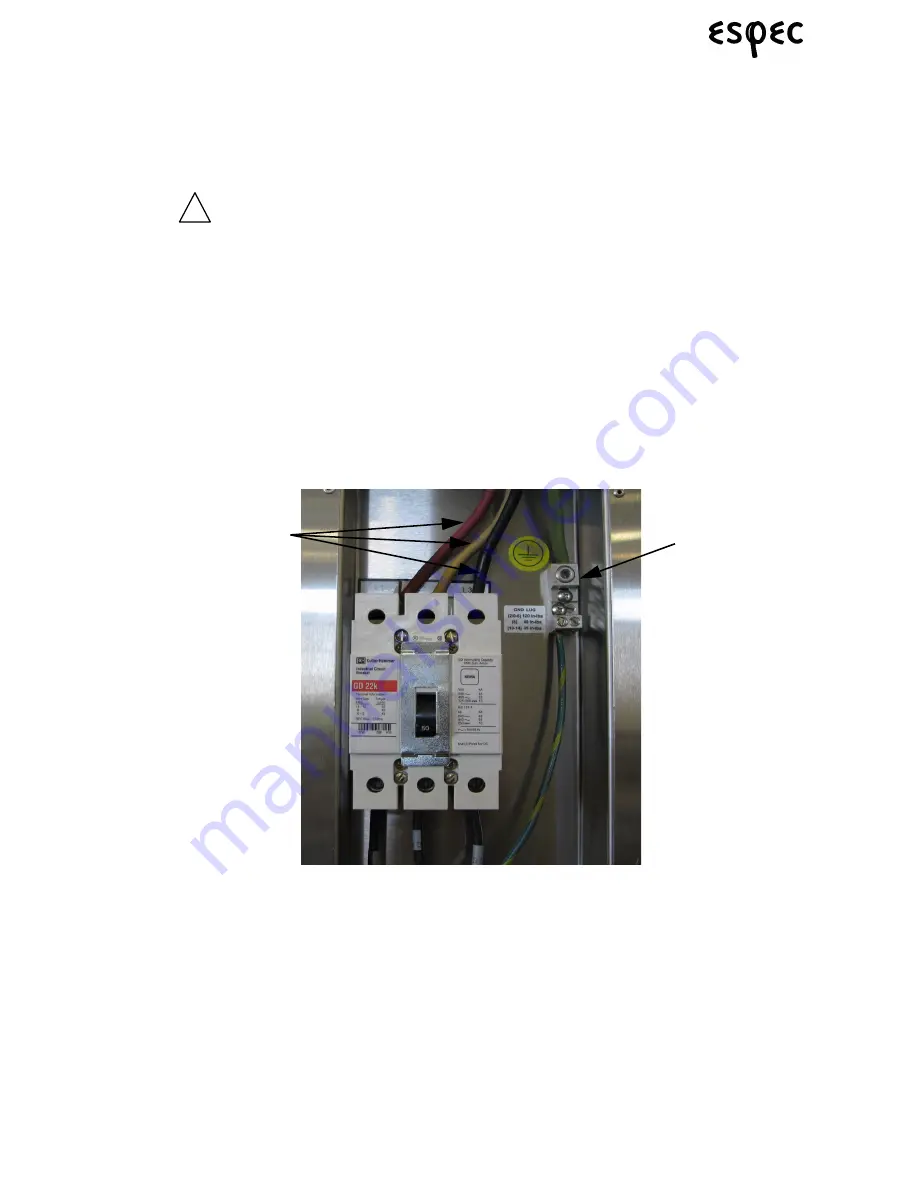
Installation
40
Platinous User’s Manual
5.3.2 Primary Power Supply Connections
The chamber is connected to the primary power supply via the power cable. It is also grounded to prevent
noise from infiltrating electronic circuits and to protect users against electric shock which can result from
leakage current.
EXPLOSION! DO NOT ground the equipment on gas pipes.
Grounding of this sort could result in explosion.
Ground the equipment PROPERLY
ELECTRICAL SHOCK! Unless the equipment is grounded, overcurrent
and short circuit protective devices cannot operate properly, possibly
resulting in electric shock. This will also leave the equipment unprotected against power supply
noise.
Procedure:
Figure 4.11, “Left, rear and top,” on page 24
).
2. Feed the power cable through the top power cable port.
3. Connect phase wires to terminals on top of breaker.
4. Connect the grounding wire of the power cable to the grounding terminal.
FIGURE 5.21.
P
RIMARY
POWER
SUPPLY
CONNECTION
!
DANGER
Grounding
Terminal
Power Phase Wires
Summary of Contents for Platinous ESL Series
Page 1: ...PLATINOUS CHAMBER SERIES USER S MANUAL...
Page 2: ......
Page 6: ...iv Platinous User s Manual...
Page 22: ...Precautions in Usage 16 Platinous User s Manual...
Page 31: ...Platinous User s Manual 25 Names and Functions of Parts...
Page 40: ...Names and Functions of Parts 34 Platinous User s Manual...
Page 58: ...Installation 52 Platinous User s Manual...
Page 80: ...Operation 74 Platinous User s Manual...
Page 106: ...Troubleshooting 100 Platinous User s Manual...