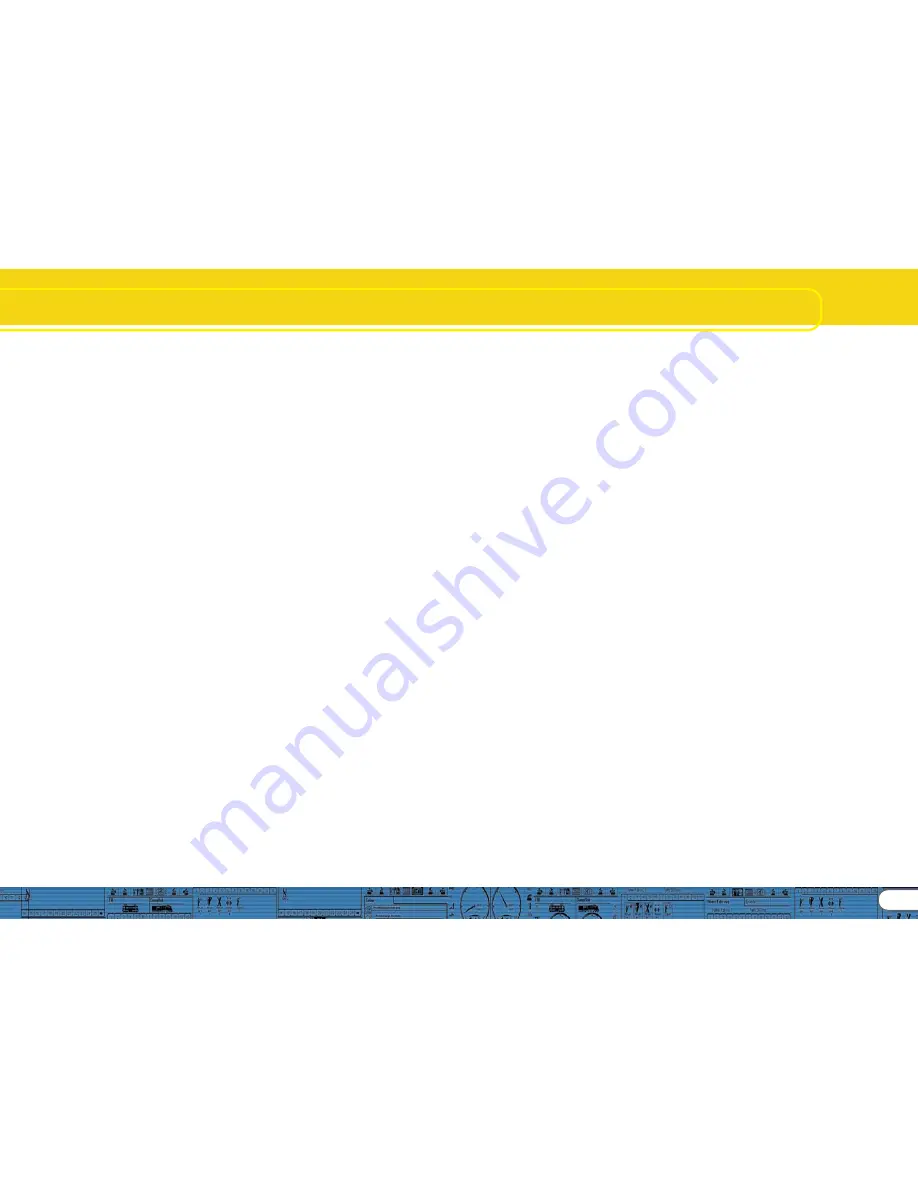
11
Subwindow „Decoder“
8.1. View window „address“
8.1. View window „address“
8.1. View window „address“
8.1. View window „address“
8.1. View window „address“
8.1.1. Address (CV 1, CV 17, CV 18)
8.1.1. Address (CV 1, CV 17, CV 18)
8.1.1. Address (CV 1, CV 17, CV 18)
8.1.1. Address (CV 1, CV 17, CV 18)
8.1.1. Address (CV 1, CV 17, CV 18)
All modifications of the address are done in the window
„Address“. Subject to the decoder type so called short (two
digits, CV1) or long addresses (four digits, CV17 and CV18) can
be used.
Please note that any settings in these CVs are only effective for
operation with NMRA-DCC compliant command stations.
When operating decoders with the Märklin® / Motorola®-
protocol a separate address, namely the Märklin®-address is
valid.
You may enter a second address for M4-decoders in Motorola®
mode in order to activate F5 to F8. Normally this would be the
address of the decoder plus 1.
