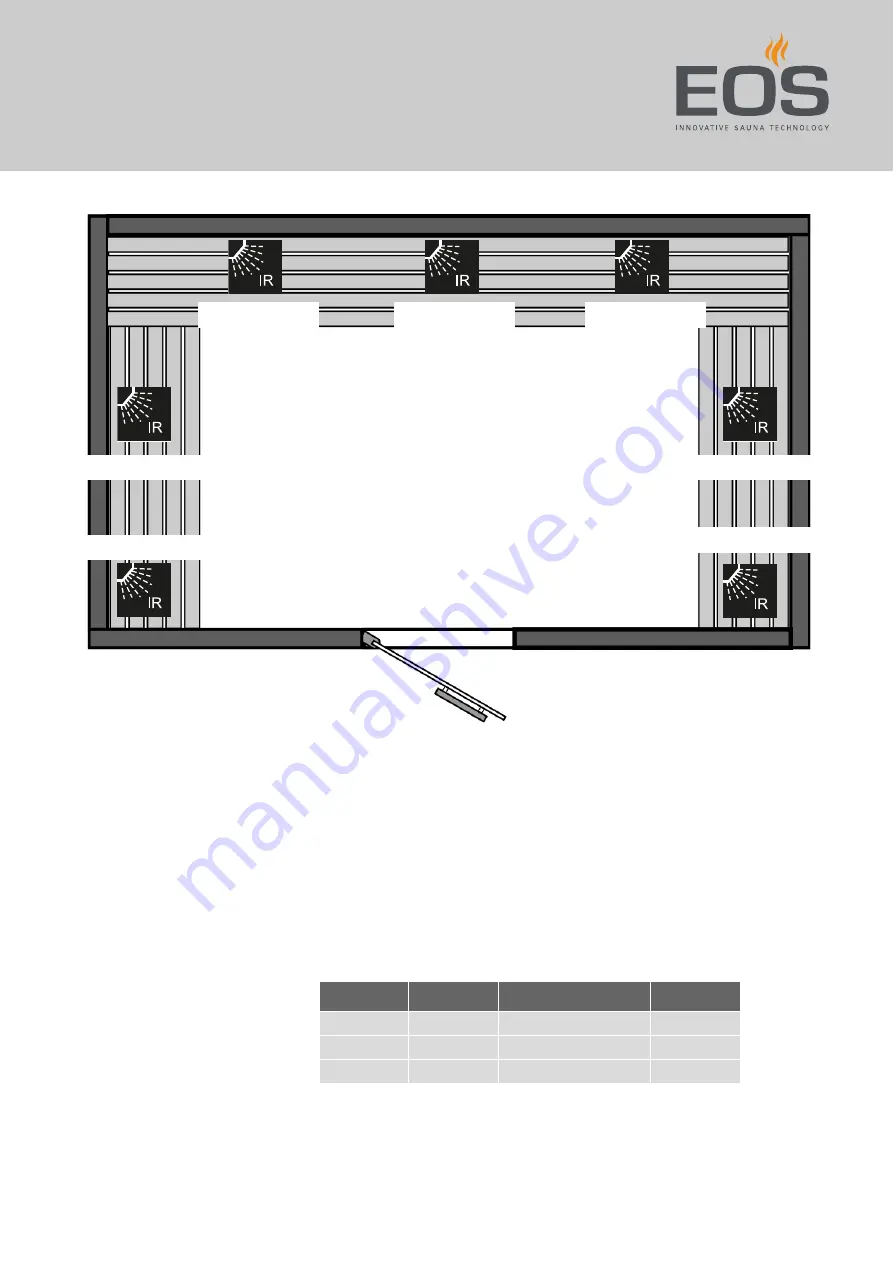
InfraStyle / InfraStyle i - Installation Instructions
71
Commissioning
Example – cabin
The IR emitters in this example have different tasks and should be con-
trolled together in so-called channel groups.
IR emitters 1, 2 and 3 are emitters for the back. Together their output is
1.5 kW.
IR emitters 4 and 5 are foils for the heating the back with an output of
0.3 kW each. They should heat to an intensity of 66%.
IR emitters 6 and 7 are corner emitters. Both emitters have an output of
0.5 kW. They should switch off once the cabin temperature reaches
65°C.
IR emitter 1
IR emitter 3
IR emitter 4
IR emitter 5
IR emitter 2
IR emitter 6
IR emitter 7
Emitter
Connection Jumper
Channel
1, 2, 3
IR-1
Emitter (R)
A
4, 5
IR-2
Foil (F)
B
6, 7
IR-3
C