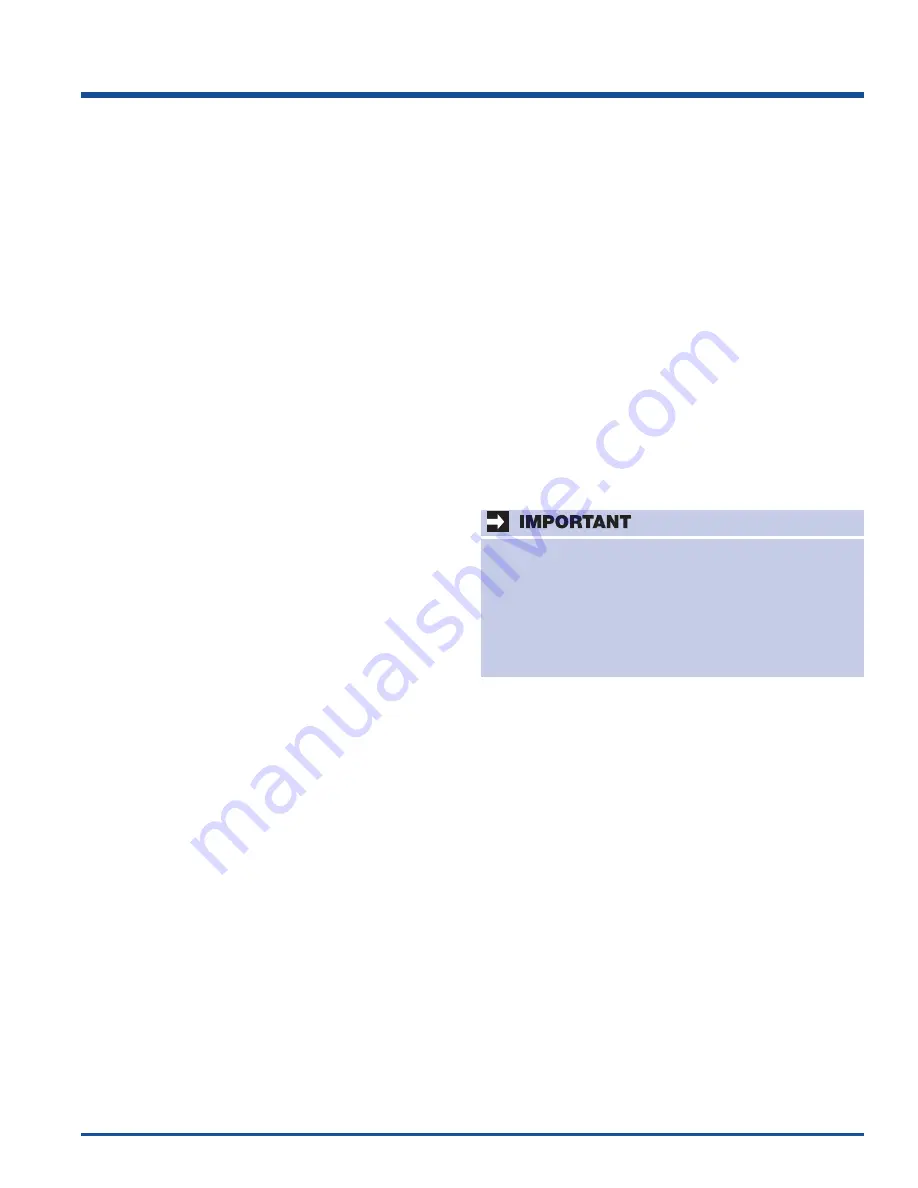
Sealed System
7-23
Service Diagnostic Tips
A prime requisite on the initial contact is: Always allow
the customer to explain the problem. Many times the
trouble can be diagnosed more quickly, based on the
customer’s explanation. Most of all, do not jump to
conclusions until you have heard the full story and have
evaluated the information obtained from the customer.
Then proceed with your diagnosis.
Before starting a test procedure, connect the product
service cord to the power source, through a wattmeter,
combined with a voltmeter. Then make a visual
inspection and operational check of the refrigerator to
determine the following:
1. Is the product properly leveled?
2. Is the product located for proper dissipation of heat
from the condenser? Check recommended spacing
from walls.
3. Feel condenser. With compressor in operation,
condenser should be hot, with gradual reduction in
temperature from entry to exit of condenser.
4. Are door gaskets sealing properly?
(Refrigerators and freezers)
5. Does the door actuate the light switch?
(Refrigerators and freezers)
6. Is evaporator fan properly located on motor shaft?
7. Is the thermostat sensing element properly
positioned?
8. Observe frost pattern on evaporator.
9. Check thermostat knob setting.
10. Inscribe bracket opposite slotted shaft of defrost
timer to determine if timer advances (Refrigerators
and freezers - auto defrost models only).
The service technician should inquire as to the number
of people in the family to determine the service load and
daily door openings. In addition, he should know the
room temperature for refrigerator and freezers. For
air-conditioners, check room size, temperature, amount
of people, windows, and other factors that increase the
load on the product.
After this phase of diagnosis is completed, a thorough
operational check should be made of the refrigeration
system.
Refrigerator and Freezer Air Temperatures
Temperatures are affected by improper door seal, frost
accumulation on the evaporator, service load, ambient
temperature, percent of relative humidity, thermostat
calibration (cut-in and cut-out), location of evaporator fan
blade on motor shaft, and by compressor efficiency.
Line Voltage
It is essential to know the line voltage at the product.
A voltage reading should be taken at the instant the
compressor starts, and also while the compressor is
running. Line voltage fluctuation should not exceed 10%
plus or minus, from nominal rating. Low voltage will
cause overheating of the compressor motor windings,
resulting in compressor cycling on thermal overload, or
the compressor may fail to start. Inadequate line wire
size, and overloaded lines, are common reasons for low
voltage at the product.
Your Country may have regulations or restrictions
governing the discharging of chlorofluorocarbons
(CFC’s) such as R-12 and R-22 to the atmosphere.
Therefore, when discharging or purging the
sealed system, use an approved refrigerant
recovery system.
Summary of Contents for 5995502399
Page 2: ......
Page 56: ...Ice Maker Fresh Food Compartment 4 8 Flow Chart No Ice 1 ...
Page 57: ...Ice Maker Fresh Food Compartment 4 9 Flow Chart No Ice 2 ...
Page 58: ...Ice Maker Fresh Food Compartment 4 10 Flow Chart No Ice 3 ...
Page 59: ...Ice Maker Fresh Food Compartment 4 11 Flow Chart No Ice 4 ...
Page 60: ...Ice Maker Fresh Food Compartment 4 12 Flow Chart No Ice 5 ...
Page 61: ...Ice Maker Fresh Food Compartment 4 13 Flow Chart No Ice 6 ...
Page 62: ...Ice Maker Fresh Food Compartment 4 14 Flow Chart Test 48C ...
Page 63: ...Ice Maker Fresh Food Compartment 4 15 Flow Chart Test 49C ...
Page 64: ...Ice Maker Fresh Food Compartment 4 16 Flow Chart Test 50C ...
Page 65: ...Ice Maker Fresh Food Compartment 4 17 Flow Chart 51C ...
Page 66: ...Ice Maker Fresh Food Compartment 4 18 Flow Chart 52C ...
Page 67: ...Ice Maker Fresh Food Compartment 4 19 Flow Chart 54C ...
Page 68: ...Ice Maker Fresh Food Compartment 4 20 Flow Chart 55C ...
Page 69: ...Ice Maker Fresh Food Compartment 4 21 Flow Chart 56C ...
Page 70: ...Ice Maker Fresh Food Compartment 4 22 Flow Chart 57C ...
Page 71: ...Ice Maker Fresh Food Compartment 4 23 Flow Chart 58C ...
Page 72: ...Ice Maker Fresh Food Compartment 4 24 Flow Chart 59C ...
Page 73: ...Ice Maker Fresh Food Compartment 4 25 Flow Chart 60C ...
Page 74: ...Ice Maker Fresh Food Compartment 4 26 Flow Chart 61C ...
Page 75: ...Ice Maker Fresh Food Compartment 4 27 Flow Chart 62C ...
Page 76: ...Ice Maker Fresh Food Compartment 4 28 Flow Chart 63C ...
Page 77: ...Ice Maker Fresh Food Compartment 4 29 Flow Chart ICE t3 Error ...
Page 92: ...Ice Maker Freezer Compartment 4 44 Step 7 Step 8 Step 9 Step 10 ...
Page 94: ...Ice Maker Freezer Compartment 4 46 Notes ...
Page 97: ...Water System 5 3 Standard Depth Water Schematic Counter Depth Water Schematic ...
Page 166: ...9 1 Wiring Schematics ERF2500 Control Schematic ...
Page 167: ...Wiring Schematics 9 2 PTD Board Ice and Water Module and LED Power Board ...
Page 168: ...Wiring Schematics 9 3 Icemaker Control Board ...
Page 169: ...Wiring Schematics 9 4 YELLOW YELLOW YELLOW Freezer Compartment Ice Maker Schematic ...
Page 170: ...Wiring Schematics Diagram 2419559 Rev C ...
Page 171: ...Wiring Schematics Diagram 2419801 Rev C ...
Page 172: ...Wiring Schematics Non Dispenser Models Diagram 242046100 Rev A ...
Page 173: ...Wiring Schematics Non Dispenser Models Diagram 242046700 Rev A ...