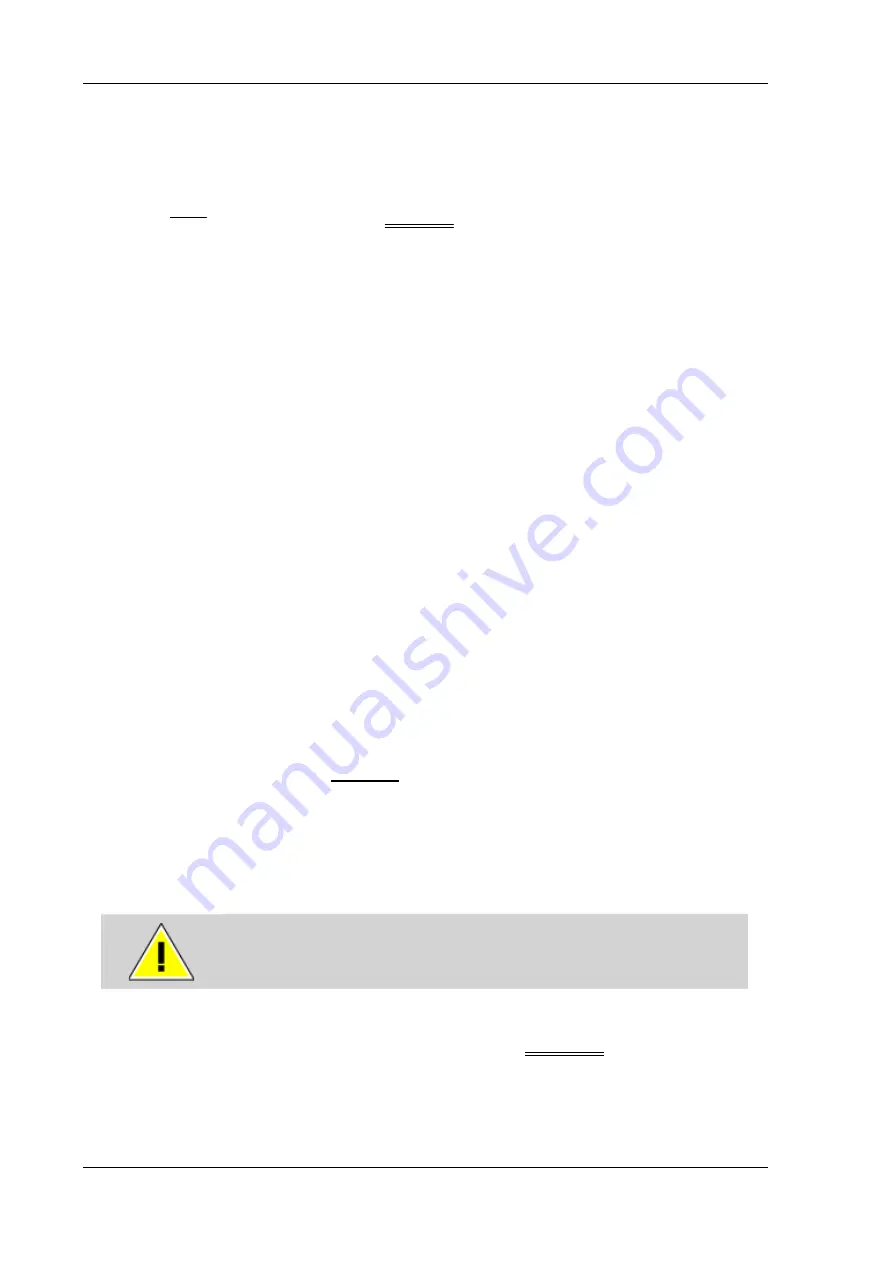
Appendix E: Mechanical dynamic loading
158
Manual
DLoG MPC 6
20.4.1.
Approximate solution for the selection of elastomer springs
Since
ω
² = c / m, we obtain the following relationship:
Where:
m
= oscillatory mass
= 5 kg
f
e
= natural frequency
= 20 Hz
c
= spring constant in N/mm
This model applies to the oscillatory mass at the device’s center of gravity. This lies
around 120 mm above the mounting surface of the group of springs and also displaced
from it. To determine the spring constant for an individual elastomer spring, the leverages
and arrangement of the springs (here in a triangle) must also be considered.
Furthermore, each of the 4 elastomer springs connected in parallel must deliver one third
of the total spring constant, i.e., 78 N/mm / 3 = 26 N/mm.
To simplify matters, of the 6 possible degrees of freedom we will only consider those with
the greatest deflection in the case of the DLoG MPC 6/110. In other words: We observe
the display as it oscillates towards or away from us (a combination of rotational and
longitudinal oscillation).
Comparative measurements for precisely the arrangement displayed in
figure 20.5
(construction of the mounting bracket, quantity and position of the elastomer springs)
show that the individual spring must be stiffer by a factor of 25 for the mathematical
model stated above to be applied.
Factors for other mountings with elastomer springs must be
calculated through testing!
As a result, this model gives a value of 26 N/mm x 22.5 = 585 N/mm for the required
single spring constant.
The next step is to look through the manufacturer’s datasheets (such as those from gmt-
gmbh.de or simrit.de) to find the right types of elastomer springs and rubber buffers.
mm
N
f
m
f
m
c
e
e
/
78
039
,
0
1000
²
4
2
2
=
⋅
⋅
≈
⋅
⋅
≅
π