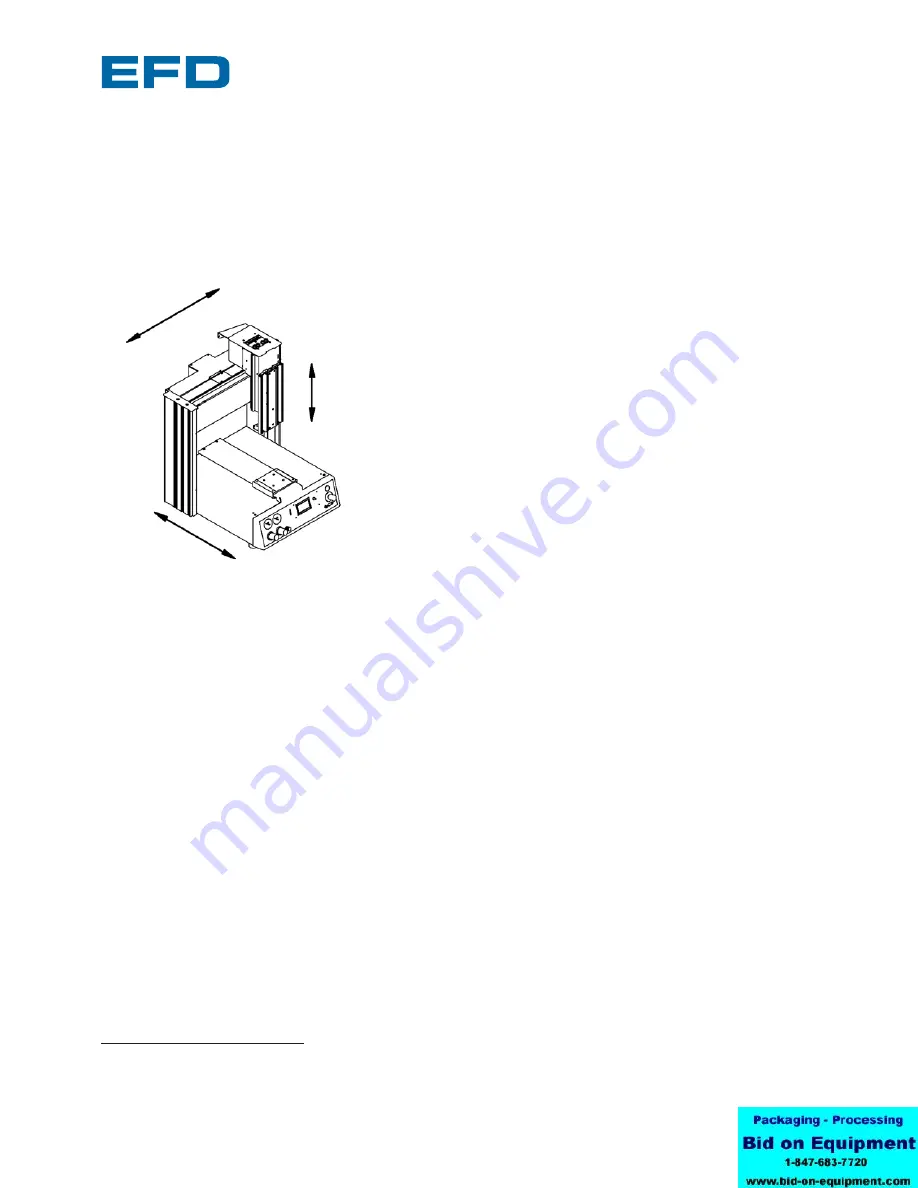
®
A NORDSON COMPANY
Ultra TT User's Guide
Version 1.2
1.2
MACHINE MOVEMENTS
The Ultra TT dispensing system uses an advanced microprocessor to simultaneously control three
axes of motion. An optical encoder feedback system provides closed-loop control to accurately
position the dispensing tip whether dispensing lines, dots or contoured paths.
The Ultra TT Automation system is a three-axis
fluid
dispensing
platform. The three degrees of freedom
provided are X/Y/Z. The motions are indicated in the figure
to the left.
The actual strokes of these axes vary depending on the
model. The X-axis movement is side to side. The Y-axis
movement is forward and backward, while the Z-axis
movement is up and down. The mechanical home is
determined by the location of each axes’ home sensor.
In the case of the Ultra TT, the home position is with the
X-axis to the left, Y-axis to the back and Z-axis is up.
1.3
A TYPICAL OPERATION
A typical operation is described below. Note that setup and programming procedures are not
included in the description.
• The part(s) is manually loaded and secured onto the tooling plate
5
.
• Operator activates the system by pressing the start button on the front of the machine.
• The dispensing head then moves to the programmed X/Y position and the height sensor
probe is lowered to establish the correct dispense height based upon the dot or line
parameter dispense gap. If the height sensor is disabled, then the dispensing head simply
moves to the preprogrammed dispense height.
• Fluid is dispensed onto the part, according to the pre-programmed dispensing pattern.
• Once the dispensing procedure is complete, the dispensing head will move back to its
preprogrammed park location.
• When the tooling plate returns to the park location, the completed part can now be
removed from the tooling plate.
• The process is then repeated.
16
5
Purchased from EFD or User to supply their own.
X Axis
Y Axis
Z Axis