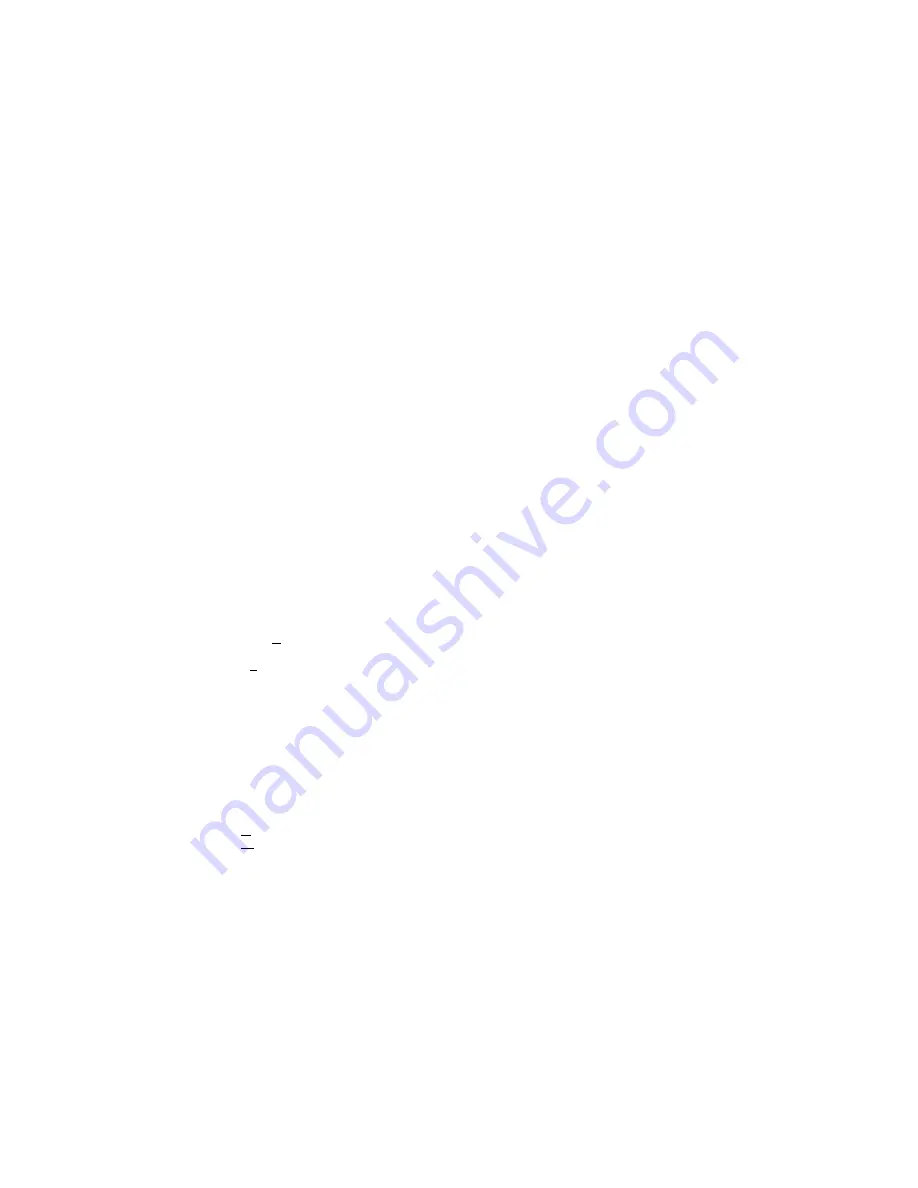
MAINTENANCE
COMPRESSOR
ordered. If you purchased start-up service, then after the
installation has been completed and checked, Form 9180
must be filled out and sent to the local Dunham- Bush
representative who sold the unit. Following receipt of this
signed form, a representative will be sent to the customer.
The purchaser should have competent service and oper-
ating personnel in attendance to assist in the work in-
volved, and also to be trained in the operation and main-
tenance of this unit.
The representative will inspect the installation to deter-
mine whether it meets Dunham-Bush, Inc. requirements,
perform the initial start-up of the installation, determine
whether it is in satisfactory operating condition, and in-
struct specified customer personnel in its operation and
maintenance for the length of time specified in the pur-
chase contract.
NOTE: Sump oil heaters should be energized a minimum
of 24 hours and the oil sump temperature must be at a
minimum of 100°F (38°C) prior to arrival of start-up rep-
resentative. This will ensure that the oil is warm enough
to vaporize any dissolved refrigerant and that the oil is
within the normal operating temperature range.
2. Before starting the compressor(s), check all three phases
of supply voltage, of all legs of the motor. They must be
within ± 10% of the nameplate voltage. Check to be sure
compressor is not running backwards.
3. Start compressor(s), check the gages and note if the
pressures are within the prescribed limits.
1.
