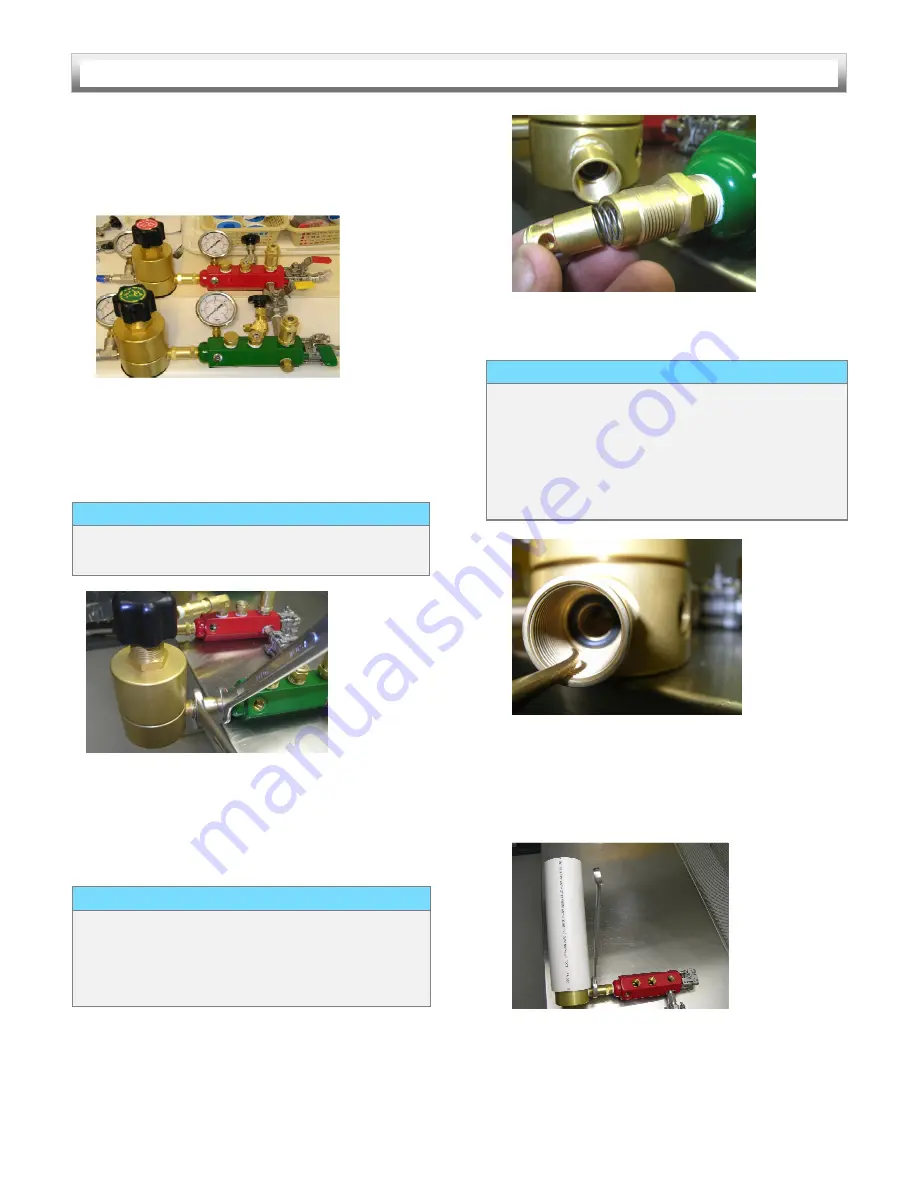
© Copyright 2003-2019 Dive Lab® Inc. All rights reserved.
This Guide is made available for the express use of owners and users of the Dive Lab XLDS systems.
This information is subject to periodic updates and changes. Always check the Dive Lab web site for the latest versions.
Document XLDS Guide – Section Four A
Revised September 30, 2019
22
SECTION FOUR A: RDC REPAIR / MAINTENANCE / OVERHAUL
3. Lift the complete two, or three diver manifold
assembly from the box as an assembly. Place
the manifold on a clean, flat, work table then
remove the hand loader knobs.
Figure 32
4. Position the regulators, so they hang over the
edge of the work bench, and using two 7/8”
wrenches, loosen and separate, the one-way
valve, by turning counter - clockwise.
Figure 33
5. Remove the spring (3), and poppet/spring
housing (2), then using the flashlight, carefully
inspect the insides of each half, for corrosion
and contamination.
Figure 34
6. Using the brass pick, remove the O-ring (5).
Figure 35
7. Using 12” long piece of 3” diameter plastic
(PVC) pipe, hold the regulator, while turning
the check valve body counter-clockwise, with
the 7/8”wrench.
Figure 36
NOTICE
Use care when separating the valve, so the
spring and poppet don’t fall free.
NOTICE
Remove the O-ring using a brass, or plastic pick
only. The use of steel picks or screw drivers
could scratch the seat, causing the valve to
leak.
NOTICE
If the body (4), spring (3), and poppet/spring
housing (2), are clean and free of corrosion,
cleaning will not be necessary, and simply
lubricating and installing the new O-ring, is all
that is required. Skip steps 7 and 8 and
continue to step 9.