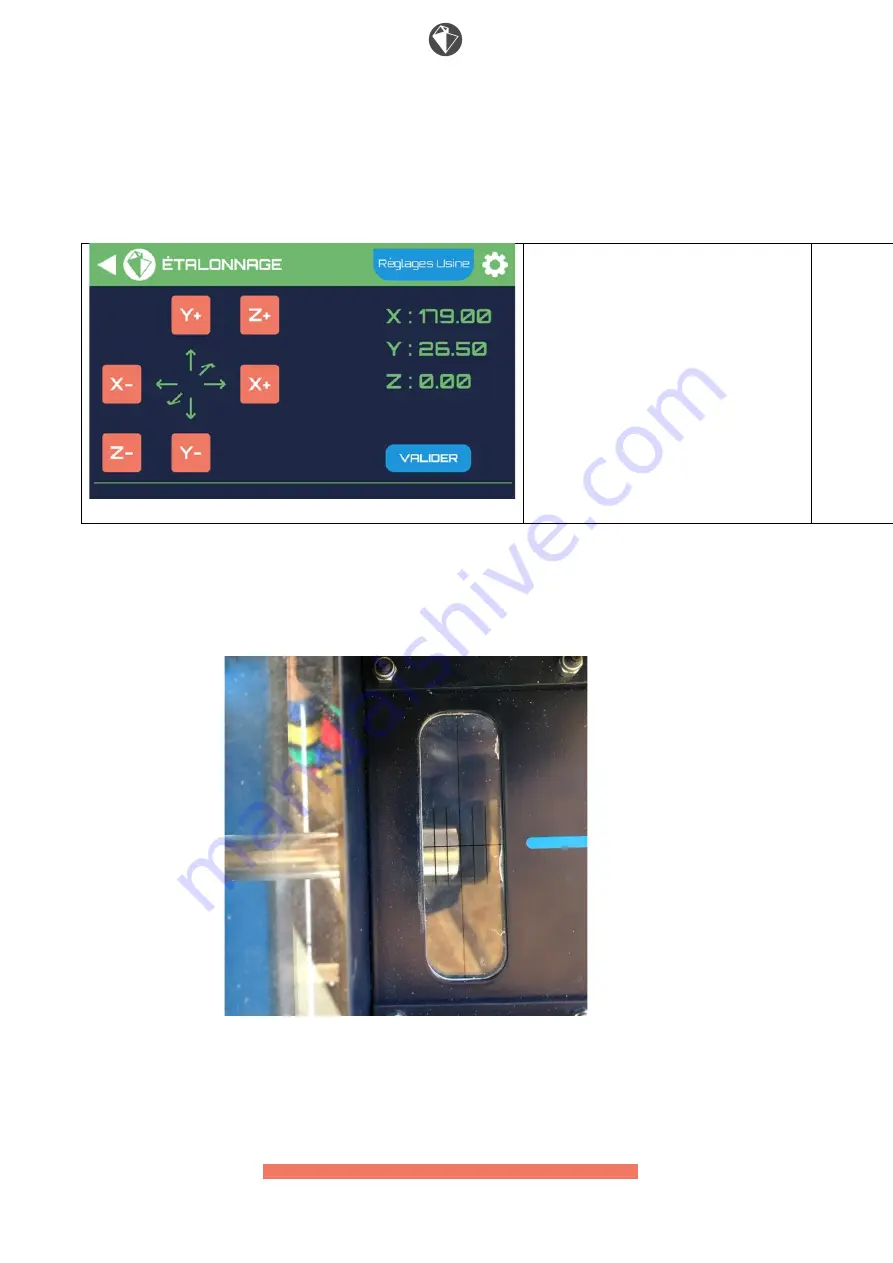
epur | USER’S MANUAL
www.epur.io - - | 35 | - - [email protected]
6.
Using the X+, X-, Y+, Y-, Z+ and Z- buttons, you can move the tool along three
axes. The aim is to align the calibration tool with a physical point on each
of the axes.
CALIBRATION
Factory Settings
OK
7.
Initially, press Z+ until the end of the tool is aligned with the reference
line on the polycarbonate clamping plate. Once aligned, do not touch this axis
any more until the calibration process is over.
8.
Then go to Y to align the top of the tool with the bottom of table Y. Come into
slight contact with the table, being careful not to force. Once in contact, do
not touch this axis any more until the calibration process is over.
Summary of Contents for OAKBOT EOX 4.2 Series
Page 1: ...DOCUMENT epur User s Manual OAKBOT EOX series 4 2 Original Manual...
Page 7: ...epur USER S MANUAL www epur io 7 contact epur io Machining Module Mass 35 kg...
Page 10: ...epur USER S MANUAL www epur io 10 contact epur io Calibration tool Clamps...
Page 36: ...epur USER S MANUAL www epur io 36 contact epur io...
Page 50: ...epur USER S MANUAL www epur io 50 contact epur io...