OIL LEVEL
- The oil level in the compressor(s) should be
checked periodically, with the compressor stopped. Stage
the unit down until all compressors are off and check the
compressor crankcase sight glass for oil level. If the oil level
is below one half (1/2) the sight glass, oil must be added.
2.
A. RECOMMENDED OIL FOR R-22 MACHINES
Compressor Model Series SSC
A
- The compressor is factory
charged with DB Karlube #10
Oil.
Compressor Model Series SSC
B
- The compressor is factory charged
with DB Karlube #21 Oil.
Do not mix above oils or attempt to operate the screw
compressor with any other oil. It is suggested that a gallon
or more of the appropriate oil be obtained and kept at the
job site.
DB Karlube #10
DB Karlube #21
B.
RECOMMENDED OIL FOR 407C MACHINES
DO NOT USE DB Karlube #10.
Compressor Models SSC
A
use DB Karlube #16 Oil.
Compressor Models SSC
B
use DB Karlube #21 Oil.
Contact factory for price.
The above-listed oils are synthetic lubricants of the Polyol
Ester (POE) type. Due to the complex nature of the POE,
great precaution must be taken to prevent any moisture
from entering the system when servicing or adding oil. POE
oil has a greater solvency for water. Water reacts chemi-
cally with the ester to form acids and alcohols in a process
called “hydrolysis”. POE molecules attract moisture. Mois-
ture removal by evacuation is more difficult because the
POE “holds water more tightly” than mineral oil. Moisture
causes corrosion and copper plating at an unacceptable,
high level. This reaction occurs where temperatures are the
highest within the compressor.
The holding tank must be clean and free of any mois-
ture.
(Evacuate tank to 200 microns). The holding tank
can be a receiver or reclaiming tank of a size large enough
for the total oil change and must be able to withstand
the operating pressure of the system. When adding oil, it
should be transferred from the container supplied to a
holding tank and then evacuated through the vapor port
down to 100 microns with no more than a 50 micron rise
per hour. Do not allow the container to vent to the atmo-
sphere as the transfer must be done through a closed
loop. An oil pump will be required.
PROCEDURE FOR ADDING OIL
Manually close liquid line service valve. Lower return wa-
ter T-stat (4TAS) setting to start the compressor. Run com-
pressor until unit shuts down on low pressure. Place the
control circuit on/off switch in the off position. Locate
the high pressure port adjacent to solenoid valve UL-3
(see drawing page 8) and remove the cap. Attach oil pump
to holding tank high pressure port. Pump oil into this
port until the oil level is 1/2 of the sight glass.
Replace the port cap, open the liquid line shut off valve
and place the control circuit on/off switch in the on posi-
tion. Set the operating T-stat to the normal operating
temperature and reset the low pressure switch.
Oil can also be added, through the suction port of the
compressor, while running the compressor.
3.
COMPRESSOR REPAIRS (internal)
- Contact factory or an
authorized DB Service Agency if a compressor malfunc-
tion is suspected.
4.
COMPRESSOR REPAIRS (External)
- Proper operation of
unloaded start, loading, and unloading is controlled by
solenoid valves UL-1, UL-2 and UL-3. Any of these three (3)
solenoid valves may be repaired or replaced in the field,
as required. Also the compressor crankcase heater may be
replaced.
5. Standard oil acid test kit is not compatible with synthetic
oil. See DB color chart for oil condition.
6
4. Check the refrigerant sightglass at the TX Valve to be sure
it is free of bubbles. If not, charge as required to clean
sight glass.
5. Stage unit down until all compressors are off and check
the compressor crankcase sight glass for oil level. It should
be 1/2 to 3/4 of the compressor sight glass. If not, see pro-
cedure for adding oil on page 7.
6. Restart the compressor. After an hour of operation, the
expansion valve superheat setting should be checked, it
should be between 9°Fand 12°F at full load design condi-
tions. In some instances, it will be necessary to lower the
superheat setting to ensure proper distribution. Turn the
TX valve adjustment stem clockwise to increase the super-
heat setting and counterclockwise to decrease the setting.
Be sure and allow ample time between each adjustment
for the system to re-balance.
7. The electrical control settings should be checked and, if
necessary, reset to those settings indicated on the wiring
diagram. Safety controls are factory set and must be main-
tained at settings indicated on the wiring diagram.
8. The temperatures of the chilled water both in and out,
should be checked to insure the unit is operating within
the desired temperatures.
To prevent moisture entering the system and contaminating
the oil,
extra care is necessary
. Follow the enclosed proce-
dure to add or remove oil from the system.
Summary of Contents for HRSC - D
Page 20: ...19 TYPICAL HRSC 150 POWER WIRING 460 3 60 COMPRESSOR MOTORS 1 2 SEE NOTE 5...
Page 21: ...20 TYPICAL HRSC 150 CONTROL WIRING Electrical Mechanical...
Page 22: ...21 TYPICAL HRSC 150 CONTROL WIRING Optional Micro Computer Controller...
Page 23: ......
Page 29: ......
Page 30: ......