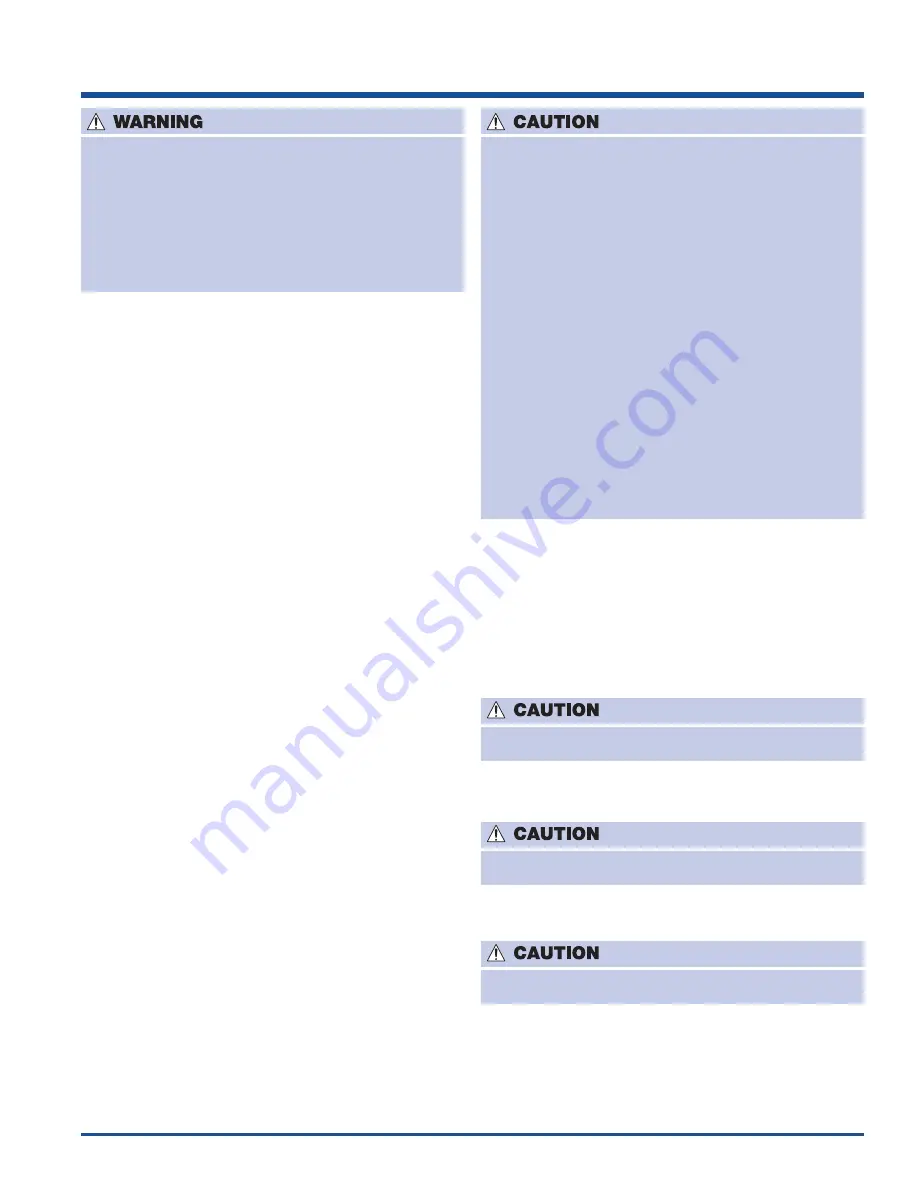
Sealed System
7-9
If dry nitrogen or carbon dioxide is not available.
Follow instructions 1 through 3, then use 4 and 5 listed
below as an alternative method.
4. Connect gauges to charging hose fittings. Pull a
vacuum on each side of the system.
5. Leave the vacuum on each side of the system for 24
hours. Any loss of vacuum is an indication of a leak.
Compressor Replacement
Before installing new compressor, check for possible
system contamination by obtaining an oil sample from
the old compressor. On R-134a systems use an oil test
kit to check for contamination. If oil has a burned odor or
shows contamination (dark color), the system should be
flushed to remove as much of the contamination as
possible before installing a new compressor and
filter-drier. If this contamination is allowed to remain
in the system it will mix with the new oil causing it to
become contaminated and damage the new compressor,
or cause a restriction in the filter-drier or cap tube.
NEVER PRESSURIZE WITH OXYGEN. NEVER
OPEN A HIGH PRESSURE TANK UNLESS IT IS
EQUIPPED WITH A PRESSURE REGULATOR.
NEVER PUT HIGH PRESSURE ON THE DOME OF
THE COMPRESSOR - IT MIGHT EXPLODE.
MAKE SURE GAUGE FITTINGS ARE IN GOOD
CONDITION AND DO NOT LEAK.
