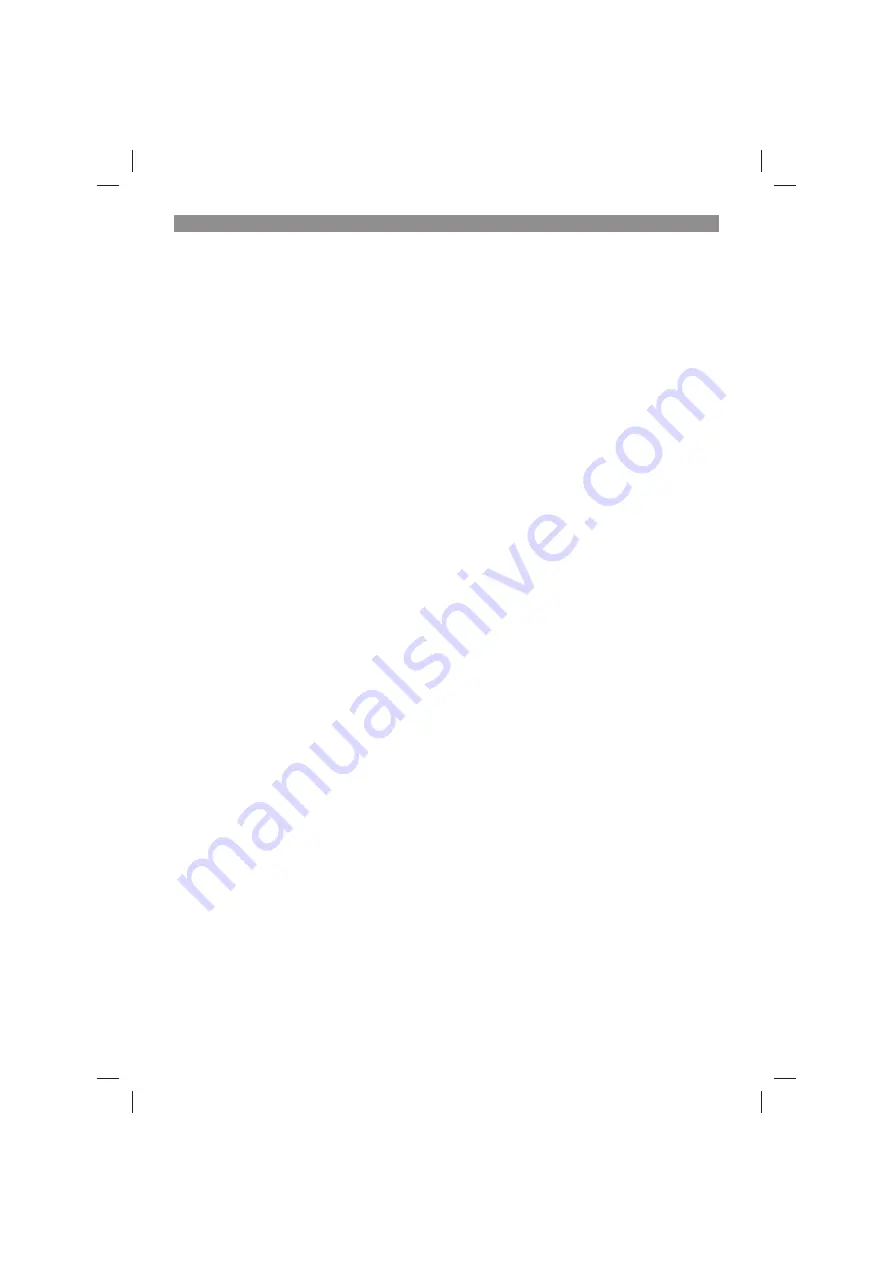
GB
- 22 -
tack the plastic parts of the equipment. Ensu-
re that no water can seep into the device. The
ingress of water into an electric tool increases
the risk of an electric shock.
7.2 Maintenance
Important: Switch o
ff
the machine immedia-
tely and contact an authorized dealer in the
following cases:
•
In the event of unusual vibrations or noise.
•
If the engine appears to be overloaded or
misfires.
•
More information can be found in section 4
“Technical data and service manual for petrol-
powered equipment”.
7.2.1 Air
fi
lter maintenance
•
Check the air filter and filter oil before every
use, clean the air filter, replace if necessary.
•
Remove the filter element (Fig. 8a-8b).
•
Do not use abrasive cleaning agents or petrol
to clean the element. If the filter element is
soaked with oil, squeeze the oil out.
•
Replace the filter element (A) if it is heavily
soiled or damaged.
•
Fill engine oil into the air filter box (B) up to
the mark (C). Take care not to tilt the machine
too much or oil will run out of the air filter box.
•
Assemble in reverse order.
7.2.2 Spark plug maintenance
Check the spark plug for dirt and grime after 10
hours of operation and if necessary clean it with
a copper wire brush. Thereafter service the spark
plug after every 50 hours of operation.
•
Pull off the spark plug boot (Fig. 9) with a
twist.
•
Remove the spark plug (Fig. 9/Item D) with
the supplied spark plug wrench.
•
Assemble in reverse order.
7.2.3 Changing the engine oil/checking the
engine oil level (before each use)
The engine oil is best changed when the engine
is at working temperature.
•
Remove the oil dip stick (Fig. 10a / Item E)
and the oil drain plug (Fig. 10b / Item F).
•
Drain the warm engine oil into a drip tray.
•
Fill in engine oil up to the top mark on the oil
dip stick (Fig. 10c/H).
•
Important: Do not screw in the dip stick when
you check the oil level, simply insert it as far
as the thread (H = Max. / L = Min.).
•
Dispose of the waste oil properly.
7.2.4 Adjusting the Bowden wires
In the working setting it should be possible to
push the clutch lever up to the push bar without
this requiring much e
ff
ort. If the Bowden wire is
too taut for this, it must be extended. To do this,
undo the lock nut opposite the main cable, extend
the screw connector and then tighten the lock nut
again (see Fig. 6b/Item G). If the star-type hoes
no longer rotate, the screw connector will have to
be shortened (as described above).
7.2.5 Changing the gearing oil/checking for
oil loss from the gearing (visual check
before each use)
The oil is best changed when the gearing is at
working temperature. Carry out the
fi
rst oil change
after 20 hours in operation, then at regular inter-
vals of 50 hours.
•
Open the oil cap (Fig. 2) (G) and the oil drain
plug (Fig. 2) (E). Drain the warm oil into a drip
tray.
•
Top up with oil.
•
Dispose of the waste oil properly.
The gear unit is driven by a V-belt. The gear unit
can be repaired if this should become necessary.
If repairs are necessary, please contact our custo-
mer service center.
7.3 Storage
Empty the fuel tank before you decommission the
machine for a lengthy period of time. Clean the
machine and coat all metal parts with a thin
fi
lm of
oil to protect them from rusting. Store the machine
in a clean, dry room.
7.4 Ordering replacement parts:
Please quote the following data when ordering
replacement parts:
•
Type of machine
•
Article number of the machine
•
Identification number of the machine
•
Replacement part number of the part required
For our latest prices and information please go to
www.Einhell-Service.com
Anl_GC_MT_4280_SPK13.indb 22
Anl_GC_MT_4280_SPK13.indb 22
20.09.2021 11:29:46
20.09.2021 11:29:46