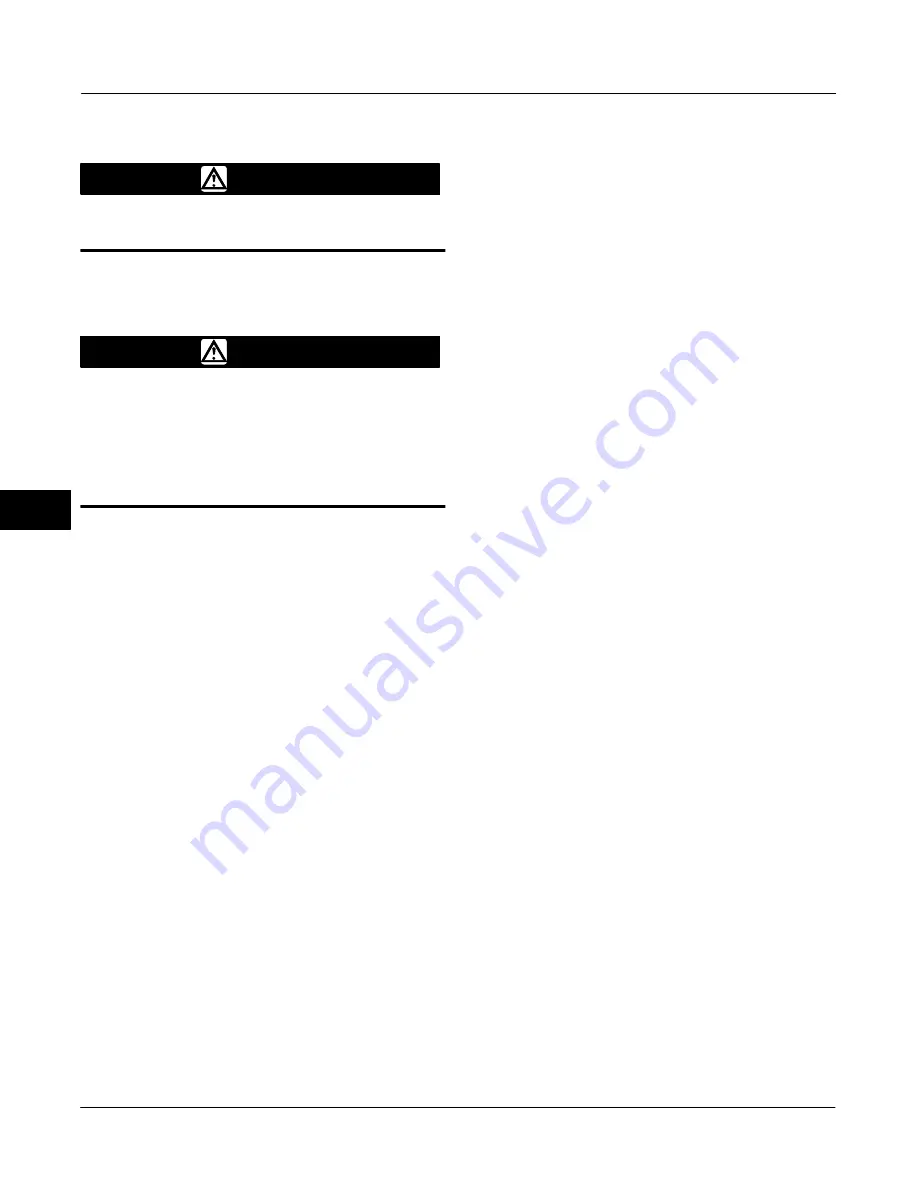
DVC6000f Digital Valve Controllers
December 2009
7-10
Travel Sensor
WARNING
Refer to the Maintenance WARNING at
the beginning of this section.
Replacing the travel sensor requires removing the
digital valve controller from the actuator.
WARNING
To avoid personal injury or property
damage caused by fire or explosion,
remove power to the instrument
before replacing the travel sensor in
an area which contains a potentially
explosive atmosphere or has been
classified as hazardous.
Disassembly
DVC6010f Digital Valve Controller and
DVC6015 Remote Feedback Unit
Refer to figure 8-2 for DVC6010f and 8-7 for DVC6015
key number locations.
