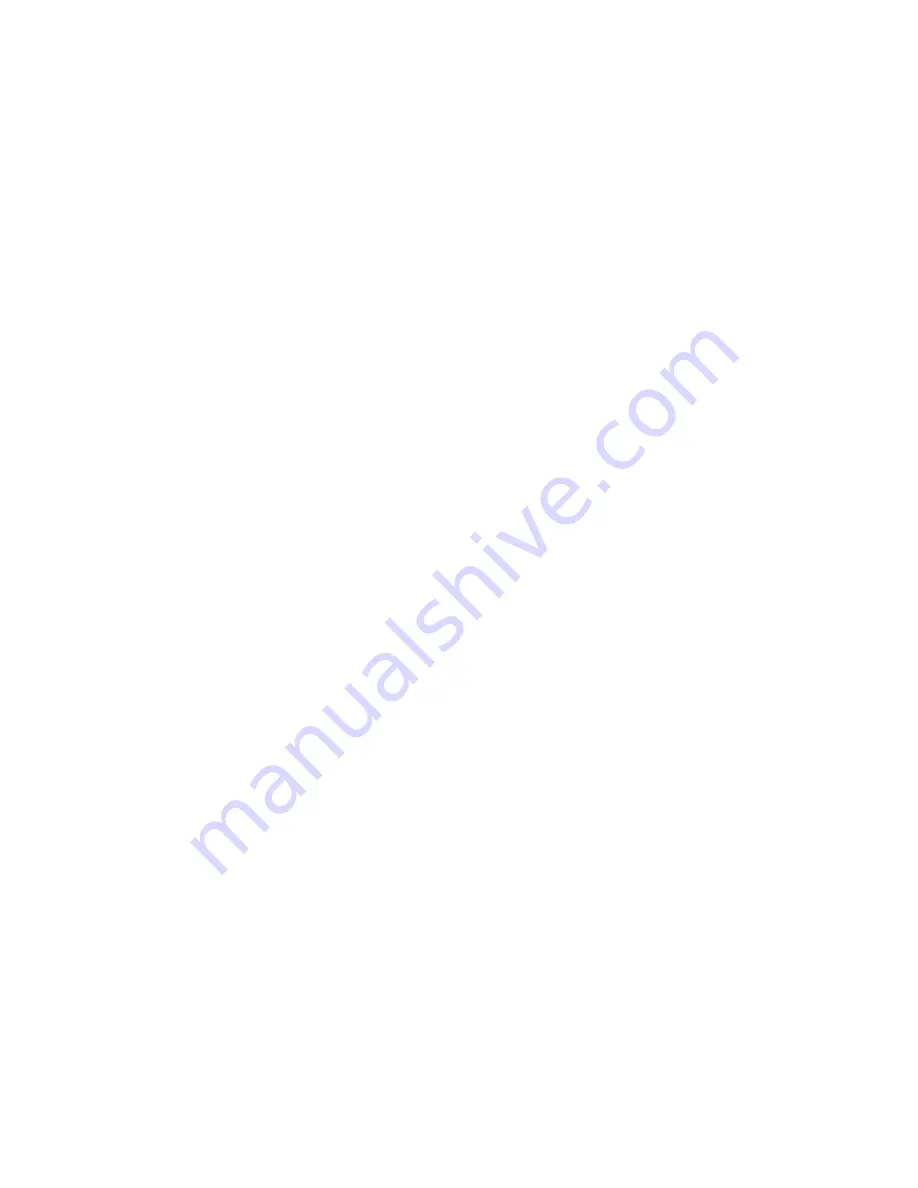
TROUBLESHOOTING GUIDE
POSSIBLE CAUSE
REMEDY
CHILLER UNIT WILL NOT START
1. Power off
1.
Check main disconnect switch
2. Main line open
2.
Check main fuses
3. Incorrect wiring
3.
Check the wiring diagram
4. Loose terminals
4.
Tighten all terminals
5. Control circuit open
5.
Check phase loss monitor, flow switch, circuit
breakers, temperature control, low ambient
thermostat, low temperature, thermostat,
remote switch, etc.
6. Time delay
6.
Wait
COMPRESSOR HUMS BUT DOES NOT START
1. Low Voltage
1a. Check at service and unit for loss
b.
Consult power company
COMPRESSOR CUTS OUT ON LOW PRESSURE SAFETY CONTROL
1. Refrigerant shortage
1.
Check for leaks -- add refrigerant
2. Restriction in liquid line
2a. Plugged strainer -- clean or replace
b. Liquid line valve partially closed — open valves fully
c. Expansion valve clogged or inoperative — clean or
replace as required
d. Solenoid valve partially open — clean or replace as
required
3. Low water flow thru cooler
3.
Check water flow thru cooler and correct as required
COMPRESSOR CYCLES ON HIGH PRESSURE CONTROL
1. Compressor discharge valve partially closed
1.
Open valve fully
2. Non-condensible gases in system
2.
Operate condenser fans with compressors off.
If condenser pressure exceeds saturated
pressure corresponding to condenser entering air
temperature, then reclaim air from the top of hot
gas vertical header coil.
3. Overcharge of R-22
3.
Reclaim refrigerant from system while in oper-
ation until head pressure reaches a normal level.
4
.
Clean the condenser
5.
Replace if necessary
6.
Check pressure control setting
CAUSES AND PREVENTION OF FREEZE-UP
CAUSES
PREVENTION
1. Improper charging
1.
Charge per manufacturer’s recommendation
2. Improperly set safety time delay
2.
Check the safety time delay low pressure control for
proper setting at the beginning of each season.
3. Improper chilled water circulation
3.
Use an ample sized cleanable strainer in the chilled
water circuit. Make certain the strainer is clean to
insure full flow and velocity of chilled water. It may
sometimes be necessary to treat the water to prevent
formation of deposits.
30
Summary of Contents for HRSC - D
Page 20: ...19 TYPICAL HRSC 150 POWER WIRING 460 3 60 COMPRESSOR MOTORS 1 2 SEE NOTE 5...
Page 21: ...20 TYPICAL HRSC 150 CONTROL WIRING Electrical Mechanical...
Page 22: ...21 TYPICAL HRSC 150 CONTROL WIRING Optional Micro Computer Controller...
Page 23: ......
Page 29: ......
Page 30: ......