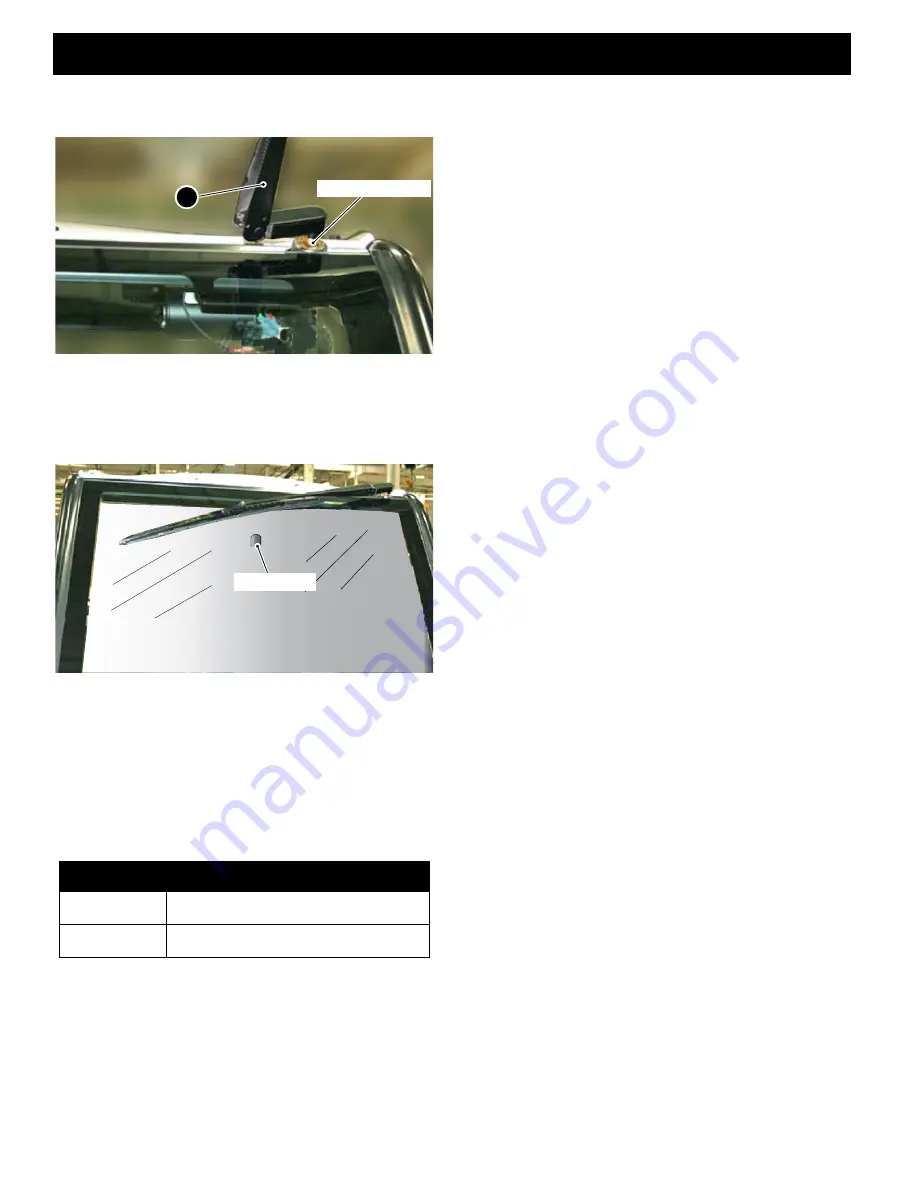
Page N-8
WEATHER PROTECTION
Repair and Service Manual
Read all of Section B and this section before attempting any procedure. Pay particular attention to all Notices, Cautions, Warnings and Dangers.
B
12. Slide wiper arm (1) straight onto the motor pivot shaft
and lower wiper arm onto the glass.
13. Cycle the wiper system to check the wiper position.
The wiper arm should park above the mirror mount but
not off the top of the windshield glass.
14. Cycle the wiper motor again; make sure the blade
does not hit the side seal or the OPS structure. If the
wiper blade is not in correct position on the wind-
shield, push the release tab with a flat screwdriver to
release the wiper arm from the motor pivot shaft,
adjust to correct position and then slide the wiper arm
back onto the wiper pivot shaft, cycle the wiper motor
again and reposition the wiper arm if necessary.
ITEM
TORQUE SPECIFICATION
4, 11
4-10 in. lbs (0.56-1.12 Nm)
7
26-44 in. lbs (3.3-4.5 Nm)
1
Motor Pivot Shaft
Mirror Mount