1. Remove piping and fittings from the instrument.
2. Disconnect the adjustment arm from the connector
arm and the feedback arm (see figures 2-1 and 2-2).
3. Remove the instrument from the actuator.
4. Loosen the screw (key 80) that secures the
feedback arm (key 79) to the travel sensor shaft.
5. Remove the feedback arm (key 79) from the travel
sensor shaft.
If disassembling a DVC6010f digital valve controller,
use step 6a. If disassembling a DVC6015 remote
feedback unit, use step 6b.
6. a. Separate the module base from the housing by
performing the Removing the Module Base procedure.
b. Disconnect the three potentiometer assembly
wires from the terminals.
7. Remove the screw (key 72) that fastens the travel
sensor assembly to the housing.
8. Pull the travel sensor assembly (key 223) straight
out of the housing.
DVC6020f Digital Valve Controller and
DVC6025 Remote Feedback Unit
Refer to figure 8-3 for DVC6020f and 8-8 for DVC6025
key number locations.
1. Remove piping and fittings from the instrument.
2. Remove the digital valve controller from the
actuator.
3. Disconnect the bias spring (key 82) from the
feedback arm assembly (key 84) and the arm
assembly (key 91). Remove the mounting bracket (key
74) from the back of the digital controller. If the torsion
spring (key 93) needs to be replaced, ensure that the
shaft on which it is installed is smooth and free of
rough spots. Replace the entire feedback arm
assembly if necessary.
4. Loosen the screw (key 80) that secures the arm
assembly to the travel sensor shaft.
5. Remove the arm assembly (key 91) from the travel
sensor assembly (key 77) shaft.
If disassembling a DVC6020f digital valve controller,
use step 6a. If disassembling a DVC6025 remote
feedback unit use step 6b.
6. a. Separate the module base from the housing by
performing the Removing the Module Base procedure.
b. Disconnect the three potentiometer assembly
wires from the terminals.
7. Remove the screw (key 72) that fastens the travel
sensor assembly to the housing.
8. Pull the travel sensor assembly (key 223) straight
out of the housing.
DVC6030f Digital Valve Controller and
DVC6035 Remote Feedback Unit
Refer to figure 8-4 for DVC6030f and 8-9 for DVC6035
key number locations.
1. Remove piping and fittings from the instrument.
2. Remove the digital valve controller from the
actuator. Loosen the screw (key 80) that secures the
feedback arm (key 79) to the travel sensor shaft.
Remove the feedback arm from the travel sensor
shaft.
If disassembling a DVC6030f digital valve controller
use step 3a. If disassembling a DVC6035 remote
feedback unit use step 3b.
3. a. Separate the module base from the housing by
performing the Removing the Module Base procedure.
b. Disconnect the three potentiometer assembly
wires from the terminals.
4. From within the housing, unscrew the travel sensor
assembly (key 223) from the housing.
7
Summary of Contents for Fisher FIELDVUE DVC6000f
Page 54: ...DVC6000f Digital Valve Controllers December 2009 2 30 2 ...
Page 62: ...DVC6000f Digital Valve Controllers December 2009 4 2 4 ...
Page 127: ...Transducer Block December 2009 4 67 4 ...
Page 141: ...AO Function Block December 2009 4 81 4 ...
Page 207: ...MAI Function Block December 2009 4 147 4 ...
Page 219: ...DO Function Block December 2009 4 159 4 ...
Page 231: ...DI Function Block December 2009 4 171 4 ...
Page 302: ...DVC6000f Digital Valve Controllers December 2009 8 16 8 ...
Page 306: ...DVC6000f Digital Valve Controllers December 2009 A 4 A ...
Page 350: ...DVC6000f Digital Valve Controllers December 2009 E 6 E ...
Page 368: ...DVC6000f Digital Valve Controllers December 2009 F 18 F ...
Page 372: ...DVC6000f Digital Valve Controllers December 2009 Glossary 4 Notes G Glossary ...
Page 382: ...DVC6000f Digital Valve Controllers December 2009 Index 10 F Index ...