12
Push Mode
t
Status Word – bit 14
Push Detected
t
Status Word – bit 8
Push State
1
3
t
Control Word – bit 13
Non-stop Push
2
t
Control Word – bit 8
Halt
4
4
Figure 4.8: Push Motion (Non-stop Mode)
1. A work was detected. The detection status can be judged by Push Detected (Bit 14) of Status
word.
2. It continues the Push Motion when a work is disappeard.
3. The target position is reached. But the Push Motion is not finished.
4. When Halt (Bit 8) of Control word becomes SET, the motor stops and the Push Motion is finished.
the Target Reached (Bit 10) of Status word becomes SET after finished the Push Motion.
Information
If the motor speed is fast or the value of Push ratio is low, it may be determined that a work is
detected even if a work is not detected actually. In this case, lower the motor speed or increase the
Push ratio.
Rev.37
FASTECH Co., Ltd.
50
Summary of Contents for Ezi-SERVOII EtherCAT TO
Page 10: ...Chapter 1 Product Specification Rev 37 FASTECH Co Ltd 10...
Page 12: ...1 Product Specification 1 2 Product Dimension Figure 1 2 Dimensions Rev 37 FASTECH Co Ltd 12...
Page 15: ...Chapter 2 Installation Rev 37 FASTECH Co Ltd 15...
Page 29: ...Chapter 3 EtherCAT Communication Rev 37 FASTECH Co Ltd 29...
Page 35: ...Chapter 4 CiA402 Drive Profile Rev 37 FASTECH Co Ltd 35...
Page 67: ...Chapter 5 Operation Rev 37 FASTECH Co Ltd 67...
Page 71: ...Chapter 6 EtherCAT Object Dictionary Rev 37 FASTECH Co Ltd 71...