Use extreme care when using Dry Nitrogen to flush
systems. Pressure in nitrogen cylinder could be
as high as 2000 psi. Nitrogen cylinder must be
equipped with approved pressure regulator and
pressure relief valve. Ensure that your hoses have
adequate ratings for pressure involved and that all
of your equipment is in good condition.
When flushing with nitrogen there MUST Be a
pressure regulator on the tank with the maximum
pressure on the lowside of the sealed system
(evaporator) at 150 PSI and at the High side, 300
PSI.
The end of the flushing hose on this tank
regulator must be equipped with a hand shut-off
valve (Robinair No. 40380). Close hand shut-off
valve and adjust nitrogen regulator to correct
pressure before proceeding with flushing
procedure.
1. Remove compressor and filter-drier. Connect
process coupling to outlet tube of condenser.
2. Fasten cloth over other end of coil to prevent old oil
from spraying over room.
3. Connect hand shut-off valve on flushing hose to
process
coupling.
4. Slowly open hand shut-off valve and allow nitrogen
to flow through condenser until discharge is clear.
5. Disconnect cap tube from evaporator. Flush
evaporator in same manner as condenser.
6. Flush cap tube. This is only possible if you have a
proper service valve adapter.
7. Reassemble system.
Flushing The System With
Nitrogen
It is recommended that system be flushed with dry
Nitrogen. However, if refrigerant is used to flush the
system you must look at the serial plate to see what
type of refrigerant is used in the system. This is the only
refrigerant that can be used to flush the system and it
must be recovered.
DO NOT exceed 300 Psi.
DO NOT exceed 300 Psi.
DO NOT exceed 150 Psi.
Summary of Contents for 5995502399
Page 2: ......
Page 56: ...Ice Maker Fresh Food Compartment 4 8 Flow Chart No Ice 1 ...
Page 57: ...Ice Maker Fresh Food Compartment 4 9 Flow Chart No Ice 2 ...
Page 58: ...Ice Maker Fresh Food Compartment 4 10 Flow Chart No Ice 3 ...
Page 59: ...Ice Maker Fresh Food Compartment 4 11 Flow Chart No Ice 4 ...
Page 60: ...Ice Maker Fresh Food Compartment 4 12 Flow Chart No Ice 5 ...
Page 61: ...Ice Maker Fresh Food Compartment 4 13 Flow Chart No Ice 6 ...
Page 62: ...Ice Maker Fresh Food Compartment 4 14 Flow Chart Test 48C ...
Page 63: ...Ice Maker Fresh Food Compartment 4 15 Flow Chart Test 49C ...
Page 64: ...Ice Maker Fresh Food Compartment 4 16 Flow Chart Test 50C ...
Page 65: ...Ice Maker Fresh Food Compartment 4 17 Flow Chart 51C ...
Page 66: ...Ice Maker Fresh Food Compartment 4 18 Flow Chart 52C ...
Page 67: ...Ice Maker Fresh Food Compartment 4 19 Flow Chart 54C ...
Page 68: ...Ice Maker Fresh Food Compartment 4 20 Flow Chart 55C ...
Page 69: ...Ice Maker Fresh Food Compartment 4 21 Flow Chart 56C ...
Page 70: ...Ice Maker Fresh Food Compartment 4 22 Flow Chart 57C ...
Page 71: ...Ice Maker Fresh Food Compartment 4 23 Flow Chart 58C ...
Page 72: ...Ice Maker Fresh Food Compartment 4 24 Flow Chart 59C ...
Page 73: ...Ice Maker Fresh Food Compartment 4 25 Flow Chart 60C ...
Page 74: ...Ice Maker Fresh Food Compartment 4 26 Flow Chart 61C ...
Page 75: ...Ice Maker Fresh Food Compartment 4 27 Flow Chart 62C ...
Page 76: ...Ice Maker Fresh Food Compartment 4 28 Flow Chart 63C ...
Page 77: ...Ice Maker Fresh Food Compartment 4 29 Flow Chart ICE t3 Error ...
Page 92: ...Ice Maker Freezer Compartment 4 44 Step 7 Step 8 Step 9 Step 10 ...
Page 94: ...Ice Maker Freezer Compartment 4 46 Notes ...
Page 97: ...Water System 5 3 Standard Depth Water Schematic Counter Depth Water Schematic ...
Page 166: ...9 1 Wiring Schematics ERF2500 Control Schematic ...
Page 167: ...Wiring Schematics 9 2 PTD Board Ice and Water Module and LED Power Board ...
Page 168: ...Wiring Schematics 9 3 Icemaker Control Board ...
Page 169: ...Wiring Schematics 9 4 YELLOW YELLOW YELLOW Freezer Compartment Ice Maker Schematic ...
Page 170: ...Wiring Schematics Diagram 2419559 Rev C ...
Page 171: ...Wiring Schematics Diagram 2419801 Rev C ...
Page 172: ...Wiring Schematics Non Dispenser Models Diagram 242046100 Rev A ...
Page 173: ...Wiring Schematics Non Dispenser Models Diagram 242046700 Rev A ...