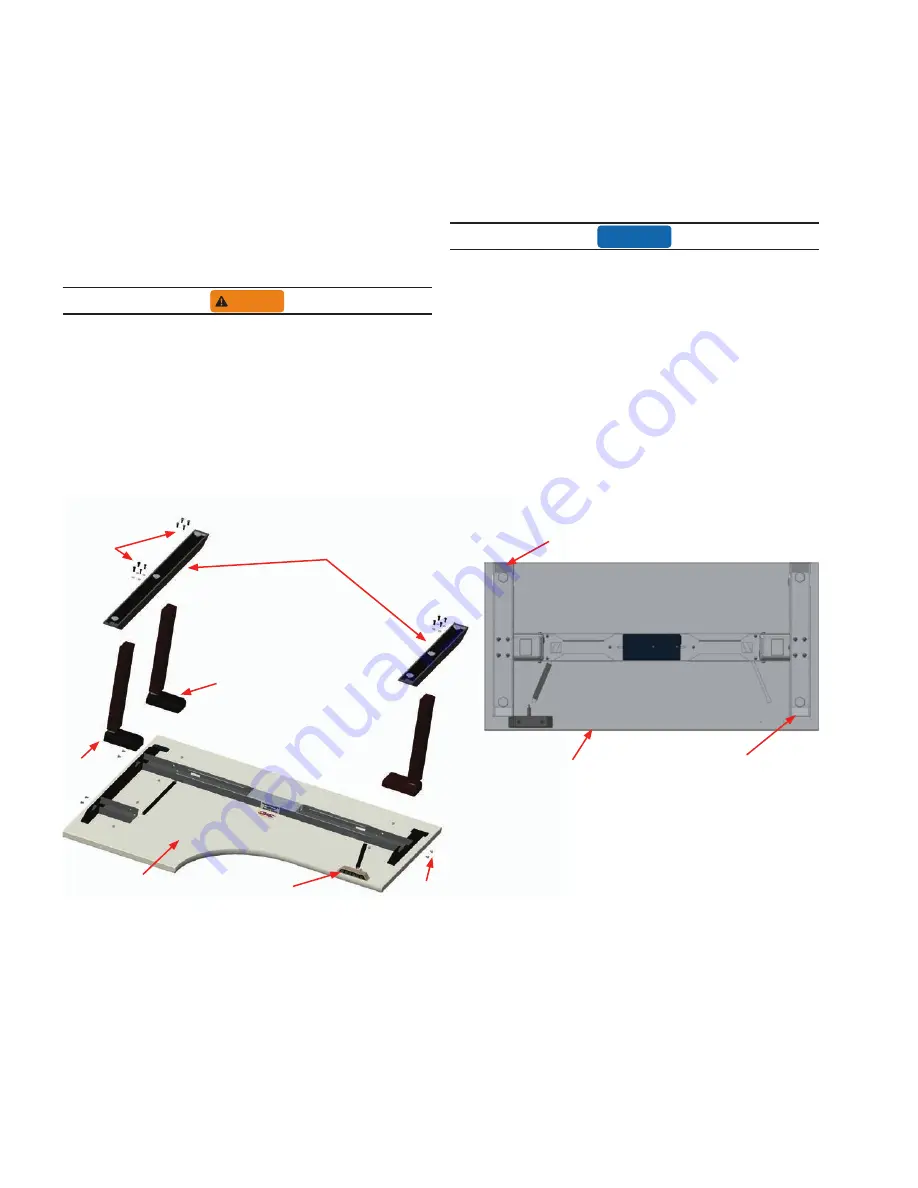
12
Compass sit-to-stand
Installation Manual
COMPASS SIT-TO-STAND INSTALLATION MANUAL
Eaton.com/compass
SECTION III – Assembling the desk
cont’d.
Important considerations
FS desks may be assembled upside down on a flat surface
for easiest access to all screws and components or
assembled upright if desired�
WARNING
During the assembly process, components may become
unstable� Completed desk will be heavy� To reduce the
risk of personal injury and product damage, always ensure
a sufficient amount of personnel are present during the
assembly process and final installation�
•
Mount lift columns to pre-assembled worksurface / stiffener�
Orient the electrical connector towards the center of
worksurface� Secure with (4) M6 x 10 Phillips head screws
(D) into each lift motor housing� No lock washers are used�
Use a #3 Phillips bit. DO NOT TIGHTEN SCREWS.
NOTICE
Start all screws in their respective holes before tightening�
Tighten the end screws first followed by the side screws�
•
Assemble feet to lift columns using (4) M6 x 20 Phillips
Head screw (C) and
5
⁄
16
" lock washers (K) per lift. Use a #3
Phillips bit� Ends of feet will be approximately even with
the back edge of worksurface and offset from the front
(user side) edge by approx� 2"�
C. Free standing desks
Refer to pages 4-5 for additional views of completed desks
•
Assemble foot to lift columns using (4) M6 x 20mm
screws,
5
⁄
16
" lock washers (do not tighten screws)
•
Connect lift column motor cables�
•
Connect AC cord to AC outlet (temporarily)
•
Initialize lift motor system�
•
Cycle lift motors to 18" twice and return to lowest position
- tighten all screws�
•
Turn the entire assembly over and set it on its feet,
carefully move into final installation space� To reduce risk
of property damage, DO NOT drag desk across flooring
surface�
•
Install cable grommets into rectangular holes in
worksurface�
•
Loosen each lift motor’s (4) M6 x 20mm screws�
•
Cycle lift system to 18" twice and return to lowest position
- tighten all screws�
Lift
Column
Front / user
edge
M6 x 20 screws
and
5
⁄
16
" lock
washers
M6 x 10
screws
Control pad
Feet
Electrical
connector
Pre-assembled
Worksurface
BOTTOM ISO VIEW OF CORNER DESK
BOTTOM VIEW OF LINEAR DESK
Feet offset from
front edge
Feet align to
back edge