8.1.2. Consist settings (CV 19)
8.1.2. Consist settings (CV 19)
8.1.2. Consist settings (CV 19)
8.1.2. Consist settings (CV 19)
8.1.2. Consist settings (CV 19)
The DCC consist address is useful for multiple traction. It is also
possible to activate function outputs for consists as well as
function buttons for consist mode.
In some cases it is desirable to set certain functions in consist
mode in such a way that the function is actually triggered by
pressing one button in both (or all) locomotives (e.g.: lights).
Click onto the appropriate button of the function that should
be activated in consist mode.
8.2. Driving characteristics
8.2. Driving characteristics
8.2. Driving characteristics
8.2. Driving characteristics
8.2. Driving characteristics
8.2.1. Selecting the number of speed steps (CV 29,
8.2.1. Selecting the number of speed steps (CV 29,
8.2.1. Selecting the number of speed steps (CV 29,
8.2.1. Selecting the number of speed steps (CV 29,
8.2.1. Selecting the number of speed steps (CV 29,
CV 49)
CV 49)
CV 49)
CV 49)
CV 49)
Here you can adjust more settings for running your locomotive.
In DCC mode you have to first set the number of speed steps to
14, 28 or 128 or alternately to automatic detection of speed
steps.
8.2.2. Reverse mode (CV 29)
8.2.2. Reverse mode (CV 29)
8.2.2. Reverse mode (CV 29)
8.2.2. Reverse mode (CV 29)
8.2.2. Reverse mode (CV 29)
A tick at „Reverse mode“ changes the direction of travel and
the directional characteristics of the headlights. This is useful in
case the wiring has been done incorrectly (swapping of track
leads or motor leads).
8.2.3. Acceleration and deceleration (CV 3, CV 4)
8.2.3. Acceleration and deceleration (CV 3, CV 4)
8.2.3. Acceleration and deceleration (CV 3, CV 4)
8.2.3. Acceleration and deceleration (CV 3, CV 4)
8.2.3. Acceleration and deceleration (CV 3, CV 4)
This option allows you to set the acceleration time (CV3)
respectively the braking time (CV4). The time is calculated by
multiplying the CV-value with 0.869 seconds.
The acceleration time is the time the locomotive takes from
stop to maximum speed. Of course the acceleration time from
stop to mid speed is accordingly shorter.
The same is valid for the braking time. This is the time from
maximum speed until the locomotive stops.
8.2.4. Supported brake modes (CV 51)
8.2.4. Supported brake modes (CV 51)
8.2.4. Supported brake modes (CV 51)
8.2.4. Supported brake modes (CV 51)
8.2.4. Supported brake modes (CV 51)
Here the brake modes can be selected. The LokProgrammer
supports the Märklin®-, Zimo- and Lenz-brake modes.
8.2.5. T
8.2.5. T
8.2.5. T
8.2.5. T
8.2.5. Trim (CV 66, CV 95)
rim (CV 66, CV 95)
rim (CV 66, CV 95)
rim (CV 66, CV 95)
rim (CV 66, CV 95)
The trim function allows you to set the maximum speed
separately for forward and reverse movement. The factor
that is used to multiply the motor voltage, results from dividing
the CV-value by 128 (forward CV 66 and reverse CV 95).
8.3. Motor
8.3. Motor
8.3. Motor
8.3. Motor
8.3. Motor
8.3.1. DC motor PWM frequency (CV 49)
8.3.1. DC motor PWM frequency (CV 49)
8.3.1. DC motor PWM frequency (CV 49)
8.3.1. DC motor PWM frequency (CV 49)
8.3.1. DC motor PWM frequency (CV 49)
Here you can select the desired tact frequency for motor control
(pulse width modulation). The possible values are 15kHz and
30kHz. LokSound decoders as from V3.5 are normally set to
30kHz.
8.3.2. Load compensation (CV 49, CV 53, CV 54,
8.3.2. Load compensation (CV 49, CV 53, CV 54,
8.3.2. Load compensation (CV 49, CV 53, CV 54,
8.3.2. Load compensation (CV 49, CV 53, CV 54,
8.3.2. Load compensation (CV 49, CV 53, CV 54,
CV 55 and CV 56)
CV 55 and CV 56)
CV 55 and CV 56)
CV 55 and CV 56)
CV 55 and CV 56)
Load compensation helps to adjust the motor power in case of
obstructions such as gradients.
