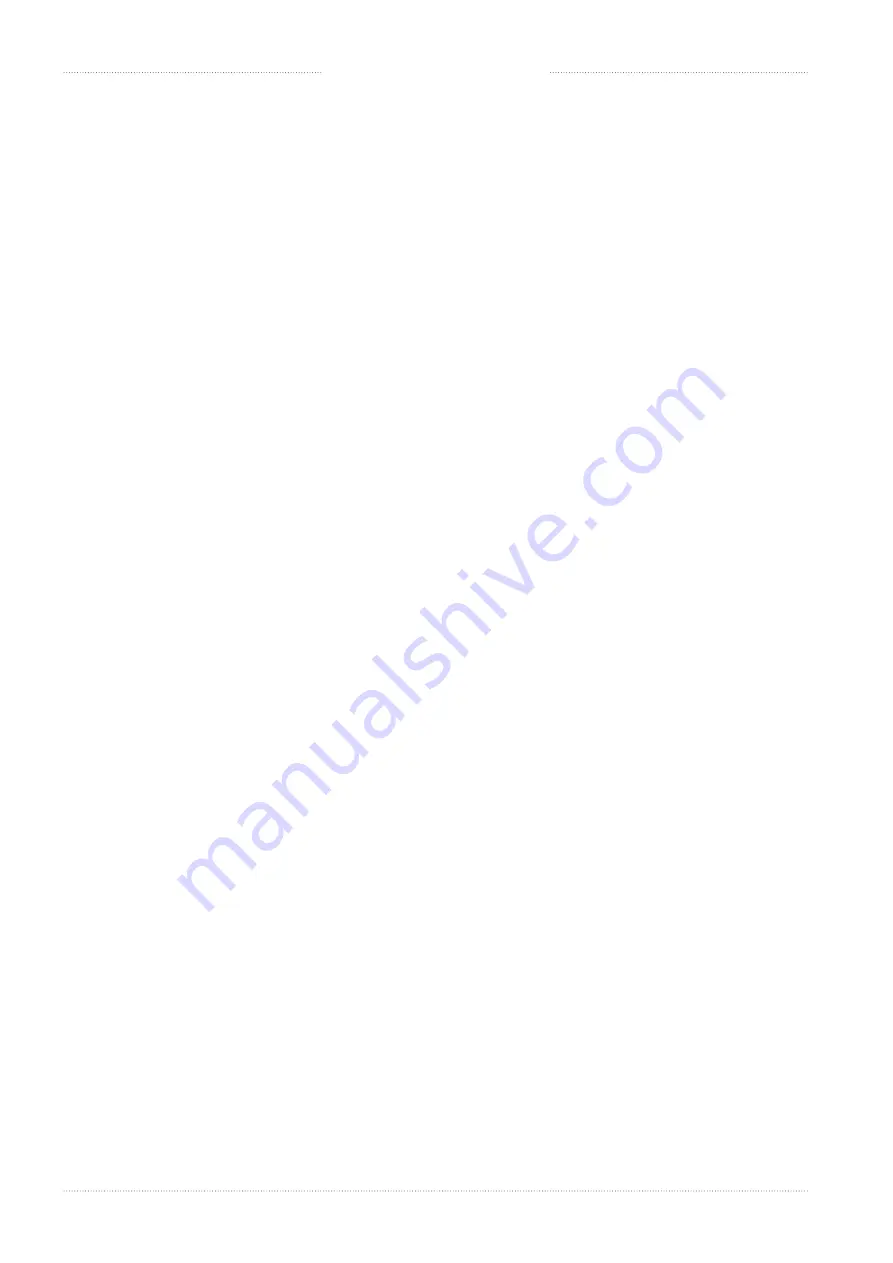
40
2021-09-21 | ECKOLD AG
Kraftformer KF 800
8.3.1.2
Damage (visual check)
• Disconnect the air supply.
• Check the product for damage.
In the case of minor damage:
• Inform the maintenance service of your company or the customer service department of
the machine manufacturer.
• Get the damage repaired.
In the case of damage which a
ff
ects safety:
• Let interrupted the air supply.
• Ensure that operation with the product is not resumed (e.g. using warning signs).
• Get the damage repaired immediately by the maintenance service of your company, or through the
customer service department of the machine manufacturer.
8. Maintenance
8.3.1.3
Observe excessively noises
• Pay attention to excessively loud noises which are not part of normal operation.
If you hear excessively loud noises:
• Disconnect the air supply.
• Inform the maintenance service of your company or the customer service department of the machine
manufacturer.
• Get the damage repaired.
8.3.1.4
Check the tools for damage
• Disconnect the air supply.
• Check the tools for visible damage.
If the tools are damaged:
• Replace the damaged tool.
8.3.1.5
Check the tools for secure fit
• Disconnect the air supply.
• Check to see if the tools sit securely.
If the tools are loose:
• Install the loose tool properly.
Summary of Contents for KRAFTFORMER KF 800
Page 48: ...48 2021 09 21 ECKOLD AG Kraftformer KF 800 8 Maintenance...
Page 52: ...52 2021 09 21 ECKOLD AG Kraftformer KF 800 9 Appendix 9 5 EC declaration of conformity...
Page 70: ...70 2021 09 21 ECKOLD AG Kraftformer KF 800 12 Pneumatikschema...
Page 71: ...71 2021 09 21 ECKOLD AG Kraftformer KF 800 Notizen Notes...
Page 72: ...FDR MAKERS SINCE 1957...