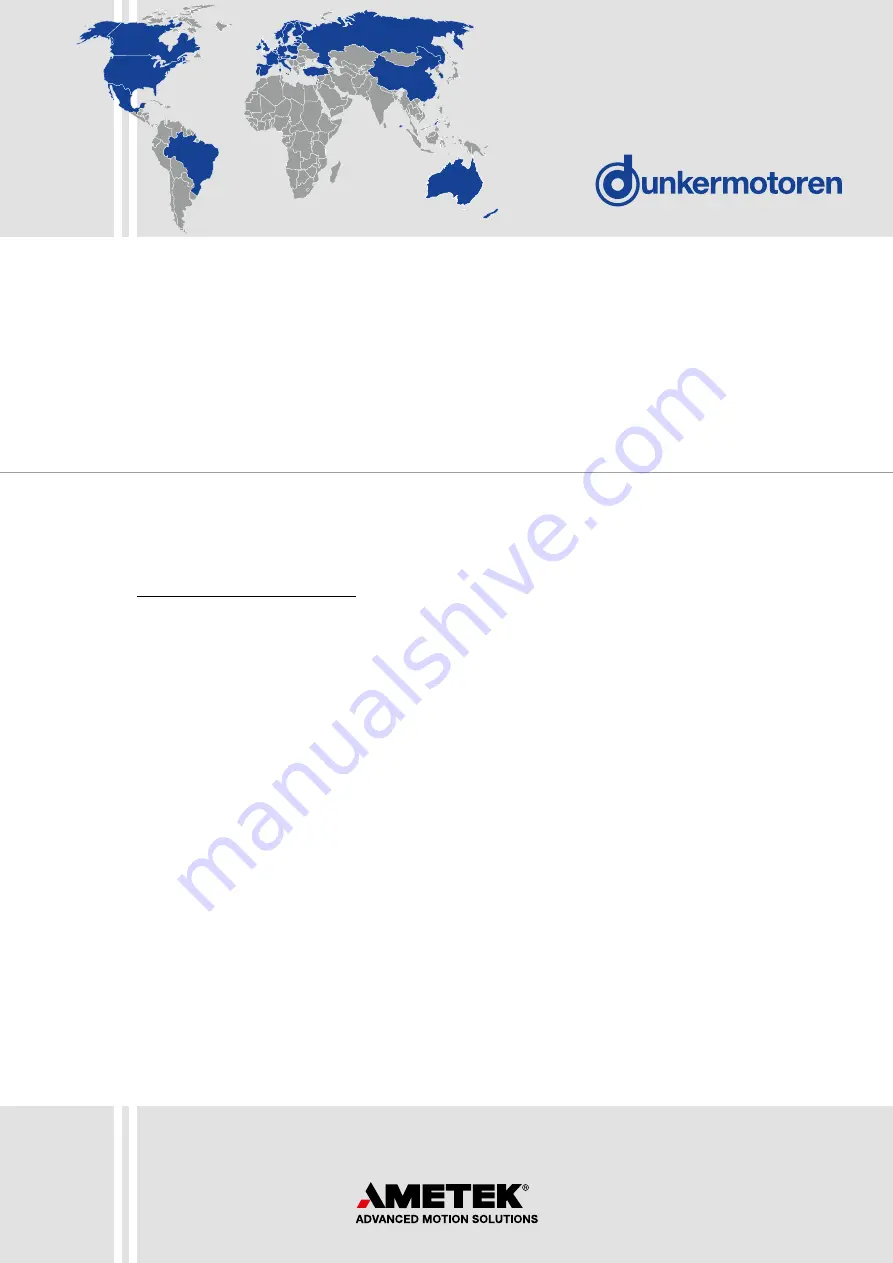
User guide
Dunkermotoren GmbH | Allmendstraße 11 | D-79848 Bonndorf/ Schwarzwald
Phone +49 (0) 7703 930-0 | Fax +49 (0) 7703 930-210/ 212 | [email protected]
Version 08/2017
Operating Manual ServoTube 11 Module
Publication Ref: UM03017/B
Betriebanaleitung ServoTube 11 Module
Publikation Ref: UM03017/B
ServoTube 11 Module