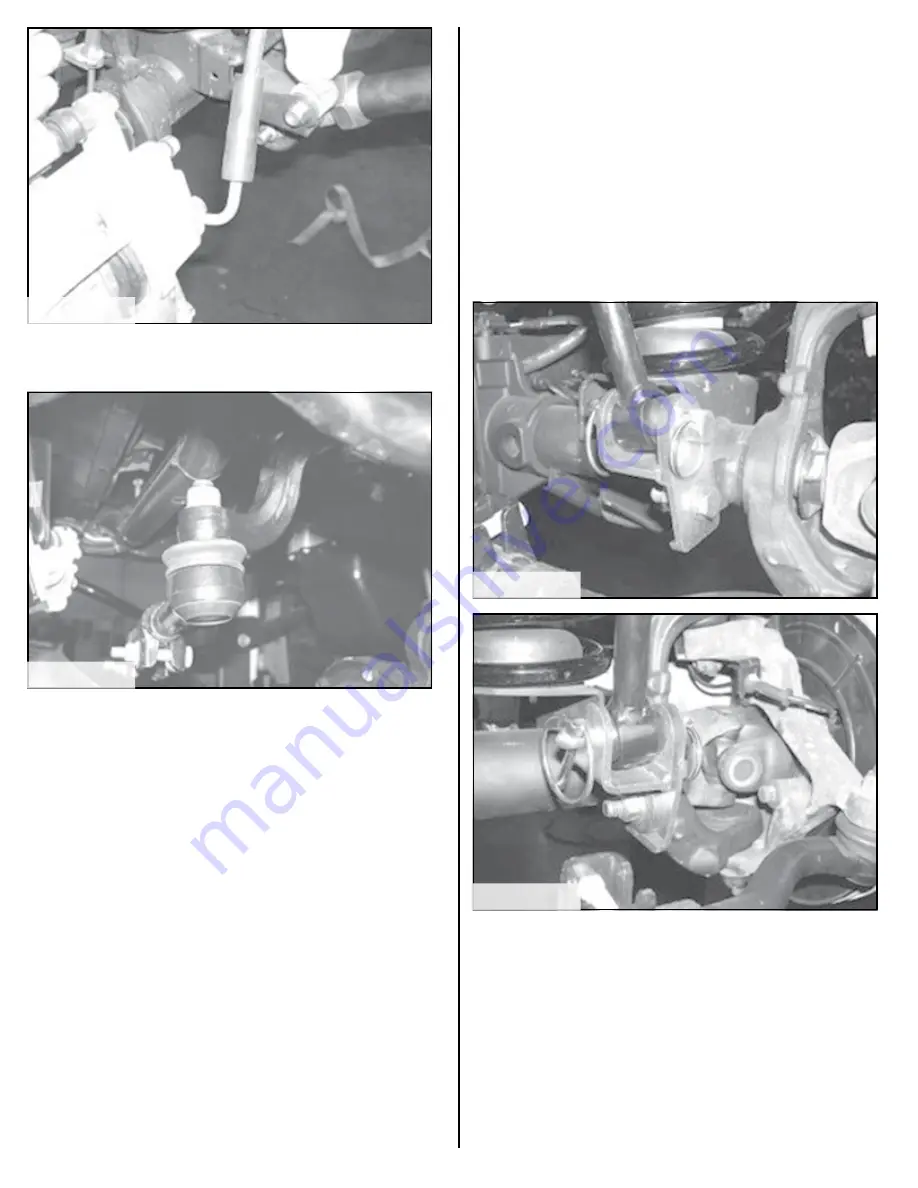
29. Reconnect the inner tie rod end using factory hardware
to the new dropped pitman arm. Torque to 60 ft lbs.
SEE
FIGURE 53.
30. Locate FT50360 drv. & FT50361 pass. Sway Bar Link
Mounts, FT50261 Front Sway Bar Endlinks, FT50048
& FT50089 bushing and sleeve kits. Press one bushing
and one sleeve from the supplied bushing kit into each
end of the end link. Attach the link mount brackets to
the factory sway bar mount on the axle with the supplied
½”x1 ½’ bolts and hardware. Torque to **127 ft. lbs. With
the supplied ½” x 2 ¾” bolts & hardware, connect the new
end link to the sway bar (factory hole in sway bar may
need to be enlarged with a die grinder out to ½”). Mount
the bolt with the head of the bolt facing outward towards
the tire. Then, using the FT42 Sway Bar Pin, FT45 Key
Ring, & FT90036 Lynch pin, connect to the new lower
sway bar mount. Torque the upper hardware to **127 ft.
lbs.
SEE FIGURES 54-57.
FIGURE 52
FIGURE 53
FIGURE 54
FIGURE 55
15 of 31