First of all you may decide if you want to use load compensation
or not (CV 49). Then you can set the reference voltage (CV 53)
and the two control parameters K and I (CV 54 and 55).
Furthermore you can set the impact (effectiveness) of load
compensation (CV 56). At 100%, load compensation is active
over the entire speed range; at 50% it is only active up to half
the maximum speed.
With this setting your locomotives benefit from load
compensation at lower speeds while their speed changes
prototypically on gradients.
The numbers of values respectively the values themselves are
subject to the type of decoder. For useful values please consult
chapter X.1 or the user manual of your decoder.
8.3.3. Speed curves (CV 2, CV 5, CV 6, CV 26,
8.3.3. Speed curves (CV 2, CV 5, CV 6, CV 26,
8.3.3. Speed curves (CV 2, CV 5, CV 6, CV 26,
8.3.3. Speed curves (CV 2, CV 5, CV 6, CV 26,
8.3.3. Speed curves (CV 2, CV 5, CV 6, CV 26, ...
...
...
...
...
and CV 67-97)
and CV 67-97)
and CV 67-97)
and CV 67-97)
and CV 67-97)
The field „Speed Curves“ gives you a choice of a three-point-
speed curve or a user-defined speed curve.
The three-point-speed-curve is determined by the start voltage
(CV 2), the medium speed (CV 6) and the maximum speed (CV
5).
The speed curve has a higher resolution with 28 speed steps.
Subject to the selected speed steps you can move the individu-
al speed points up and down with the mouse and adjust them
to the most prototypical setting.
The three-point-speed-curve and the individual speed curve
with 28 entries are valid for all operating modes: DCC 14, 28 or
128 speed steps, Motorola® format (14 speed steps) or M4;
the selected speed curve will always be adapted (interpolated)
to the actual speed mode.
With the choice menu „Default“ you can enter a simple linear
or exponential speed curve.
8.4. DCC / Analogue
8.4. DCC / Analogue
8.4. DCC / Analogue
8.4. DCC / Analogue
8.4. DCC / Analogue
8.4.1. Zimo® manual function (CV 49)
8.4.1. Zimo® manual function (CV 49)
8.4.1. Zimo® manual function (CV 49)
8.4.1. Zimo® manual function (CV 49)
8.4.1. Zimo® manual function (CV 49)
Activates the Zimo® manual function.
8.4.2. Analogue mode (CV 29)
8.4.2. Analogue mode (CV 29)
8.4.2. Analogue mode (CV 29)
8.4.2. Analogue mode (CV 29)
8.4.2. Analogue mode (CV 29)
Activates the analogue mode.
8.4.3. Supported analogue modes and settings
8.4.3. Supported analogue modes and settings
8.4.3. Supported analogue modes and settings
8.4.3. Supported analogue modes and settings
8.4.3. Supported analogue modes and settings
(CV 50, CV 125, CV 126, CV 127 and CV 128)
(CV 50, CV 125, CV 126, CV 127 and CV 128)
(CV 50, CV 125, CV 126, CV 127 and CV 128)
(CV 50, CV 125, CV 126, CV 127 and CV 128)
(CV 50, CV 125, CV 126, CV 127 and CV 128)
In analogue mode load compensation is not active. Therefore
by using the appropriate slide control you can adapt the start
voltage and the maximum speed separately for AC or DC
analogue mode to match the characteristics of your motor or
transformer.
Furthermore you can select the functions that should be active
in analogue mode (DC, AC or both; CV 50).
8.4.4. Analogue mode F1-F8 / Analogue mode FL,
8.4.4. Analogue mode F1-F8 / Analogue mode FL,
8.4.4. Analogue mode F1-F8 / Analogue mode FL,
8.4.4. Analogue mode F1-F8 / Analogue mode FL,
8.4.4. Analogue mode F1-F8 / Analogue mode FL,
F9-F12 (CV 13, CV 14)
F9-F12 (CV 13, CV 14)
F9-F12 (CV 13, CV 14)
F9-F12 (CV 13, CV 14)
F9-F12 (CV 13, CV 14)
Since most analogue layouts do not have input devices to trigger
functions, these parameters allow you to pre-select which
functions should be automatically active in analogue mode.
It is recommended to turn on the sound (default value F1) and
the smoke generator of steam locomotives (often F4).
Furthermore the headlights in both directions would be switched
on in analogue mode (marked as FL(f) and FL(r) in the register).
Functions F9 and F10 can also be set as directional functions
(F9(f), F9(r), F10(f), F10(r)).
Summary of Contents for LokProgrammer
Page 35: ...35...