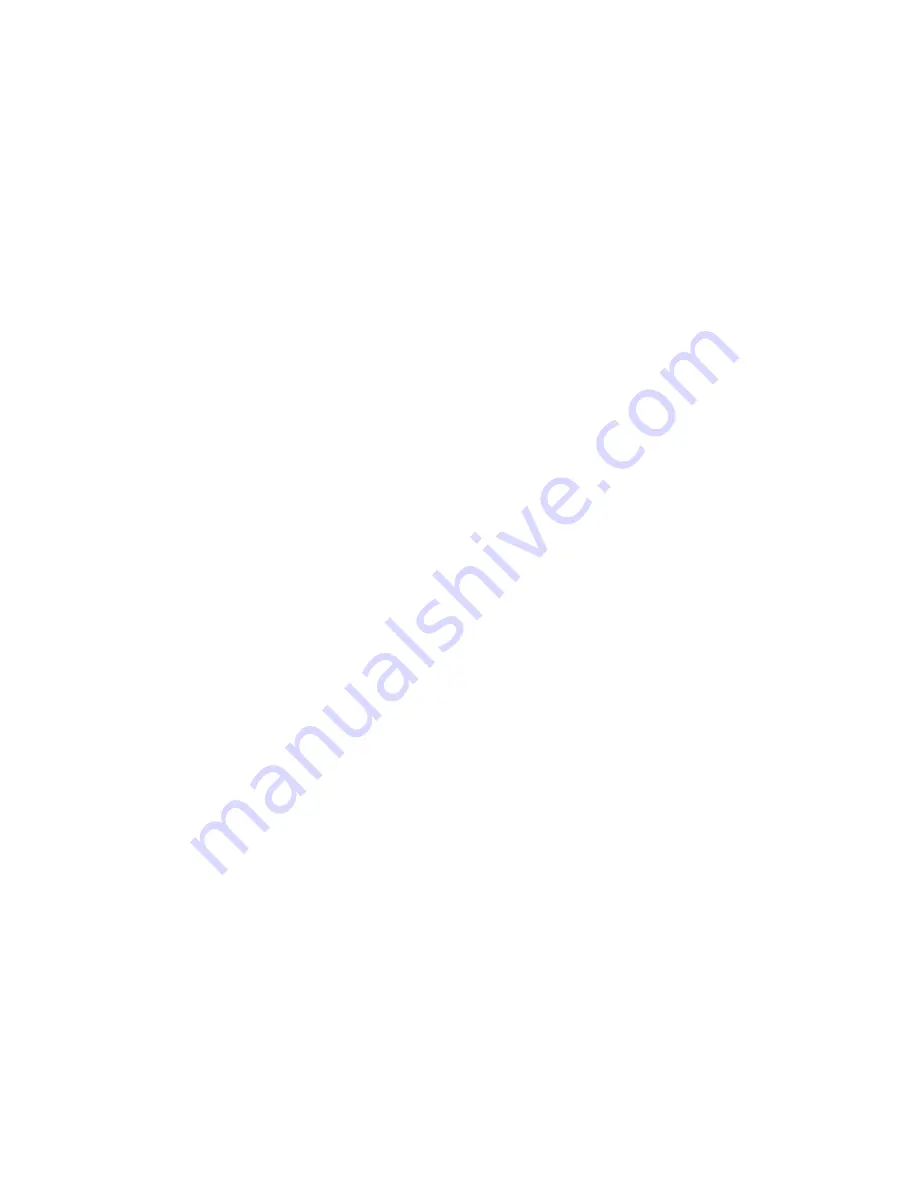
- 8 -
Introduction to the basic positioning drive amplifier
The Positioning Drive amplifier is different from common analog amplifiers in that it includes a
position feedback loop and the electronics to control motion functions. To accomplish this, the
motor uses resolver feedback. The resolver converter electronics in the amplifier develops
velocity and position feedback signals required for high performance and precise velocity and
position control.
In addition the amplifier offers three standard modes of control providing a host of alternatives
for implementing real time motion control.
In the ANALOG TORQUE or VELOCITY mode, the amplifier responds to a conven/-
10 volt signal. Most variable speed drives and servo amplifiers on the market today receive
commands via analog input.
The true power and versatility of the Positioning Drive is best utilized in the additional
positioning control modes. In most applications the user will use one of the following modes of
operation.
In the PULSE mode, the drive responds to a serial pulse train representing externally generated
incremental position change commands. These commands are normally in the form of CW or
CCW directional pulses. This mode is commonly used to control DC stepper motors or numeric
controlled (CNC) machinery.
The INDEXING mode allows up to thirty-two different indexes or positions to be pre-
programmed and stored in a non-volatile memory. These indexes plus other commands such as
STOP and JOG are selected easily by the drive’s parallel input/output (I/O) lines from devices
such as PLCs or operator push buttons. Parallel I/O commands can be used for stand alone
operation or, simultaneously in conjunction with any other two control modes.
Another powerful feature of the INDEXING mode allows ASCII commands through the
standard RS423 serial interface. This interface port allows the user to down load new
dimensional data e.g., position, distance, velocity, etc., and command an internally generated
index using those parameters. These ASCII serial commands are well suited to operation from
the RS232C serial interface on an IBM Personal Computer (PC) or Programmable Logic
Controller (PLC) with ASCII or Basic Module.
For additional stand alone motion control capability, the drive is designed to accept a series of
application oriented modules called “PCM” modules. The PCMs can be attached to any drive by
simply plugging them onto the front. The PCM is designed to share the power supply inside of
the drive and includes 12 additional optically isolated inputs/outputs (making a total of 24).
When attached, the PCM module extends the operation of the Positioning Drive system.
The IOM-1, PCM-1, PCM-2 and PCM-5 modules are designed to be plug-on additions to
EMERSON EMC’s line of Positioning Drives. Each module is intended to enhance a specific
performance characteristic of the positioning drives.
Artisan Technology Group - Quality Instrumentation ... Guaranteed | (888) 88-SOURCE | www.artisantg.com