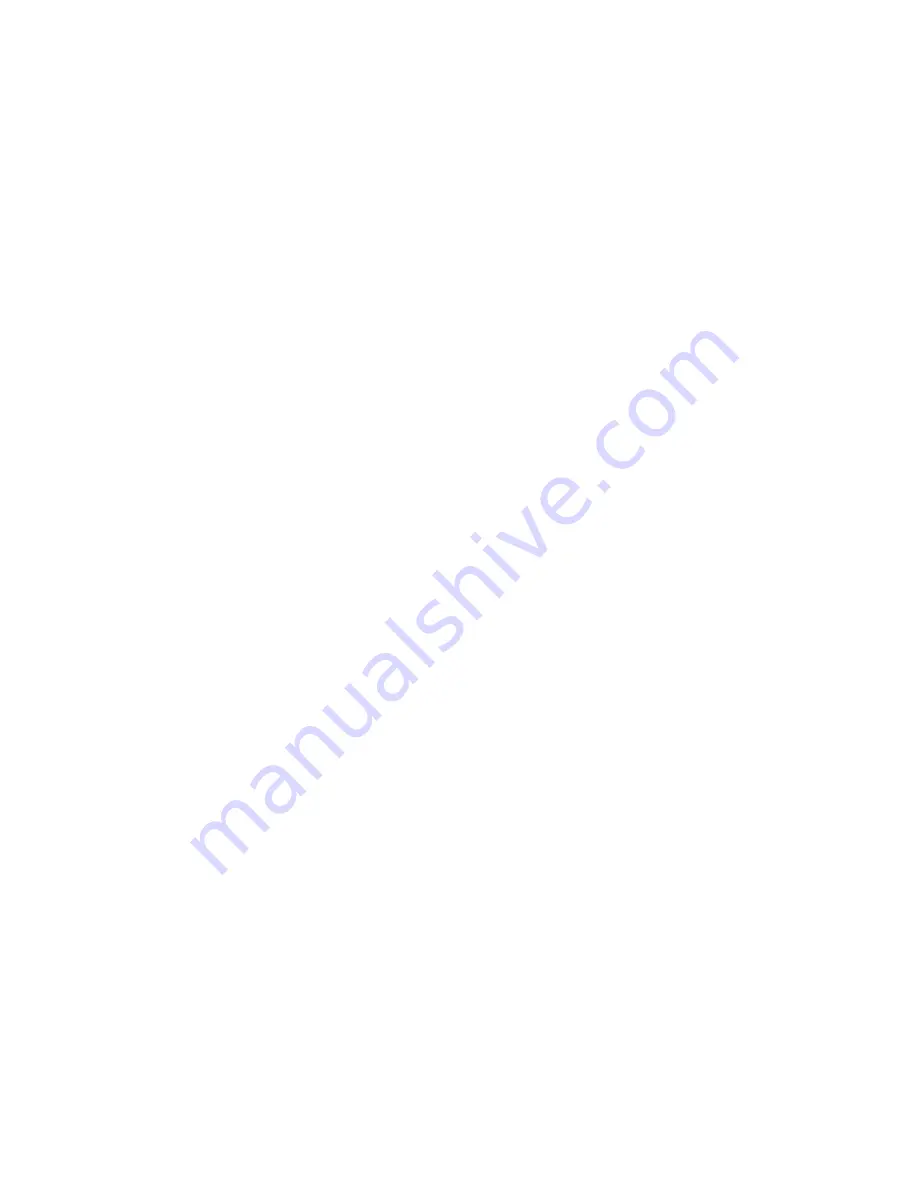
3
Crane 4000LE
07-2022
RL6002-003
Crane 4000LE Wiring, Setup and Troubleshooting Manual
In-ground Motion Assist 360 drive and speed control
Remote control enclosure
Table of Contents
14 Parameter
detail
54
14.1 Motion Assist 360 modes of operation
with "S" module
54
14.2 Basic parameters F, d and dE
54
14.3 Driving
parameters
54
15
Special functions, diagnostic detail
56
15.1 Motion Assist 360 modes of operation
with Motion Assist module
56
15.2 Special
functions
56
15.3 Diagnostics
57
16 Error
list
58
16.1 Error
indication
58
16.2 Reset column of error list (Para. 16.3)
58
16.3 Error
list
59
17 Information
61
18
Revolving door functional test
62
18.1 Revolving door functional test
62
19
Install in-ground container covers
67
19.1 Install outer section container lids
67
19.2 Install
floor
cover plates 68
Appendix A - Definitions
69
A.1
Revolving door definitions, from
ANSI/BHMA A156.27 appendix
69
Appendix B - dormakaba handheld
70
B.1 Firmware
update
70
B.2 dormakaba handheld; access parameters
72
B.3 dormakaba handheld configuration
parameters 74
B.4 dormakaba handheld driving parameters
74
B.5 dormakaba handheld special functions
75
B.6 dormakaba handheld diagnostics
76
B.7 New dormakaba handheld; language
change to English
78
Appendix C - Function modules
79
C.1 Function
modules
79
C.2 Container
module
79
C.3 Installing
function
module
80