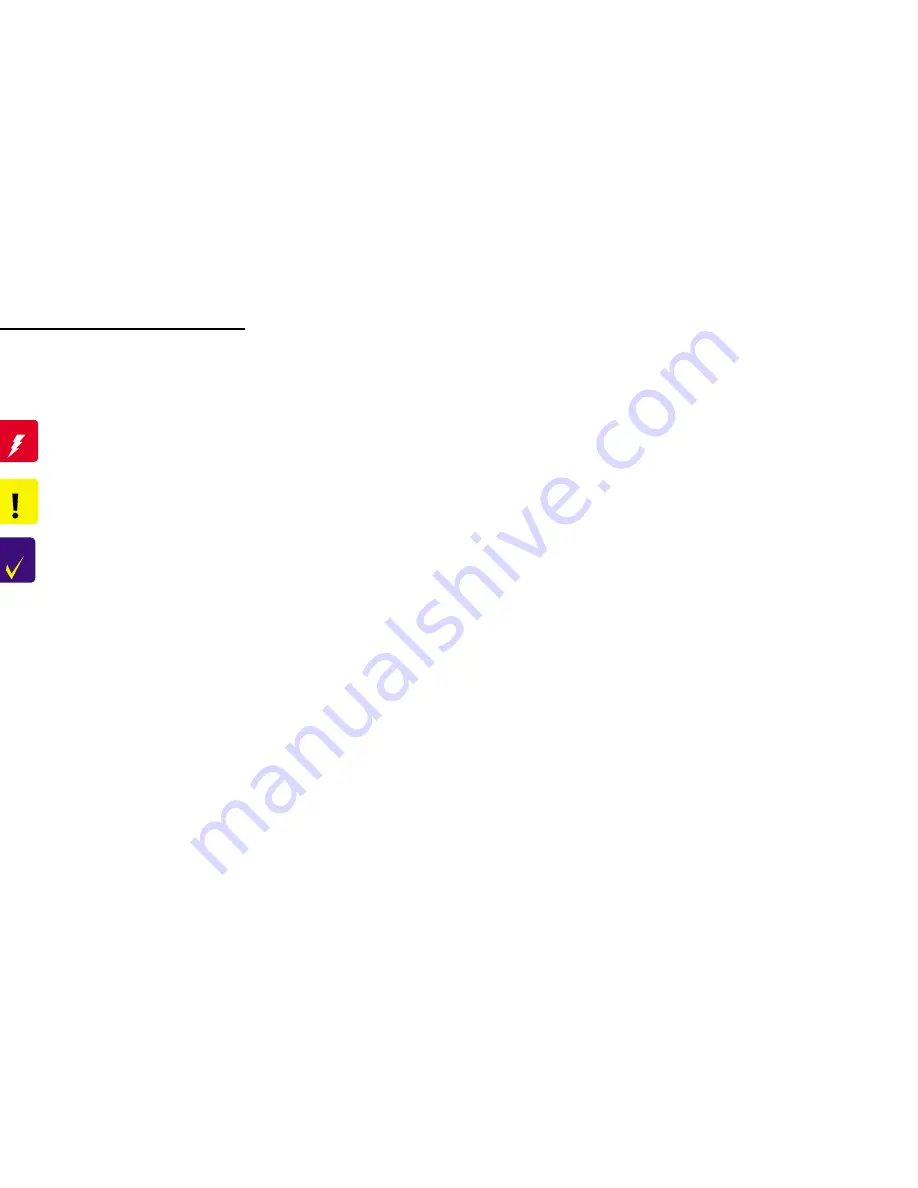
Symbols Used in This Manual
Various symbols are used throughout this manual either to provide additional
information on a specific topic or to warn of possible danger present during a
procedure or an action. Be aware of all symbols when they are used, and always read
WARNING, CAUTION or NOTE messages.
Indicates an operating or maintenance procedure, practice or condition
that, if not strictly observed, could result in injury or loss of life.
Indicates an operating or maintenance procedure, practice, or condition
that, if not strictly observed, could result in damage to, or destruction of,
equipment.
May indicate an operating or maintenance procedure, practice or
condition that is necessary to accomplish a task efficiently. It may also
provide additional information that is related to a specific subject, or
comment on the results achieved through a previous action.
W A R N I N G
C A U T I O N
C H E C K
P O I N T
Summary of Contents for STYLUS COLOR 580
Page 1: ...EPSON STYLUSCOLOR580 Color Inkjet Printer SEIJ00013 SERVICE MANUAL ...
Page 6: ...Revision Status Revision Issued Date Description Rev A August 31 2000 First Release ...
Page 9: ...C H A P T E R PRODUCTDESCRIPTION ...
Page 29: ...C H A P T E R OPERATINGPRINCIPLES ...
Page 50: ...C H A P T E R TROUBLESHOOTING ...
Page 66: ...C H A P T E R DISASSEMBLYANDASSEMBLY ...
Page 99: ...C H A P T E R ADJUSTMENT ...
Page 122: ...C H A P T E R MAINTENANCE ...
Page 129: ...C H A P T E R APPENDIX ...
Page 146: ......
Page 147: ......
Page 148: ......
Page 149: ......