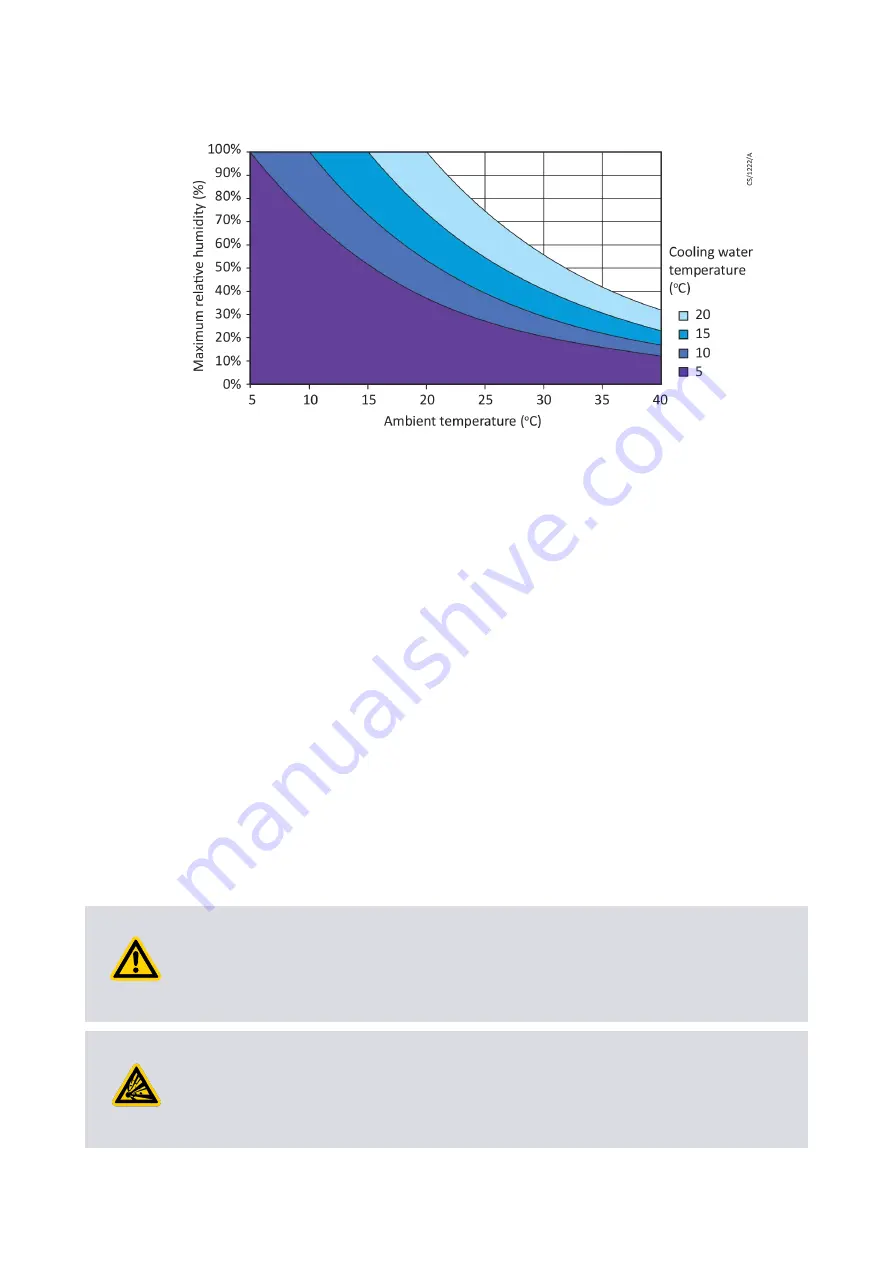
Figure 11 Maximum relative humidity to avoid condensation with water cooling
3.6 Electrical data
The nEXT pumps can be operated by the customers system or by the manufacturer's TIC
Turbo Instrument Controller, TIC Turbo Controller or TAG Controller.
If using the customer system, use an applicable, pre
‑
approved, UL / CSA rated 24
‑
48 V
d.c. power supply. The size of the power supply depends on the application and the
power limit configured in the nEXT pump. The rate of increase in the pump speed is
dependent on the power limit setting. The power limit setting overrides the necessary
power supply setting. If serial communication is available, the power limit setting of the
pump can be selected.
Refer to
Table: Logic interface technical data
for the maximum power limit settings for
the pumps. If the rapid cycling of the pump is necessary for an application, you can get
faster rate of increase in the pump speed if the power supply supplies higher current, up
to a maximum in accordance with
Table: Logic interface technical data
If the power limit setting is not adjustable, use a power supply capable to supply
sufficient current to meet the manufacturer's factory default power limit setting shown
3.7 Pumping media
WARNING: DANGEROUS GASES
Risk of asphyxiation. Release the dangerous gases and gas mixtures safely. Do not
expose people to the gases. Pump the hazardous gases or vapour as per safety
recommendations given by supplier.
WARNING: PYROPHORIC OR EXPLOSIVE GASES
Risk of explosion. Do not use the nEXT pump to pump pyrophoric or explosive gas
mixtures as the pump is not applicable for this purpose. The pump and its
connections are not designed to contain an explosion.
07/2021 - ©Edwards Limited
Page 24
B8G000880_E
B8G000880_E - Technical data
Summary of Contents for nEXT 55
Page 110: ...This page has been intentionally left blank...
Page 114: ...This page has been intentionally left blank...
Page 115: ...This page has been intentionally left blank...
Page 116: ...edwardsvacuum com...