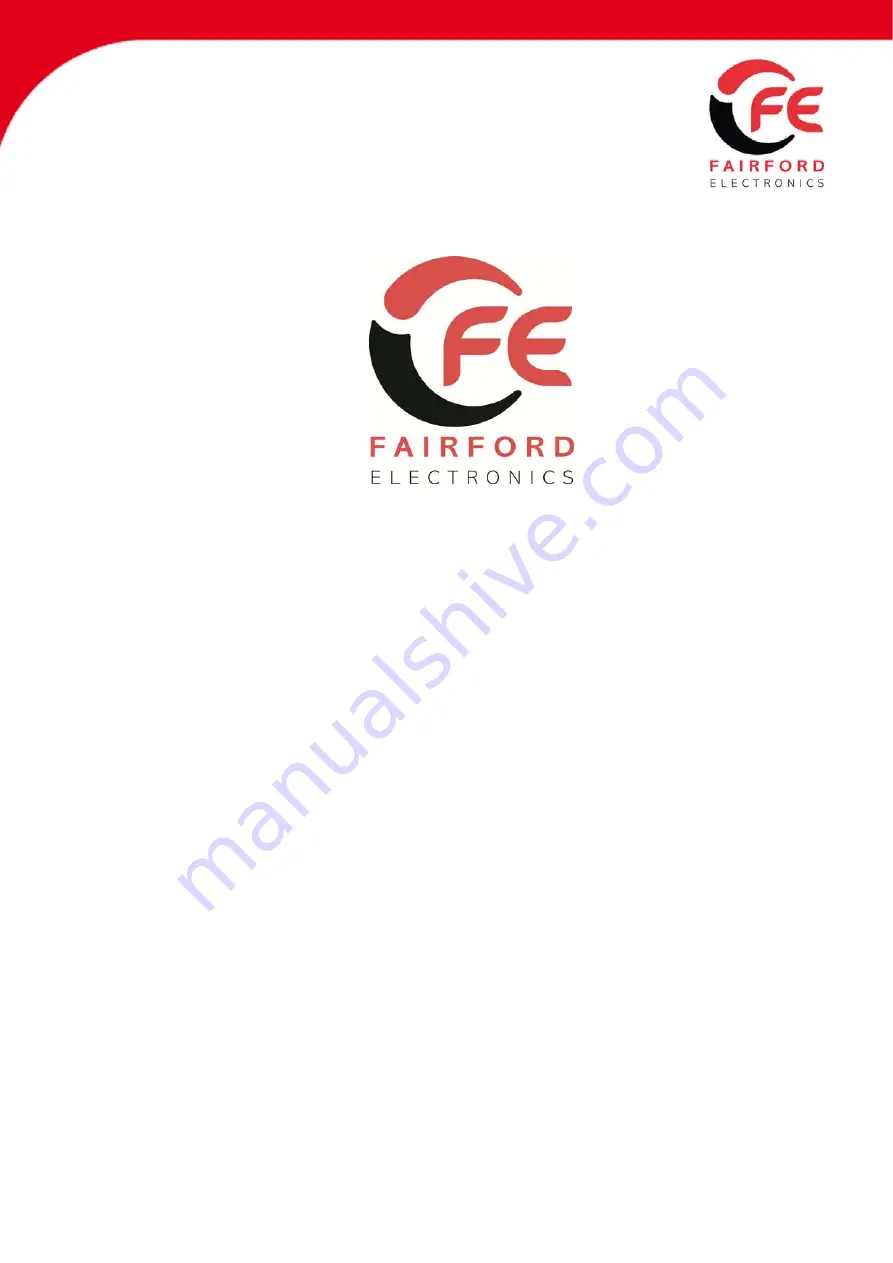
Fairford Electronics •
Innovation in Soft Start Technology
Bristow House, Gillard Way, Lee Mill Industrial Estate, Ivybridge, PL21 9GG. United Kingdom Tel: +44 (0) 1752 894554 • Fax: +44 (0) 1752 897145 • Email: [email protected] •
www.fairford.com
QFE
Manual
©
2011
by
Fairford
Electronics,
all
rights
reserved
Copyright
subsists
in
all
Fairford
Electronics
deliverables
including
magnetic,
optical
and/or
any
other
soft
copy
of
these
deliverables.
This
document
may
not
be
reproduced,
in
full
or
in
part,
without
written
permission.
Enquiries
about
copyright
of
Fairford
Electronics
deliverables
should
be
made
to
Fairford
Electronics,
Bristow
House,
Gillard
Way,
Lee
Mill
Industrial
Estate,
Ivybridge,
PL21
9GG.
If,
by
permission
of
the
copyright
owner,
any
part
of
this
document
is
quoted,
then
a
statement
specifying
the
original
document
shall
be
added
to
the
quotation.
Any
such
quotation
shall
be
according
to
the
original
(text,
figure
or
table)
and
may
not
be
shortened
or
modified.
Summary of Contents for QFE Series
Page 18: ...Mechanical Installation QFE page 1 2 FD841205_F...
Page 26: ...Mechanical Installation QFE page 1 10 FD841205_F...
Page 43: ...QFE page 2 19 Electrical Installation FD8413 issue03_F...
Page 50: ...Electrical Installation QFE page 2 26 FD8413 issue03_F...
Page 51: ...QFE Soft Start Motor Controller Technical Data for the QFE and QFEplus Applications...
Page 73: ...QFE page 3 25 Applications FD841405_F...
Page 158: ...page 5 47 Programming QFE FD8420 issue02_F This page is left intentionally blank...
Page 181: ...Modbus page 6 4 5MC FD510007...