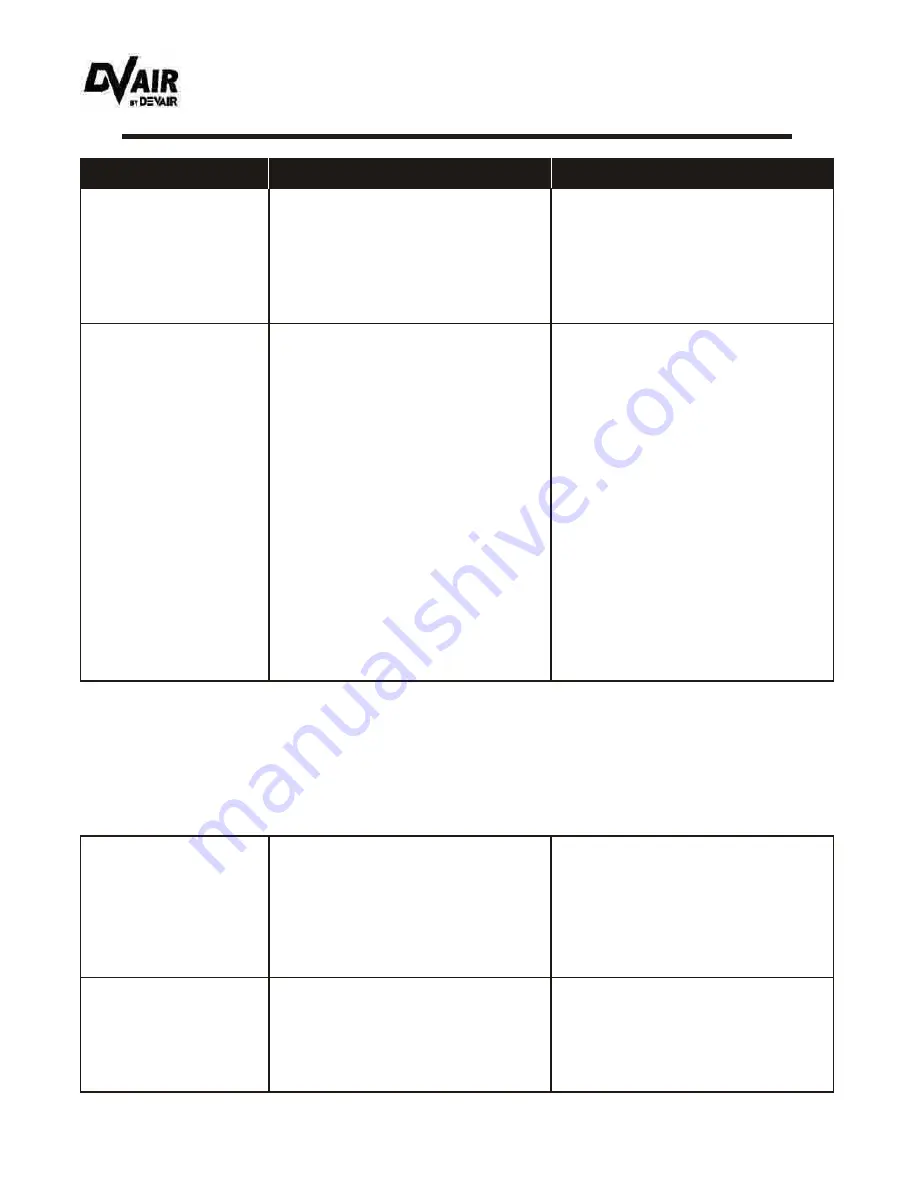
D. Compressor Over-
heating
1.
Undersized unit for air requirements.
2.
Compressor too close to building wall.
3.
Pump rotating wrong way.
4.
Air leaks in air lines.
5.
Remote air intake piping restricted or
too small.
6.
Restricted air filter.
7.
Improper level and/or grade of oil in
the crankcase.
8.
Worn or carbonned valves.
9.
Broken valve discs or springs, loose
valve assemblies, or badly worn or
damaged valve seats.
10. Carbonned aftercooler tube or check
valve.
1.
Maximum pump operating time
should be 75% to 80%, which relates to
45 minutes per hour.
2.
Relocate compressor. See 'Location of
the Unit' (page 7) in this bulletin.
3.
Check rotation of the flywheel;
rotation must be clockwise when
facing the unit. Reversing the leads at
the motor will correct.
4.
Check for source of leak and correct.
5.
Clean or replace piping. Contact
Devair or your local distributor or
service centre.
6.
Clean or replace air filter.
7.
See 'Lubrication' (page 8) in this bulletin,
or contact your local Distributor or
Service Centre.
8.
Clean or replace as required.
9.
Replace components as required.
10. Clean or replace.
Suggested Correction
Condition
Cause
C. Reduced Air Delivery or
Insufficient Air
1.
Restricted air intake piping or filter.
2.
Loose 'V' belt.
3.
Pump valves or tank check valve
leaking,sticking, or carbonned-up.
4.
Air leaks in system.
5.
Undersized unit for air requirements.
1.
Clean or replace.
2.
Tighten as required. Do not over-
tighten.
3.
Clean, repair, or replace.
4.
Fix leaks.
5.
Contact local distributor or service
centre for suggestions.
Should the items as noted in 'D' not provide any insight as to why the unit is overheating, the problem
may lie in the environment in which the unit is operating. A compressor unit located in a warm room
may show signs of overheating.
The unit should either be moved to a cooler environment, or the existing environment modified. Wall
louvers or stationary fans may improve conditions. Contact your local Distributor or Service Centre
for further information.
E. 'V' Belt(s) roll off the
Flywheel or Motor Pulley
1.
Flywheel and motor pulley not
aligned properly.
2.
In the case where 2 belts are used,
belts may not be 'matched set'.
3.
A nick or tear on the edge of the belt.
4.
Belts do not match the flywheel
groove (such as 'A' or 'B' section).
1.
Align using a straight edge.
2.
Purchase new set of matched belts.
3.
Purchase new set of matched belts.
4.
Purchase new set of matched belts,
paying close attention to 'section'
requirements.
F. Flywheel or motor pulley
wobbles or comes loose.
1.
Clamping bolt not tight enough on
flywheel.
2.
Set screw on motor pulley not tight
enough.
1.
Tighten as required.
2.
Take existing set screw out purchase
new one. Set screws have a lock-tite
coating, and can only be adjusted once.
Trouble-Shooting Guide (cont’d)
- 21 -
HDI-01
Mar ‘07
Distributed by: CENTRAIR Air Systems & Supplies, 68 Hooper Rd., Unit 5, Barrie, ON L4N 8Z9
Phone: 705-722-5747 Fax: 705-722-5458 [email protected] www.centrair.ca
All manuals and user guides at all-guides.com
all-guides.com