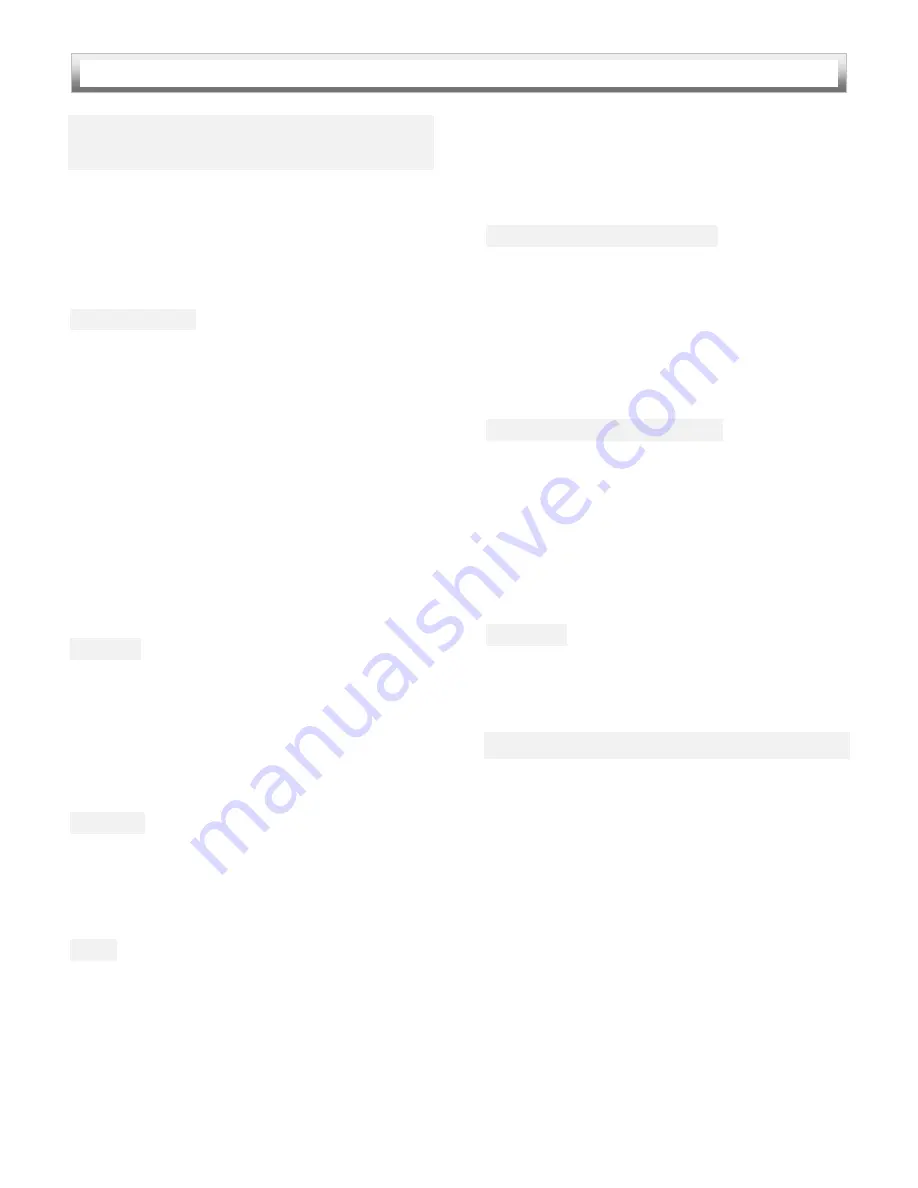
© Copyright 2003-2019 Dive Lab® Inc. All rights reserved.
This Guide is made available for the express use of owners and users of the Dive Lab XLDS systems.
This information is subject to periodic updates and changes. Always check the Dive Lab web site for the latest versions.
Document XLDS Guide – Section Four A
Revised September 30, 2019
11
SECTION FOUR A: RDC REPAIR / MAINTENANCE / OVERHAUL
General Cleaning / Inspection
Procedures
Prior to commencement of system work, a clean
area should be established and tools to be used
must be clean and free of grease and oil. Persons
performing repairs and overhauls should be
trained and experienced.
Cleaning Solution
All components of the XLDS and RDC should be
cleaned using a detergent like Simple Green
diluted, with clean filtered water at a ratio of 1
and 1/2 ounces of detergent to each gallon of
water. Regular hand washing type dish detergent,
or Non-Ionic Detergent may also be used by
mixing at a ratio of, one tea spoon per gallon of
water. All components must be thoroughly rinsed
with condition fresh water filtered to 5 micron or
less. After rinsing, take a sample of the final rinse
water in a clear container and perform a shake
test to check for suds, re-rinse components if
suds are observed during shake test.
Corrosion
Parts showing corrosion should be cleaned with
detergent and water to remove as much old
lubricant as possible, and then acid cleaned by
immersion in a 50/50 solution of white vinegar
and water for up to 4 hrs. Re-clean parts using
the detergent solution and rinse thoroughly.
Inspection
After cleaning, the parts should be inspected for
obvious
contamination
and re-cleaned
as
necessary and carefully inspected for signs of
wear and damage.
Drying
All parts should be left to air dry in a clean
controlled space, or dried using nitrogen or
divers’ air. A hair dryer set on a low heat is also an
effective way of drying parts. When parts are dry,
inspect using a bright light. Complete a final visual
inspection and if any contamination is found, the
components must be re-cleaned.
Control of Cleaned Components
All parts cleaned should be protected by sealed
airtight designated containers or individually
bagged as necessary until reinstalled in the
system. All attempts should be made to maintain
Foreign Material Exclusion (FME) of all parts and
components,
during
all
phases
of
the
repair/overhaul process.
Cleaning and Handling of O-rings
All O-rings used in the XLDS and RDC will be
cleaned using a detergent solution then
thoroughly rinsed, dried and sealed, in an
appropriate container. Once cleaned, all O-rings
should only be handled while wearing gloves. O-
rings should not be lubricated, until they are
staged, and ready to be installed into the
components.
Lubrication
Lubricant applied to O-rings and components,
must be done sparingly. The recommended
lubricant is Christo-Lube
.
Pipe Threads
Pipe thread fittings in high- and low-pressure
breathing gas systems, are often used as an
alternative to straight thread O-ring or welded
fittings due to cost, complexity, and selection.
Pipe thread fittings offer an attractive alternative
to large bend radius welded, or compression joint
systems, and can produce exceptionally strong,
reliable, compact systems.
However, shock and vibration especially in
portable systems can cause movement between
joints resulting in leaks. Unlike O-Ring fittings,