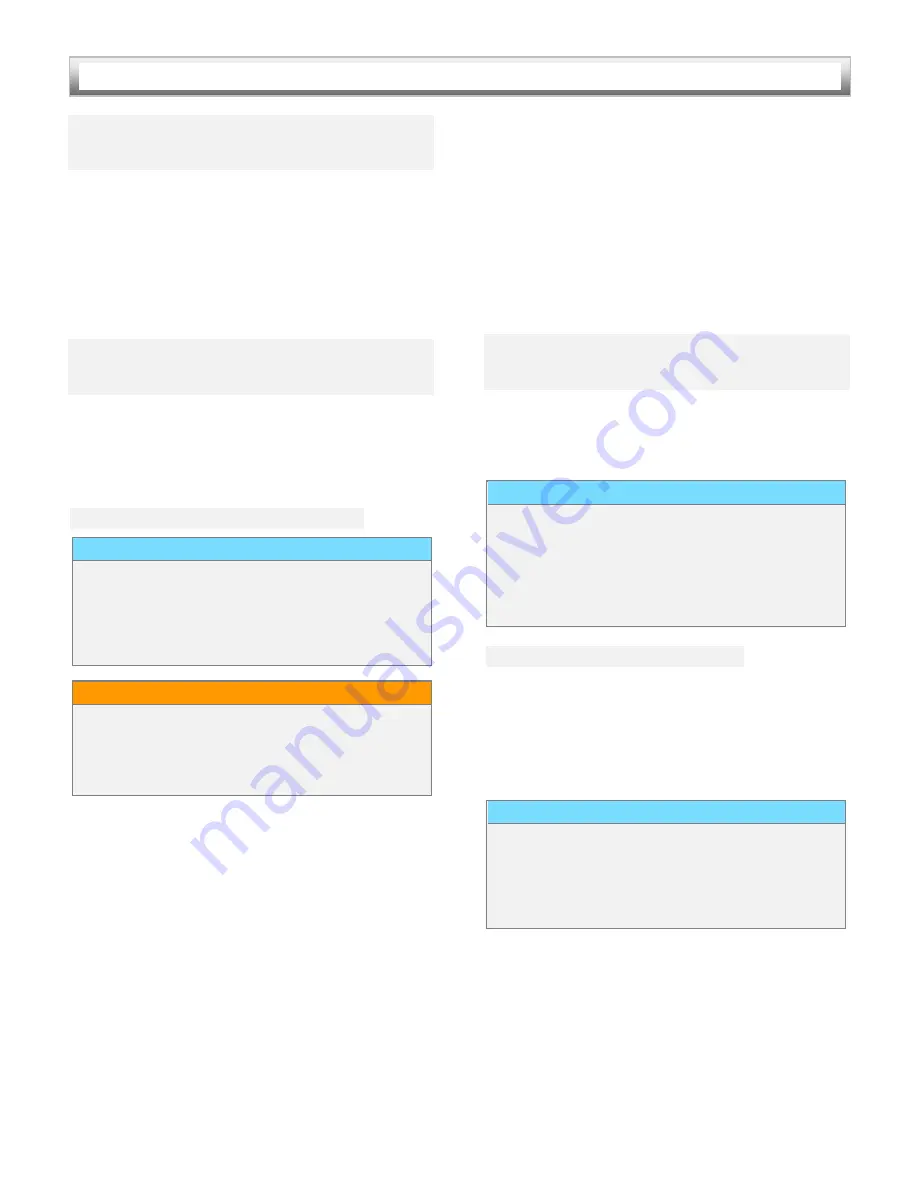
© Copyright 2003-2019 Dive Lab® Inc. All rights reserved.
This Guide is made available for the express use of owners and users of the Dive Lab XLDS systems.
This information is subject to periodic updates and changes. Always check the Dive Lab web site for the latest versions.
Document XLDS Guide – Section Four B
Revised August 20, 2019
51
SECTION FOUR B: RDC REPAIR / MAINTENANCE / OVERHAUL
ICS 300 psig Intermediate Test
Gauge Comparison
The ICS Intermediate Pressure Gauge is a 0-300
psig gauge that has a full-scale accuracy of 3% or
less. This means the maximum error could be up
to 9 psig over the full scale. However, in most
cases these model gauges are rarely more than
two to three psig off in the 100-200 psig range.
XLDS System Pressure Test
Procedure
A pressure test of the XLDS RDC with HP supply
system should be completed at least once a year
or whenever system tightness integrity is in
question.
Pressure / Joint Tightness Testing
Perform a pressure / joint tightness test of the
complete RDC and HP and LP supply systems to
the maximum system pressure normally used.
Document and use the Dive Lab RDC Pressure
Test / Joint Tightness Test Procedure A2.1A.
Perform the high pressure test using a minimum
of 3000 psig, or to the maximum intended “use”
supply pressure which could be as high as 3500
psig if using “A” yokes, up to 4350 psig using DIN
connections, and to a maximum of 5000 psig with
other properly rated fittings and supply whip
components. The low-pressure circuits for Red,
Green, and Yellow Diver’s should be tested using
a test pressure of between 350-400 psig and held
for 10 minutes, zero leakage allowed as shown on
the RDC HP and LP gauges. Document the testing
on the XLDS RAPID Deployment console Annual
Pressure /Joint Tightness Test Checklist A2.1A
sheet.
XLDS Annual Relief Valve Lift
Check
The relief valves should be set to start relieving at
a pressure of 390-400 psig as read on each of the
diver LP gauges.
Brass and Stainless Versions:
1. Attach the HP supply to the circuits being tested.
Slowly bring up pressure to the manifold by
rotating the regulator adjustment knob clockwise
(in), until the LP gauge reads the desired relief
pressure setting.
2a.Brass Circle Seal Relief: For the Brass Valve, If the
relief needs to be adjusted proceed as follows, for
the “Brass Relief”, loosen the cap (9) using a 1”
wrench, then adjust the housing (8) with a 5/16
NOTICE
Prior to performing the pressure/joint tightness
tests, ensure all the RDC gauges have been
compared to master gauges of known accuracy.
Ensure comparison has been properly documented
using comparison test sheets.
WARNING
When performing any type of pressure tests
eye protection should be worn at all time.
Testing should be done in a clear secure area
occupied by the test personnel only.
NOTICE
Early RDC’s (pre-2011) used brass Circle Seal® relief
valves. XLDS systems after 2011 all have stainless
steel HyLock® angle relief valve. Both models adjust
in a similar fashion. Lift testing the reliefs will not
damage the system and can be done on a routine
basis if desired.
NOTICE
Quite often if a relief has not been lifted for a long
period, the relief may stick, and can go as high as
twenty psig over the set pressure before it lifts.
Lightly tapping on the top of the relief will often jog
it free.