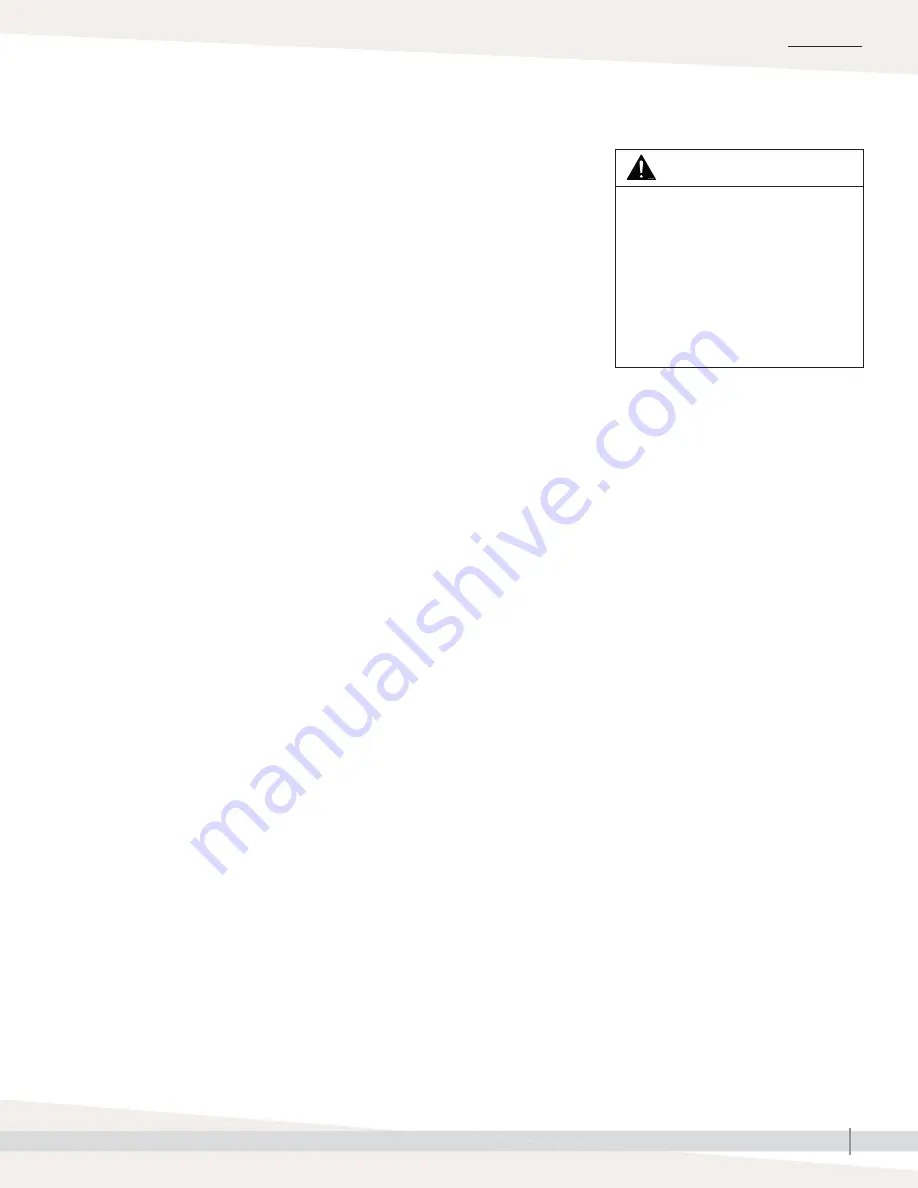
29
VAPORSTREAM INSTALLATION, OPERATION, AND MAINTENANCE MANUAL
INSTALLATION
RO/DI WATER SUPPLY PIPING
The RO/DI-water Vaporstream humidifi er controls water level with a fl oat valve.
The pipe connection is a 1/4" pipe thread (DN8), except for Vaporstream
humidifi ers in Europe, which have a 3/8" pipe thread (DN10) connection.
With the end-of-season drain option, a solenoid valve is added on the inlet
of the fl oat valve. The end-of-season feature shuts off the fi ll water supply and
drains the tank when there is no demand for humidity for 72 hours. (This
length of time is a default setting and is user-adjustable. See the
Vapor-logic
Installation and Operation Manual
for more information.)
When using nonmetallic tubing for supply water, it must be rated for 212 °F
(100 °C) minimum continuous operating temperature. DriSteem recommends
installing 3' (914 mm) of non-insulated stainless steel pipe directly off the
humidifi er (between the humidifi er and the nonmetallic tubing).
If using nonmetallic supply water tubing, DriSteem recommends making a
2" (50 mm) water seal or loop in the supply line to isolate steam from the
nonmetallic tubing. See Figure 23-1.
DriSteem recommends installing a strainer in the water supply line to prevent
clogging of the fl oat valve orifi ce. A strainer is highly recommended when
the humidifi er has the end-of-season drain option. The strainer will prevent
particulate from collecting at the solenoid valve seat.
WARNING
Fire hazard
Do not supply a RO/DI-water
Vaporstream humidifi er with tap water.
Particulates from tap supply water will
accumulate on and clog the low water
cutoff switch in the fl oat valve assembly,
causing a critical safety circuit to fail.
This can cause a dry tank fi re and
severe personal injury or death.
Water supply
Piping: