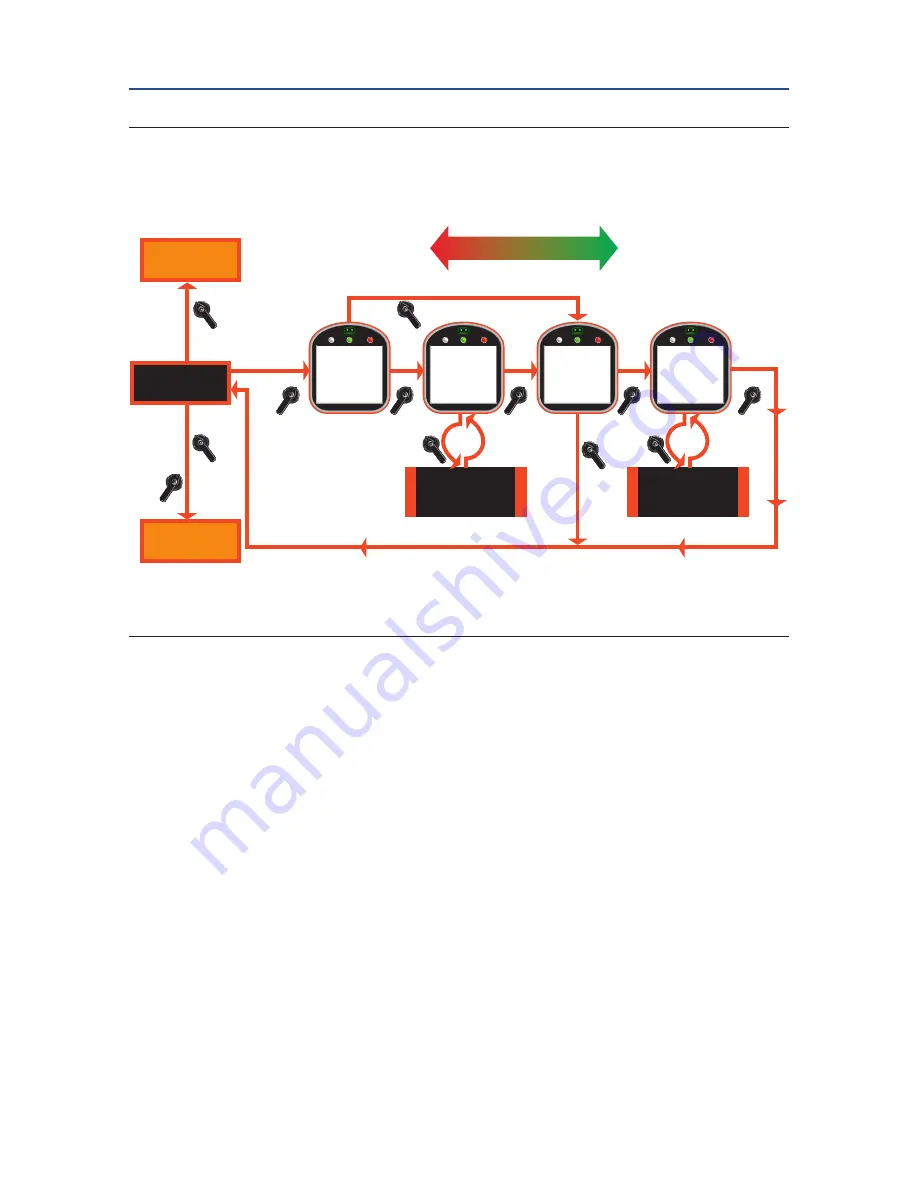
Installation and Operation Manual
E2K-405-0218 Rev. 2
February 2018
43
Section 5: Customizing Actuator Settings
Customizing Actuator Settings
Figure 5-2
Change Display
5.4
Displaying Unit Parameters
The user may view information on the actuator parameters as follows:
1.
At the “
DISPLAY UNIT PARAMETERS?
” prompt answer
YES
.
2.
Use the selector knob (
BACK/NEXT
) to view parameters as shown in
Figure 5-3
.
The tag name, method of control, and network address may be entered or changed via the
“
Change Settings
” mode. See
Section 5.5, Change Settings
.
All other parameters viewed are factory setup and cannot be changed by the user.
NO
Figure 5-2 Change Display
Go to
Figure 5-
15
Go to
Figure 5-
16
YES
YES
Change
Language?
Language?
<xxxxxxxx>
English, Spanish,Portuguese,
Russian, French,Mandarin,
Italian, German
YES
YES
Adjust
Contrast?
YES
No to Adjust
Yes to Accept
Increment 1 to 64
In Step Size of 1
NO
NO
NO
NO
or
Next
BACK
NEXT
BACK
CHANGE
DISPLAY?