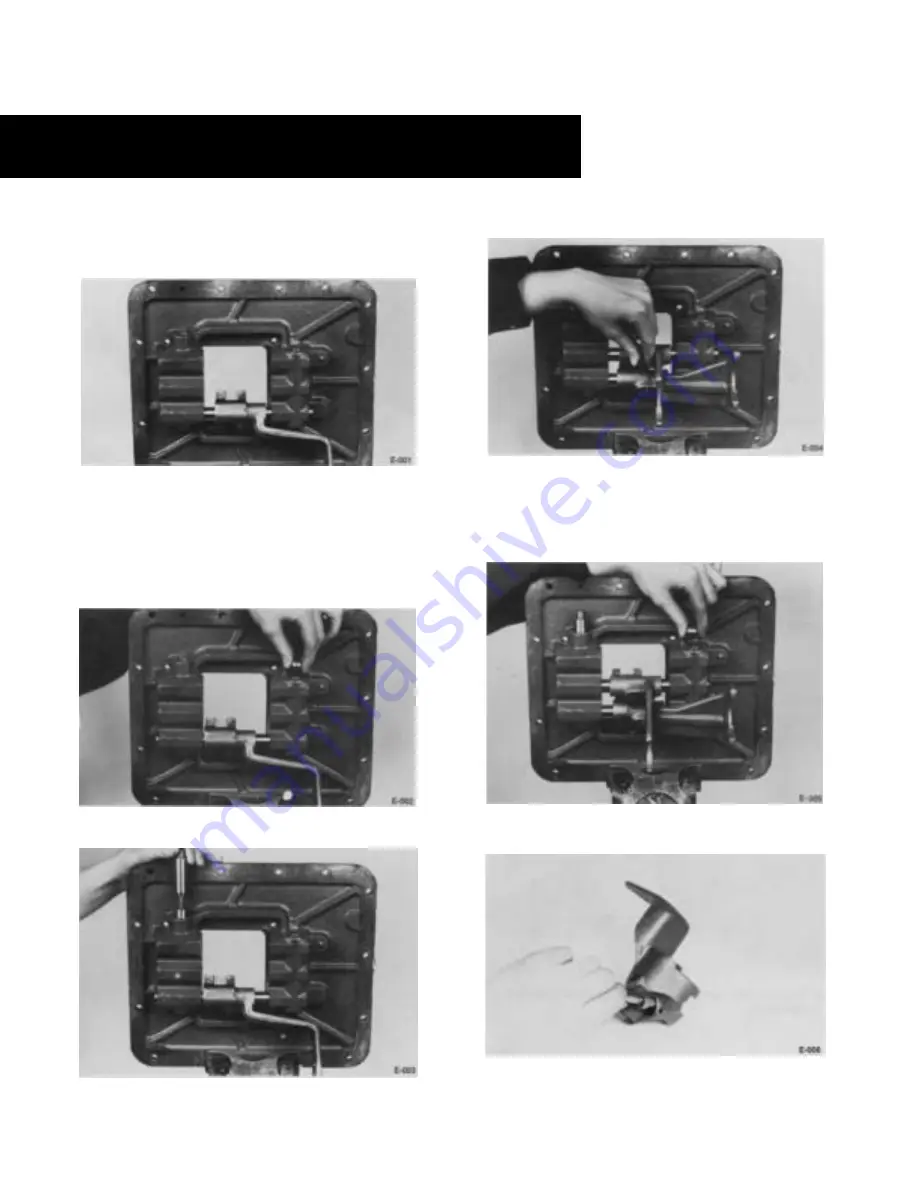
IV. SHIFTING BAR HOUSING
A. To Reassemble the Shifting Bar
Housing Assembly.
1. Place the housing in a vise with the front of
housing to the right.
2. Install the 4th-5th speed shift bar in bottom bore
with neutral notches to the front, installing yoke
on bar, fork towards front. Install yoke lock-
screw and safety wire keep bar in neutral posi-
tion.
3. Install interlock ball in vertical bore in front web.
4. Install plunger in vertical bore in rear web.
5. Install the 2nd-3rd speed shift bar in center
bore, and install yoke on bar, Iockscrew hole to
the rear of fork; insert interlock pin in bore in
neutral notch.
Install yoke Iockscrew and safety wire.
6. Install interlock ball in vertical bore in front web.
7. If previously removed, install the reverse-stop
plunger in the reverse yoke. Make sure that the
plunger is fully seated in the bore.
FRONT SECTION REASSEMBLY
Summary of Contents for TRSM0515
Page 1: ...Service Manual Fuller Heavy Duty Transmissions TRSM0515 October 2007...
Page 4: ...DESCRIPTION...
Page 10: ...PREVENTATIVE MAINTENANCE CHECK CHART...
Page 11: ...TORQUE RECOMMENDATIONS...
Page 12: ...Cut 7191D 7 84 TORQUE RECOMMENDATIONS...
Page 13: ...AIR SYSTEM...
Page 25: ...IX GEAR SHIFT LEVER HOUSING I SHIFTING CONTROLS...
Page 87: ......