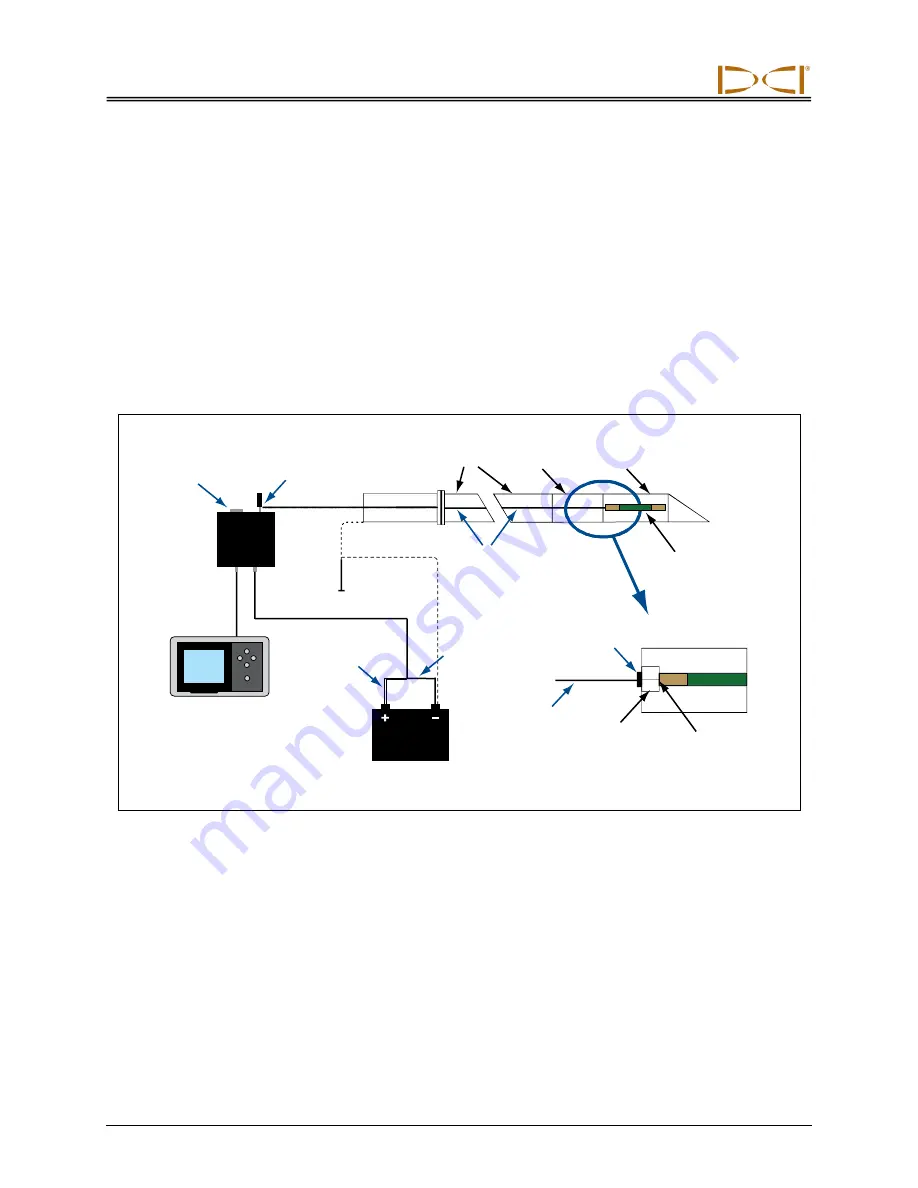
Operating Instructions
28
DigiTrak
®
F5
®
SST
®
Operator’s Manual
16. Connect SST Equipment to the Drill
You are now ready to connect the 10-gauge white wire from the SST transmitter
to the monel’s 10-gauge
wire with a butt splice and heat shrink. The monel is a non-mag drill pipe that measures approximately 15
ft (4.6 m) in length and must be used between the non-mag housing and the regular drill pipe. Once this
wire connection is made, the housing can be threaded onto the monel while carefully pulling the slack in
the wire to ensure that the wire does not get caught in the threads. You will continue to thread the wireline
through the drill rods in the same manner, carefully making the connection for each drill pipe.
The following diagram shows how the SST system components are connected.
A ground wire needs to
be installed between the negative terminal of the free-standing battery and a ground point on the drill rig.
The ground point can be the negative terminal on the
drill rig’s battery or a metal contact point on the drill
rig or drill stem.
Connecting SST System Components
The compression fitting shown in the diagram is a non-DCI part required to seal the transmitter from the
drilling fluid. Contact a drill or tooling manufacturer for information on compression fittings.
With the SST transmitter properly grounded through the drill housing, connect the wire from the trans-
mitter and now exiting the drill string to the power post on the cable box. Rotate the knob on the power
post counterclockwise until the hole in the post is exposed. Insert the stripped portion of the wire into the
hole and gently tighten the knob.
Connect the cable box to the serial port on the laptop computer using the serial cable provided with the
system. The laptop can be positioned as far as 50 ft (15 m) from the drill.
SST
transmitter
End plug
Non-mag
housing
Monel
Drill rods
Battery
(12
–28V)
Serial port
to computer
10-gauge
white wire
Black wire
White wire
SST remote display
Power post
10-gauge
wire
Cable
box
Housing to transmitter
base is negative contact
for grounding
Compression
fitting
Ground