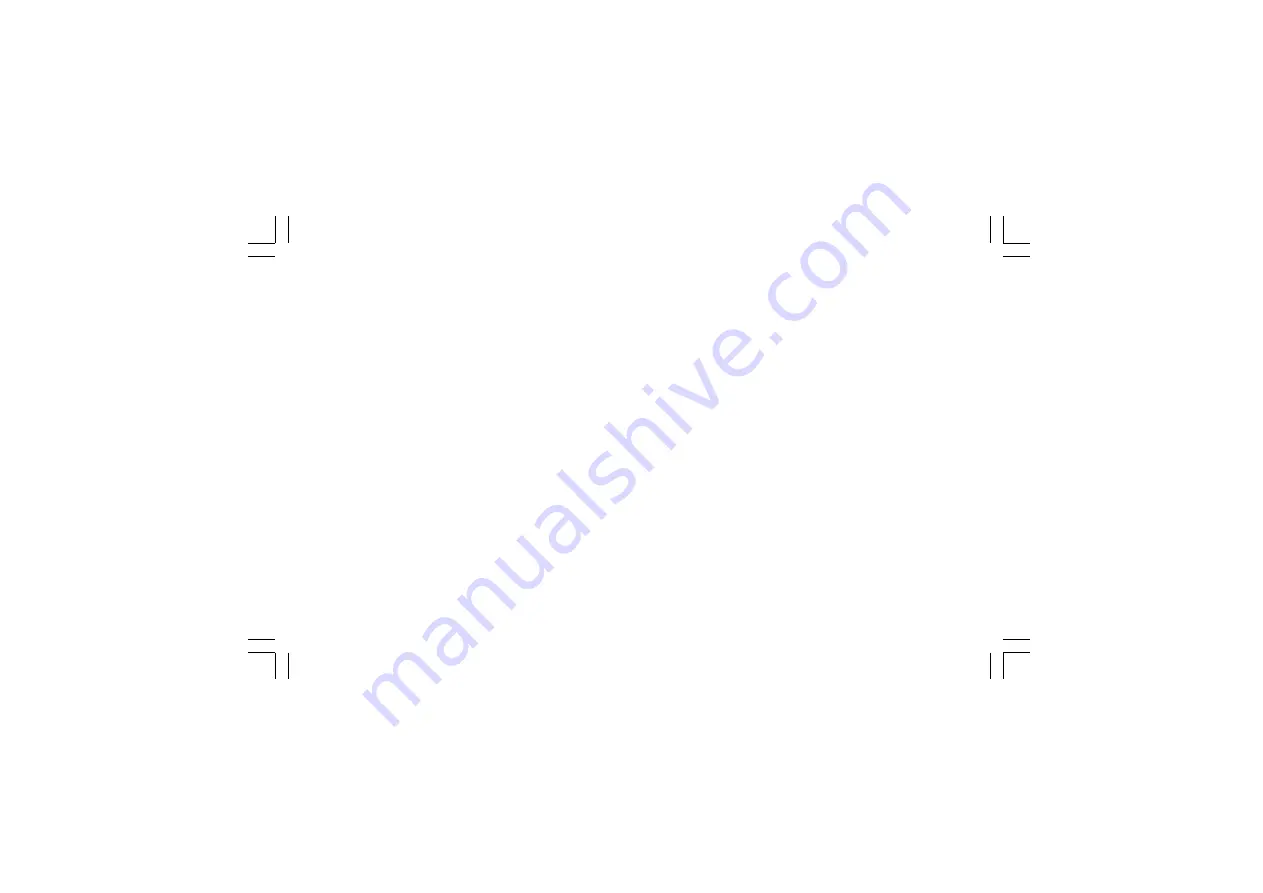
113
Anti reset windup
: from 10 % to 200 % of the input span.
Main output cycle time
: from 1 second to 200 seconds.
Secondary output cycle time
: from 1 second to 200 seconds.
Relative secondary output gain
: keyboard programmable from
0.20 to 2.00 referred to the proportional band.
Overlap / dead band
: keyboard programmable from - 20 %
(dead band) to + 50 % (overlap) of the proportional band.
Output limiters
.
For the main and/or secondary control outputs it is possible to
set:
- output high limits
- output low limits
- output max. rate of rise.
AUTO/MANUAL mode
: selectable by front push-button or logic
input.
OUTPUTS
Control output updating time
:
- 125 ms when a linear input is selected
- 250 ms when a TC or RTD input is selected.
Action
: direct/reverse programmable
Output level limiter
:
- high and low limits for main control output
- high and low limits for secondary control output.
Out 1 and 2
Function
: singularly programmable as
- Control output
- Alarm output
- Event output.
Type
: Relay, SSR or TRIAC.
Out 1 and 2 - Relay
Relay type
: SPDT
Contact rating
: 3 A @ 250 V on resistive load.
Xkc-1-C0.P65
5/29/02, 11:59 AM
113
Summary of Contents for MKC
Page 1: ...r USER MANUAL PKC MKC 170 IU0 XKC 0C1 05 02 Xkc 01 C0 P65 5 29 02 11 58 AM 1...
Page 2: ...Xkc 01 C0 P65 5 29 02 11 58 AM 2...
Page 4: ...Xkc 01 C0 P65 5 29 02 11 58 AM 4...
Page 7: ...3 Fig 2 B OUTLINE AND CUT OUT DIMENSIONS FOR MKC MODEL Xkc 1 C0 P65 5 29 02 11 59 AM 3...
Page 132: ...A 11 Xkc AA0 p65 5 29 02 12 00 PM 11...
Page 140: ...Xkc Z C0 p65 5 29 02 12 01 PM 1...